해외 프로젝트에서의 동다짐 공법 설계 및 시공관리
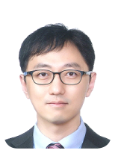
김 규 선
삼성물산㈜ 건설부문(kyusun@empas.com)
1. 개요
동다짐(dynamic compaction) 공법은 파운더(pounder)로 지반에 충격하중을 가해서 지반내 입자 재배열 효과를 통해 지반을 다지는 방법으로, 공법의 시공성과 경제성에 대한 장점으로 사질지반 개량에 널리 적용되는 공법이다. 지반조건으로 인해 쇄석으로 치환하는 경우에는 동치환(dynamic replacement) 공법이라고 한다. 동다짐 개량시 흙의 종류와 가해진 타격에너지의 규모에 따라 각각 다른 지반거동을 나타내기 때문에, 지역적 특성을 고려한 시공경험과 지반거동에 대한 종합적인 이해가 효과적인 동다짐을 수행하기 위한 핵심요소이다. 공법이 단순하고 간편해서 광범위하게 활용되고 있으나, 경험적 요소가 많기 때문에 시공중 거동을 정확히 예측하기 어려운 단점이 있다. 따라서, 설계단계에서 수립한 시공계획을 반드시 현장 Calibration한 후 수정사항을 본공사에 반영하여 적용해야 한다. 동다짐은 파운더의 타격으로 유발되는 주변지반의 히빙 및 진동으로 인해 공법을 적용할 수 있는 부지가 한정적이기 때문에 점차 사용빈도가 감소하는 추세이나, 두께 10m 내외의 느슨한 사질지반이 분포하는 지역이 많은 중동지역 공사에서는 현재에도 활발히 적용되고 있으며, 최우선적으로 고려되고 있는 중요한 지반개량공법이기도 하다.
국내에서의 동다짐 관련 연구는 1987년부터 현재까지 약 40여편의 석박사 학위논문을 통하여 다양하게 진행되어온 것을 확인할 수 있다. 공법의 특성상 다양한 지반조건에 대한 현장기반의 연구가 꾸준히 진행됐는데, 이는 동다짐의 경험적인 요소들에 대한 규명이 아직 필요하기 때문인 것으로 생각된다. 반면에, 실무에서는 시공사례 기반으로 연구결과를 정리한 미국 FHWA 매뉴얼과 몇몇 전문서에서 인용하고 있는 일본 시공사례 기반의 가이드라인에서 크게 벗어나지 않고 있다. 향후에는 국내·외의 다양한 연구 및 시공경험에 대한 체계적인 데이터 수집과 분석결과를 이용한 가이드라인 업데이트를 통해, 귀중한 연구결과 및 시공사례가 사장되지 않도록 설계실무와 시공계획에 반영하는 작업도 필요하다고 생각된다.
국내의 실무에서는 앞서 언급한 일본 시공사례(ΔN치~단위체적당 소요에너지)를 참고하여 타격계획을 수립하고 있는데, 중동지역 프로젝트에서는 상대밀도를 평가하는 CPT qc 다짐품질 기준을 제시하는 경우가 종종 있다. 이 경우에 국내 가이드라인을 참고하여 동다짐 설계를 수행하게 되면 현지의 시공경험과는 다소 상이한 결과를 도출할 수도 있다. 본 고에서는 해외 프로젝트 수행시의 동다짐 설계 및 시공관리를 위해, CPT qc 기반의 설계 및 시공계획을 수립하기 위한 검토절차를 살펴보고, 동다짐 설계 예제 및 실제 적용사례를 간단히 소개하고자 한다.
2. 동다짐 공법
동다짐은 1970년대에 Menard에 의해 체계화 되었다. Menard는 포화 세립토를 다지는 공법을 제시하면서 “동압밀(Dynamic Consolidation)”이라 정의하고, 점토, 실트 또는 모래를 함유한 점토를 압밀시키기 위한 공법으로 제안하였는데, 이러한 이유로 동다짐 혹은 동압밀 이라는 용어를 혼용하기도 한다. 동다짐은 일반적으로 20tf 내외의 강재(또는 콘크리트) 파운더를 100~200tf 규모의 크롤러 크레인을 이용하여 15~25m 높이에서 자유낙하시켜 지반을 개량한다(그림 1). 사질지반에 적용하는 것이 일반적이며, 쓰레기매립지 또는 잡석성토 지반에도 적용이 가능하다. 동다짐은 기본적으로 (1) 침하량 저감, (2) 지반강도 및 지지력 증가, (3) 액상화 방지를 위해 적용되며, 일반적으로 최대 개량심도 12m, 지지력 300kPa, 침하량 10~20mm 확보를 목표로 한다.
동다짐은 통상의 롤러다짐에 비해 1회 타격에너지가 압도적으로 크다. 롤러다짐시에는 지표면 부근이 먼저 경화되어 에너지가 심부에 전달되기 어려운 경우도 발생하나, 동다짐은 깊은 심도부터 순차적으로 상부까지 개량하는 장점이 있다. 또한, 모래, 자갈, 세립토, 폐기물 등의 다양한 지반조건에 적용이 가능하며, 지반내에 암괴 등의 장애물이 있어도 타격에너지의 손실이 발생하기는 하지만 시공은 가능하다. 지반조사에서 파악이 어려운 지반의 불균일성을 시공중에 유연하게 대처 가능하고, 부지 전반에 대한 개량효과를 확실하게 확보할 수 있는 것이 공법의 장점이다.
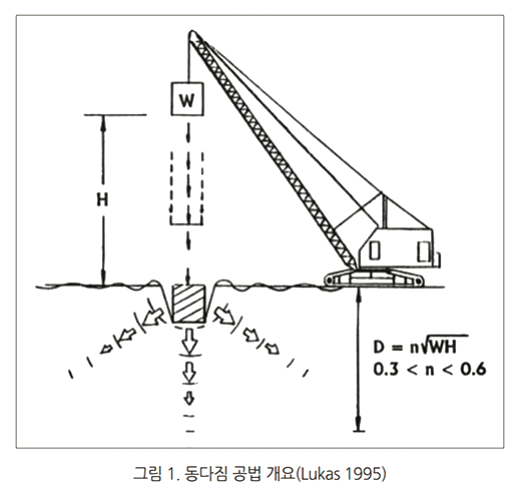
3. 동다짐 기본원리
동다짐에 의한 진동은 P파, S파, R파가 복합적으로 발생하는데, 압축파인 P파는 과잉간극수압을 발생시켜 입자를 이완시키고, 전단파인 S파는 입자를 조밀하게 재배열한다. 표면파인 R파는 지표부근에서 전파되며 가장 많은 에너지가 전달된다(그림 2). 동다짐 개량심도는 타격에 사용되는 파운더의 무게와 낙하고에 따른 타격에너지로 결정된다. 개량심도와 타격 1회당 에너지의 관계는 식 (1)과 같이 표현할 수 있다(Menard 1975).

여기서, D: 개량심도(m), W: 파운더 중량(tf), H: 낙하고(m), n: 개량심도계수(지반종류 및 사례에 따라 0.3~1.0)를 나타낸다. 흙의 종류에 따라 세분화하면 사질토 n=0.4~0.6, 쇄석 및 자갈 n=0.5~0.7, 폐기물 n=0.3~0.5의 값을 나타낸다. 각각의 계수는 포화지반보다는 건조지반에서 비교적 일치하는 결과를 나타낸다(이봉직 등, 2005). 연구자별 제안치로는 Leonards(1980) n=0.5, Menard와 Broise(1975) n=1.0, Lukas(1980) n=0.65~0.8, Michell과 Katti(1981) n=0.4~0.7, Mayne 등(1984) n=0.5 이다.
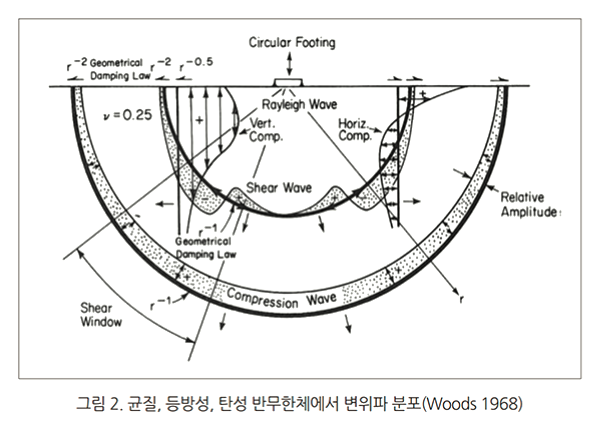
4. 동다짐 대상토질 및 유효개량심도
동다짐에 적합한 토질은 입도분포로 개략 판단이 가능하다. 타격이 진행되는 동안 함수비 변화에 따라 흙이 다져지는데, 대부분의 현장에서는 지하수위 하부 포화지반을 다지게 되므로, 간극수압 소산이 잘되는 투수성이 높은 지반에서 효과적인 다짐을 수행할 수 있다. 그림 3은 흙의 입도분포에 따라 흙의 투수성을 3개의 Zone으로 구분하고 있다. 동다짐은 포화도가 낮고, 투수성이 높으며, 배수성이 좋은 Zone 1에 해당하는 흙에 가장 효과적이다.
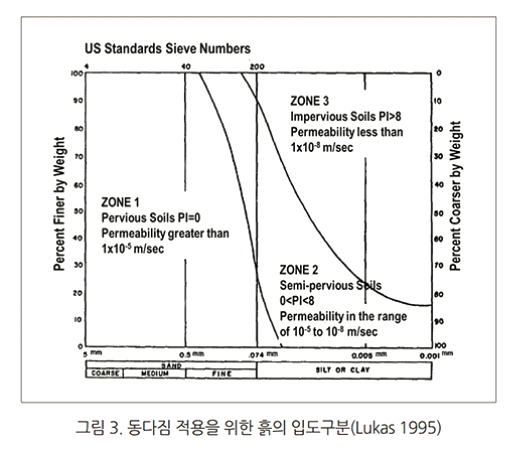
동다짐 개량심도는 식 (1)에서 정의한 파운더 중량(W) 및 낙하고(H)의 영향 외에, 투수성, 지반상태, 장비종류, 파운더 접지압, 케이블 마찰손실, 지하수위 등 복합적인 인자의 영향을 받기 때문에, 단순히 대상지층의 종류만으로 분류할 경우에는 효과적인 예측이 어려울 수 있다. 특히 다층지반을 하나의 지층으로 가정할 경우에는 예측치와 다른 개량효과가 나타날 가능성이 크다. Mayne 등(1984)은 약 120개의 다양한 현장에서 수집된 동다짐 측정치를 토대로 타격에너지와 개량심도의 관계에 대한 연구결과를 정리하였다. 동다짐 타격에너지(W×H)에 따라 다양한 개량심도 분포를 나타내고 있는데, 유효개량심도는 대체로 5~10m에 집중되고 있음을 알 수 있다(그림 4).
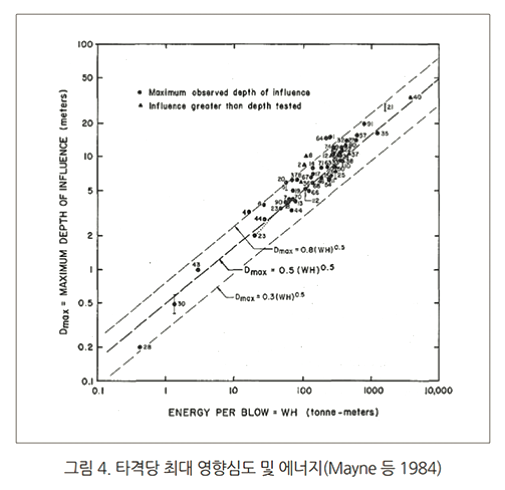
그림 5에서 나타내고 있는 타격에너지에 따른 개량심도 도표에 따르면, 타격에너지와 흙의 강성이 증가함에 따라 개량심도가 저감되는 것을 알 수 있다. 예를 들어, 느슨하거나 취약한 토질에서 W×H≒100tf·m의 타격에너지는 5~7m의 개량심도를 나타내지만, 4배 큰 에너지를 가하더라도 개량심도는 7~12m로 소폭 증가하며, 견고하고 밀실한 토질에서는 W×H≒400tf·m을 가하더라도 5~8m로 저감된 개량심도를 나타낸다.식 (1)과 그림 5에 나타낸 바와 같이, 개량심도(D)는 타격에너지(W×H)의 함수로 평가될 수 있다. 통상적인 동다짐 장비조합(파운더 및 낙하고)을 적용하였을 때의 개량심도가 10m 내외가 될 것으로 판단되며, 그 이상의 개량심도가 요구될 경우에는 타격에너지를 큰 폭으로 증가시켜야 하므로 그에 대한 효율성을 고려해야 한다. 식 (1)은 개량심도계수 n만 사용하나, 경우에 따라 식 (2)에서 제시하는 바와 같이, 낙하방법에 따른 수정계수 C와 흙의 종류에 따른 수정계수 δ로 구분하여 사용하기도 한다.

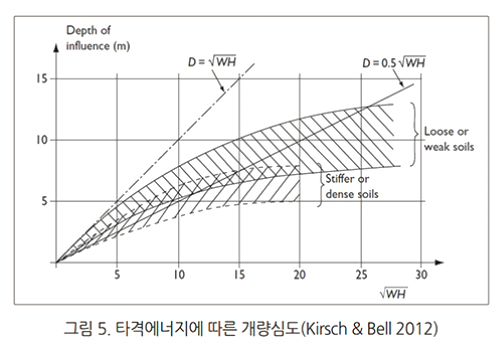
여기서, D: 개량심도(m), W: 파운더 중량(tf), H: 낙하고(m), C: 낙하방법에 따른 수정계수(표 1 참조), δ: 흙의 종류에 다른 수정계수(붕괴성 토사/매립토사=0.9, 사질토=0.4~0.6)

표 2에는 문헌에서 제시하는 개량심도 가이드라인을 정리하였다. Luongo(1992)는 흙의 종류(Zone 1(투수성)~Zone 3(불투수성), 그림 3 참조)에 따른 개량심도를 제시하고 있다. 기존 사례에 따르면, 최대 개량심도는 12m 정도까지 가능하지만 흙의 종류에 따라 10m 이내로 감소될 수도 있음을 유의해야 한다.
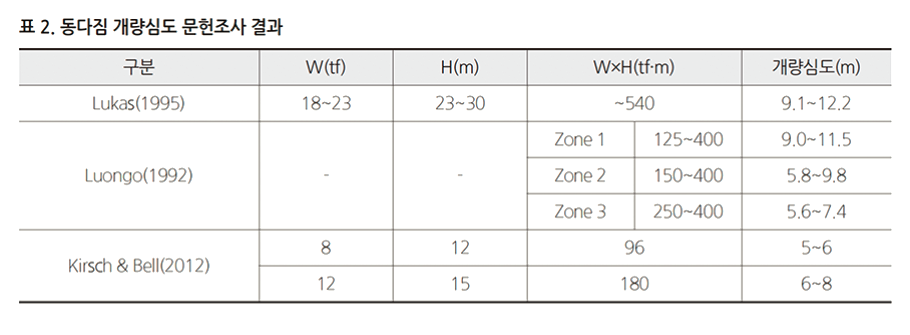
5. 동다짐 설계 및 시공관리
5.1 설계
(1) 공법 선정 및 토질 검토
지반개량공법 선정을 위한 검토방법으로, 대상 토사의 세립분 함유량(Fine Contents, FC)을 이용한 1차적인 적용공법 검토 방법은 다음과 같다.
- FC < 15% 인 경우, 진동다짐(Vibro Compaction) 적용,
- FC < 30% 인 경우, 동다짐(Dynamic Compaction) 적용,
- FC > 30% 인 경우, 동치환(Dynamic Replacement) 적용 또는 개량심도>5m 인 경우 스톤컬럼 적용을 고려한다.
FC < 30%로 동다짐 공법의 적용성이 확인된 후, 그림 3에서 나타낸 흙의 종류에 따른 입도분포 구분(Zone 1 or Zone 2)을 통하여 흙의 종류를 판정한다.
(2) 개량심도(D)와 타격에너지(W×H)
동다짐은 Phase 1으로 심부를 개량하고 Phase가 거듭되면서 순차적으로 상부를 개량해서 최종적으로 Ironing으로 지표를 개량한다. 식 (1)과 (2)에서 나타낸 바와 같이, 개량심도는 파운더 중량과 낙하고 및 토질조건을 종합적으로 고려하여 결정할 수 있다. 따라서, 동다짐 설계의 주된 내용은 파운더 중량(W)과 낙하고(H)를 결정한 후, 타격간격(s)과 타격횟수(N)를 고려하여 타격패턴을 결정하는 것이다.
(3) 타격간격(s)
타격간격(s)은 지반조건에 따라 달라지게 되며, 사질지반에는 통상 개량심도(D) 정도의 간격으로 시공하고, 다음 Phase에서는 타격지점(print) 사이 지반을 타격한다. 폐기물 지반, 점토를 함유한 토층에서는 일반적으로 0.5D~1.0D 범위에서 타격간격을 결정한다. 타격간격은 타격에너지의 효율성을 충분히 발휘할 수 있도록 고려하고, 타격이 진행되는 동안 주변지반의 히빙을 최소화하여 개량효율을 높일 수 있도록 계획해야 한다. 첫번째 그리드를 Phase 1, 그 다음 중간 타격지점을 따라 구성된 두번째 그리드를 타격하는 것을 Phase 2라고 하는데, 이와 같이 각 Phase가 거듭됨에 따라 타격지점 간격을 좁힐 수 있다.
(4) 단위면적당 소요에너지(E) 추정
타격에너지(W×H)는 개량심도(D)에 많은 영향을 미친다. 타격에너지가 너무 클 경우에는 동다짐에 의한 지반진동이 커져서 지반교란이 발생하고, 너무 작을 경우에는 개량효율이 저하되므로, 적절한 타격에너지를 결정하는 것이 중요하다. 단위면적당 소요에너지(E)는 시공실적에 대한 경험적인 자료를 토대로 식 (3)과 같이 산정할 수 있다. 여기서, 단위체적당 소요에너지(Ev)는 표 3의 가이드라인을 기준으로 개략치를 산정할 수있는데, 국내 실무에서는 일본의 시공사례에 기반한 ΔN치-단위체적당 소요에너지(tf·m/m3)의 상관관계를 자주 이용한다(그림 6). Mayne 등(1984)은 여러 나라의 다양한 조건에서의 시공사례를 기반으로 동다짐 개량후의 지반상태에 대한 현장시험결과(CPT & SPT)와 단위면적당 소요에너지(E)에 대한 상관관계를 제시하였다(그림 7).

여기서, E=단위면적당 소요에너지(tf·m/m2), D=개량심도(m), Ev=단위체적당 소요에너지(tf·m/m3)
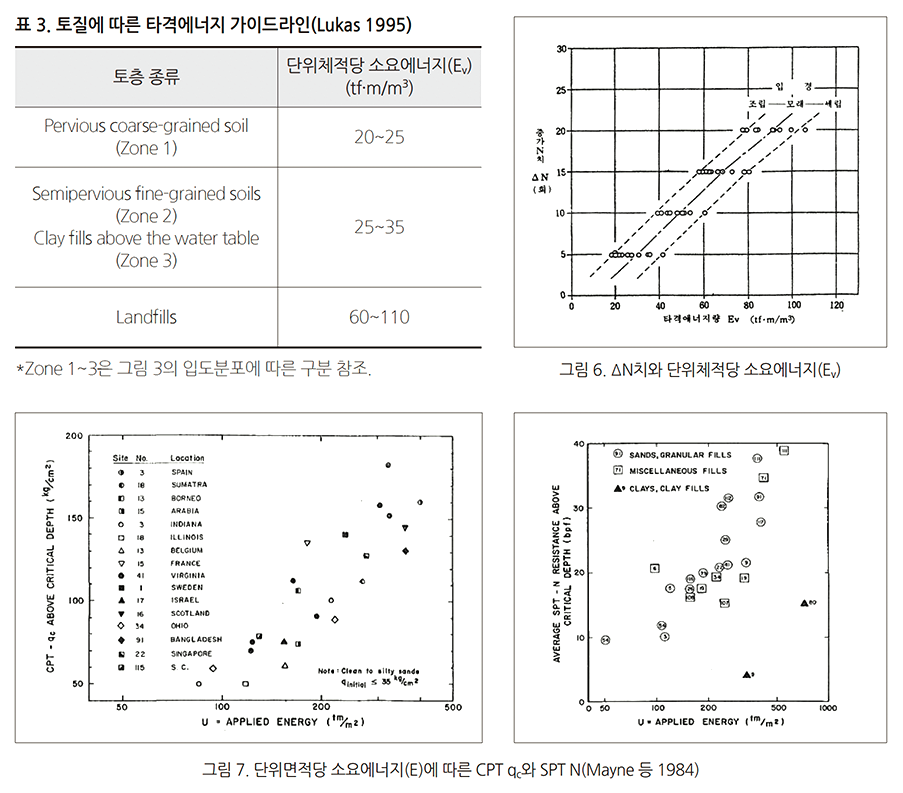
(5) 타격횟수(N) 결정
각 타격지점에서의 타격횟수(N)는 타격에너지(W×H), 단위면적당 소요에너지(E), Phase 수 등에 의해 종합적으로 결정된다. 타격에너지와 타격횟수의 곱이 총 타격에너지를 의미하며, 이를 작용면적으로 나눈 것이 단위면적당 소요에너지이므로, 타격에너지가 단위면적당 소요에너지 이상이 될 수 있도록 타격횟수를 결정해야 한다. 각 시공단계에 따라 타격횟수는 식(4)로 계산한다. 심부 개량효과가 중요한 현장에서는 초기단계에 타격에너지를 집중하여 배분하고, 시공성 및 전층의 개량을 중요시 할 때는 중간에 집중배분하는 것이 일반적이다. 특히, 표층지반이 불량한 경우에는 최초에는 시공성에 중점을 두어 배치하고, 그 후 하부의 개량효과를 중시한 타격에너지량을 배분해야 한다.

여기서, N=1타격점당 타격횟수, E=단위면적당 소요에너지(tf·m/m2), s=타격간격(m), W=파운더 중량(tf), H=낙하고(m)
5.2 동다짐 시공
동다짐 시공시 유의사항을 요약하면 다음과 같다.
(1) 지표에 세립토가 존재하거나 지하수위가 높은 경우에는 크롤러 크레인의 안정성 확보와 타격효율 저하 방지를 위해 양질토를 1.5~2.0m 두께로 포설후 작업한다.
(2) 타격으로 인한 진동 및 히빙을 고려하여 구조물에서 안전거리를 확보하여 이격시공하며, 사전에 진동영향 평가(Vibration Monitoring, VM) 및 히빙 및 관입영향 시험(Heave and Penetration Test, HPT)을 수행해야 한다.
(3) 큰 에너지의 일시 타격에 의한 지반의 소성유동 우려가 있는 토질의 경우에는 분할 타격계획을 수립한다.
(4) 세립토 타격시 과잉간극수압 소산을 위한 방치기간을 확보한다. 과잉간극수압 소산전에 추가 타격할 경우에는 다짐효과는 저하되고 소성변형만 발생하기 때문이다.
(5) 파운더 타격으로 인해 생성되는 관입부(Crater)가 깊이 패이지 않도록 시공관리한다. 타격후 파운더 인양과정에서의 마찰에 의한 케이블 부하로 인해 안전사고의 우려가 있기 때문이다. 타격전 0.6~1.0m 정도의 사질토 포설을 고려할 수 있으며, 관입깊이가 파운더의 높이를 초과할 경우는 채움작업 또는 타격중지 등의 대책이 필요하다.
5.3 동다짐 시공후 품질확인
각 구간에서의 시공후 개량효과에 대해, 프로젝트 기준의 만족여부를 확인하기 위해 품질확인 시험을 실시한다. CPT 등의 현장시험을 이용할 수 있으며, CPT 관입실패로 인해 시험이 불가할 경우, 발주처 협의후 PMT(Pressuremeter Test), SPT(Standard Penetration Test), ZLT(Zone Load Test) 등의 시험으로 대체할 수 있다.
6. 동다짐 설계 및 실시공 사례
6.1 설계 예제
다음은 동다짐 설계를 위한 예제를 나타내었다. 그림 8에 제시한 가상의 지반조건 및 동다짐 장비에 대해 개량목표(7m 개량심도에 대해 CPT qc=12MPa, SPT N=24 이상 확보)를 만족하기 위한 동다짐 시공계획 수립과정을 예제로 나타내면 다음과 같다.
(1) 개량 토층 및 심도를 고려한 낙하고 설정
n=0.5, W=15tf 일 때, 목표 개량심도 7m를 만족하기 위한 낙하고 H=15m( >13.1m)
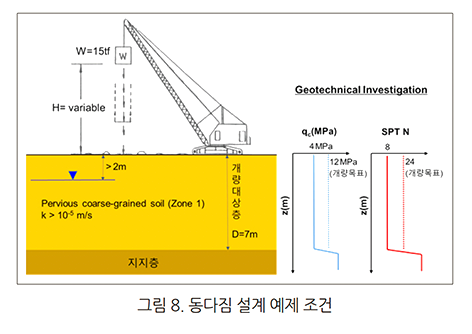
(2) 단위면적당 소요에너지(E) 결정
대상 토질조건(Pervious coarse-grained soil, Zone 1)에 적합한 단위체적당 소요에너지(표 3)는 20~25tf·m/m3으로 예상되므로, Ev=25tf·m/m3을 설계치로 채택하여 개량심도(D=7m)를 고려하면 E=175tf·m/m2임. CPT 그래프(그림 9a)를 이용하여 산정하면 E=180tf·m/m2, SPT 그래프(그림 9b)를 이용하면 E=170tf·m/m2 이므로, 보수적인 수치인 E=180tf·m/m2을 동다짐 설계시의 단위면적당 소요에너지로 채택함.
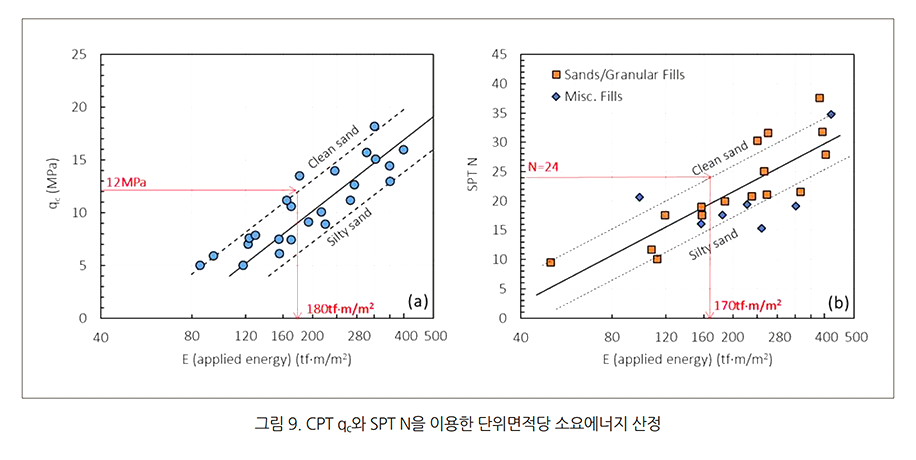
(3) 다짐패턴 결정
① Main Phase(Grid 7m×7m) 2회 + Ironing(Grid 2m×2m) 1회 다짐 결정
② Ironing Phase: W = 15tf, H=10m, 2회 타격 결정
단위면적당 소요에너지 = 15tf×10m×2 blows/(2m×2m) = 75 tf·m/m2
③ Main Phase 단위면적당 소요에너지 =180-75 = 105 tf·m/m2
④ Main Phase(Grid 7m×7m) 총 소요에너지 = 5,145 tf·m
⑤ Main Phase 총 타격횟수: W=15tf, H=15m로 타격시 필요 타격횟수 = 23회(Phase 1=13회, Phase 2 = 10회로 구분하여 계획)
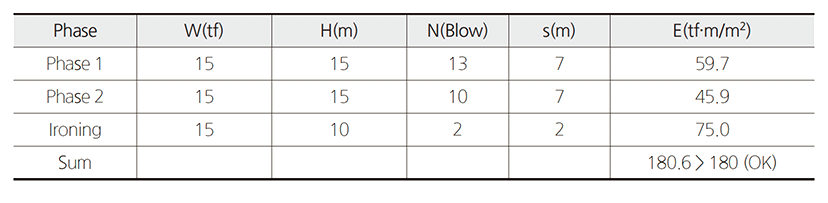
6.2 실시공 사례
다음은 중동지역에서 동다짐을 적용하여 시공한 실제 사례를 소개한다. 동다짐 본 시공전 동다짐 Calibration을 수행하는 시험시공을 통해 동다짐 시공계획의 적정성을 검증하였다. 동다짐 Calibration을 위한 작업순서는 다음과 같다.
(1) 작업 플랫폼 준비
(2) 기준점 및 시험위치 설정
(3) 시험시공 위치에서 사전 지반조사(Pre-CPT) 실시
(4) 기 설정한 Phase 1과 Phase 2의 타격위치 설정
(5) 계획한 동다짐 파라미터에 따라 동다짐을 실시
① 파운더 제원: 중량(W) 23tf, 직경(d) 1.8m(그림 10 참조)
② 낙하고(H) 18m
③ 타격횟수(N) 10회
④ HPT(Heave and Penetration Test) 수행
⑤ VB(Vibration Monitoring) 수행
(6) 작업 플랫폼 레벨링
(7) 각 타격지점에서 H=18m, 5회 타격, Pass 2에 대한 동다짐 수행
(8) 작업 플랫폼 레벨링
(9) 각 타격지점에서 H=10m, 3회 타격, Ironing 수행
(10) 다짐후 지반조사(Post-CPT)를 실시하여 동다짐 개량효과 확인
주변지반의 히빙 및 관입량을 측정하는 HPT는 동다짐 타격지점(print)에서 수행하여, 설정한 타격조합에 대해 관입량과 히빙량을 측정하고, 동다짐 Calibration을 통해 타격횟수 및 낙하고의 적정성을 확인한 후 최적의 다짐조건을 결정한다.
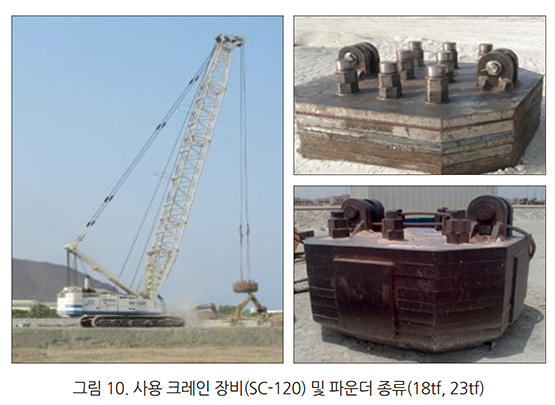
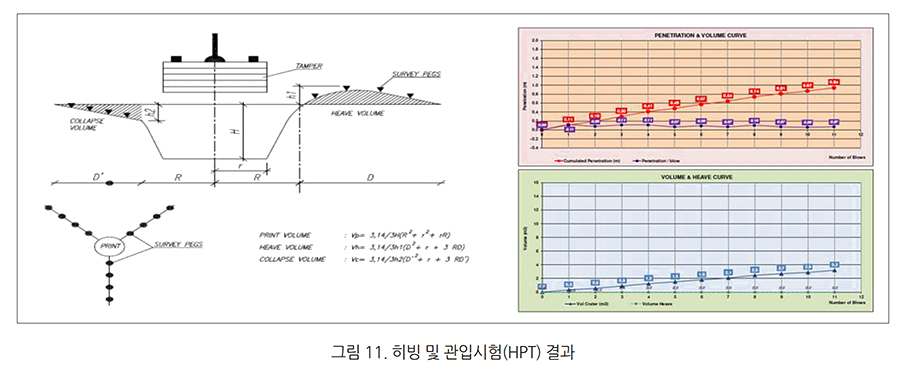
동다짐으로 인한 진동영향 평가(VM)는 인접구조물의 손상방지를 위한 안전거리 검토를 위해 수행된다. 영국 표준(BS 7385.2)에 따르면, 구조물 손상에 대한 안전 한계는 구조물에 따라 약 15~50mm/s이다. 타격중 측정결과 진동기준(PPV=50mm/s)을 만족할 수 있는 최소 안전이격거리는 14.5m로 평가되었고, 구조물과 충분한 이격거리를 확보할 수 있도록 동다짐 배치를 계획하였다(그림 12).
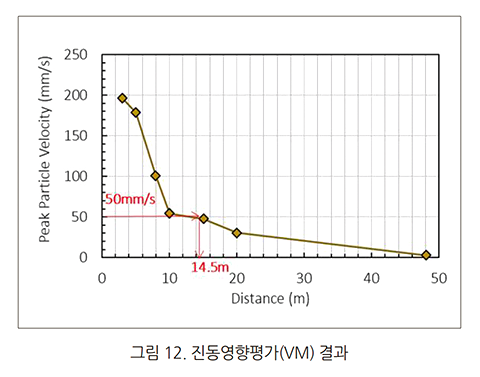
동다짐후 확인조사(Post-CPT)를 수행하여 대상기초의 기준침하량(25mm) 및 허용지지력(300kPa) 만족여부를 확인하였다(그림 13). 동다짐 Calibration에 의해 확인된 동다짐 제원으로 그림 14에 제시한 다짐패턴 및 동다짐 시험계획에 따라 본시공 진행후, 확인시험(Post-CPT) 결과로 구조물기초별 침하량 및 지지력을 평가하였다. 경우에 따라 공내재하시험(PMT), 표준관입시험(SPT) 또는 1.5m×1.5m 이상의 대형 재하판을 이용하는 ZLT을 이용하여 개량후 지반의 변형특성을 확인할 수 있다.
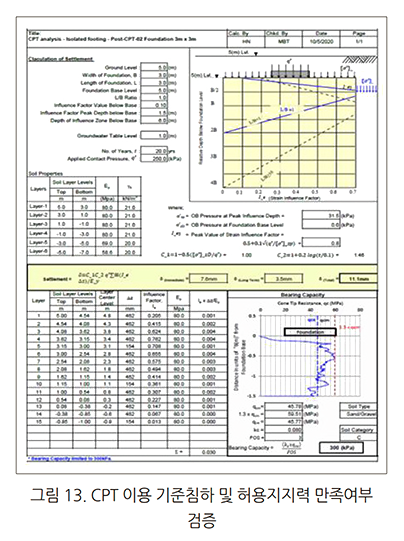
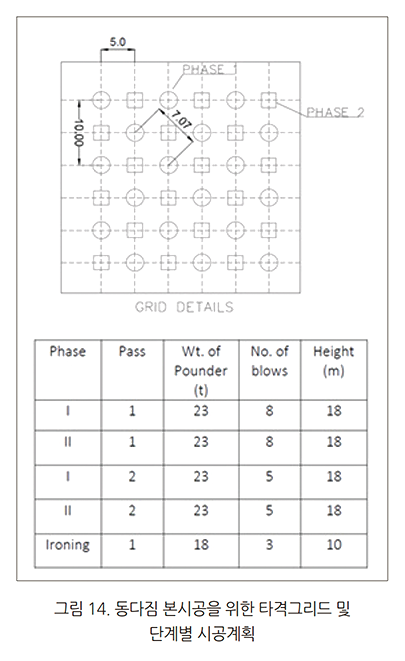
7. 결언
해외 프로젝트에서는 지역적 특성을 고려한 지반거동 예측과 해당 지역에서 동원 가능한 시공장비 및 시공경험을 기반으로 하여 동다짐 공법 적용시의 제반조건들이 결정되므로, 프로젝트 수행시 기존 시공사례에 대한 사전조사가 중요하다. 동다짐 관련 연구는 국내에서도 다수 이루어져왔으며, 특히, 준설매립토 및 쓰레기매립지 등에서의 다양한 데이터가 축적되어 왔다. 그러나, SPT N 기반으로 시공계획을 수립하는 국내 또는 일본에서의 경험과는 달리, 최근 동다짐 적용사례가 많은 중동지역에서의 프로젝트 수행시에는 CPT qc를 이용한 설계 및 시공관리가 이루어진다. 이에 따라, 동다짐 설계 및 시공계획 수립과정에서 국내의 경험과는 다소 상이한 결과를 도출할 수 있기 때문에 주의가 필요하다. SPT N이 보편적인 시험법이기는 하지만, 향후에는 동다짐 적용시 CPT qc 또는 변형특성 기반의 시험법(PMT, ZLT)과 관련한 시공 데이터를 축적하여, 좀더 세분화된 토질조건에 따른 적절한 동다짐 가이드라인을 도출할 필요가 있다. 또한, 축적된 데이터 기반으로 다양한 설계적용 및 시공후 확인결과에 대한 사례분석을 통해, 동다짐 공법의 설계와 시공간의 차이를 줄여가는 노력이 필요하다.
참고문헌
1. 이봉직, 윤준식, 이종규 (2005), “지반조건에 따른 동다짐의 개량심도 평가”, 한국지반환경공학회 논문집, 6(3), 55-61.
2. Leonards, G.A., Cutter, W.A. and Holtz, R.D. (1980), “Dynamic compaction of granular soils”, J. of Geotech. Eng., 106(1), 35-44.
3. Lukas, R.G. (1980), “Densification of loose deposits by pounding”, J. of Geotech. Eng., 106(4), 435-446.
4. Lukas, R.G. (1986), Dynamic Compaction for Highway Construction, Vol. 1: Design and Construction Guidelines, FHWA Report Rd-86/133, Federal Highway Administration.
5. Lukas, R.G. (1995), Geotechnical Engineering Circular No. 1: Dynamic Compaction, Publication No. FHWA-Sa-95-037, Federal Highway Administration.
6. Luongo, V. (1992), “Dynamic compaction: predicting depth of improvement”, Grouting, Soil Improvement and Geosynthetics, 927-939.
7. Mayne, P.W., Jones, J.S. and Dumas, J.C. (1984), "Ground response to dynamic compaction", Geotech. Eng., 110(6), 757-774.
8. Menard, L. and Broise, Y. (1975), “Theoretical and practical aspects of dynamic compaction”, Geotechnique, 25(1), 3-18.
9. Mitchell, J.K. and Katti, R.K. (1981) Soil improvement - state of the art report, Proceedings, 10th International Conference on Soil Mechanics and Foundation Engineering, Stockholm (June), pp. 509-565.
10. Moseley, M.P. and Kirsch, K. (2012), Ground Improvement, Spon Press.
11. Woods, R.D. (1968), “Screening of elastic surface waves by trenches”, J. of Soil Mech. and Foundations Div., 94(4), 951-979.
*본 기사는 저자 개인의 의견이며 학회의 공식 입장과는 관련이 없습니다
구조용 PET 합성섬유 보강 숏크리트 시공사례
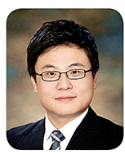
김 승 선
코오롱글로벌(주)(seungsun_kim@kolon.com)
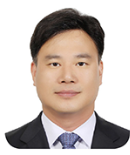
김 영 익
㈜테크비전(youngkim@kolon.com)
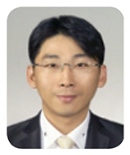
김 상 연
㈜유니온물산(sykim@unionms.co.kr)
1. 개 요
터널 내 숏크리트는 굴착 면 풍화 등 이완을 억제하고 지반을 조기에 안정화, 노출 암반의 절리 및 요철에 의한 응력완화, 지반 아치를 조기에 형성하여 하중을 분산 및 지반 거동을 구속하는 등의 기능으로 건설 중 안정성과 건설 후 내구성을 확보하는 주요 역할을 한다. 이러한 숏크리트는 균열 저감, 내화성능, 등가휨강도(휨인성) 및 내 충격성 등의 성능을 향상시키기 위해 유기계 및 무기계 섬유 보강재를 적용하고 있다. 현재까지는 섬유보강 숏크리트에 있어 강섬유가 널리 적용되고 있으나, 최근 부식에 의한 장기강도 저하와 환경오염, 시공비 증가 등의 단점이 있다. 그로 인해 국내에서는 강섬유의 단점을 보완하기 위하여 합성섬유 보강제 적용 연구가 진해중에 있으며, 국외의 경우 합성섬유 적용이 확대되고 있다.
국내의 경우 섬유보강 숏크리트에 사용되는 섬유보강재는 강섬유가 일반화되어 사용됨에 따라 강섬유에 대한 재료의 품질기준 및 혼입량에 대한 기준은 정립되어 있는 반면, 합성섬유의 경우 설계기준 및 시방서상 사용할 수 있도록 명시만 되어 있을 뿐 재료에 대한 품질 기준이 정립되어 있지않으며, 섬유보강 숏크리트의 품질 기준인 재령 28일 휨강도 4.5MPa 이상, 등가휨강도 3.0MPa 이상을 충족하면 되도록 규정되어 있다(표 1).
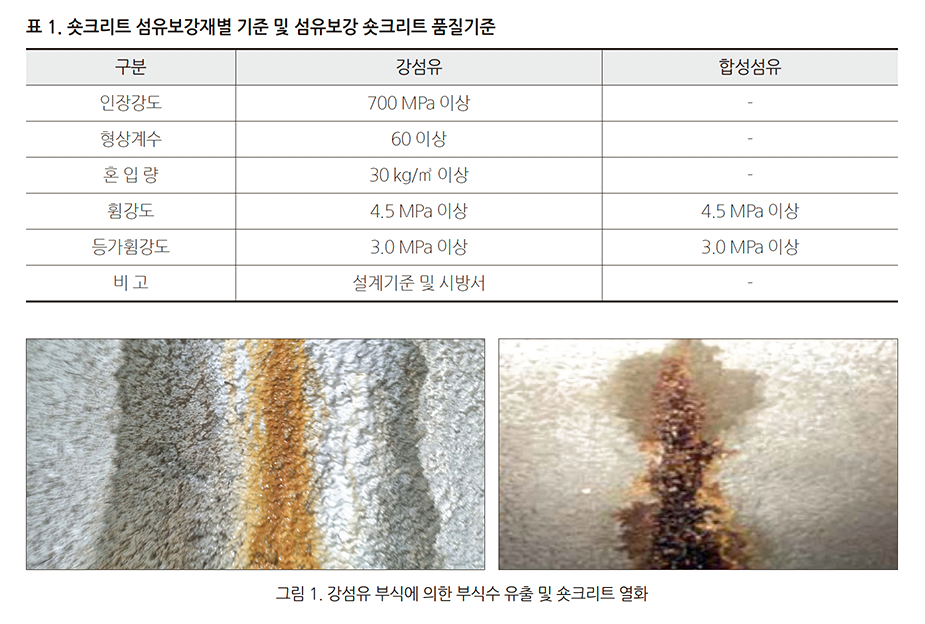
일반적으로 숏크리트는 공법의 특성상 고압의 압축공기로 뿜어 붙히는 특성상 시공이 완료된 숏크리트는 다공성의 특성을 보이게 된다. 이러한 다공성의 숏크리트내 혼합된 강섬유는 굴착과정에서 유출된 암반수와 터널 내 산소와 반응하여 부식이 촉진되며, 숏크리트의 열화현상을 촉진함으로써 장기 강도의 저하에 기인하는 요소로 작용하고 있다.
특히, 하저 또는 해저 구간의 경우 강섬유의 부식 속도가 증가함으로써 숏크리트의 강도 저하의 속도로 증가하는 요소로 작용한다(그림 1).
최근 탄소 배출에 따른 지구 온난화와 그에 따른 환경파괴 등 지구 온난화에 대한 경각심이 높아지고 탄소 배출에 대한 전 세계적인 규제강화 및 지진 등에 내구성을 가질 수 있는 터널 보강재로써 합성섬유의 적용이 증가하고 있다.
특히 숏크리트 보강용 합성섬유 적용에 있어 요구되는 성능으로, 인성 확보가 가능한 높은 인장강도와 화학적 반응을 일으키지 않으며, 원활한 혼합방식과 숏크리트와 혼합시 뭉침 현상을 억제하여 원활한 시공이 가능하며, 균일한 품질확보를 위해 숏크리트 내 균일한 분산이 요구된다.
따라서, 터널 굴착면 안정화를 위해 시공되는 섬유보강 숏크리트에 있어 기존 강섬유 보강재 대비 동등 이상의 품질을 충족하며, 경제성, 시공성, 안전성 등을 고려하여 환경 친화형인 섬유보강재인 PET계 합성섬유가 개발되었고, 본고에서는 PET 합성섬유 현장 시공사례를 소개하였다.
2. PET(Polyethylene Terephthalate) 합성섬유 보강재
본 PET계 합성섬유 보강재는 해외에서 일반적으로 사용되는 폴리에틸렌(PE, Polyethylene), 폴리프로필렌(PP, Polypropylene)의 폴리올레핀계(Polyolefin)와 달리 높은 인장강도를 보이며, 몰탈(Mortar)의 비중에 근접함으로써 배합과정에서 부유 현상이 발생하지 않아 균일한 분산이 가능하며, 내화학적 특성의 친수성 복합수지로 코팅된 합성섬유 보강재로 현재 국내 다수의 현장에 시공 중에 있으며, 기존 강섬유 대비 다음과 같은 장점이 있다.
또한, 해외의 경우 PET 합성섬유 보강재에 대한 연구가 활발히 진행중에 있다.
o 기존 Batch Plant의 구조 변경 없이 적용이 가능 함(그림 2).
o 부식이 발생하지 않아 보관이 용이 하며, 부식이 없어 숏크리트 장기 내구성 저하요소 없음.
o 기존 강섬유와 동일한 최소 인장강도 700MPa 이상으로 강섬유의 최소 혼합량(37kg/㎥) 대비 낮은 혼합량(10kg/㎥)에도 상대적 낮은 비중에 의한 개체수 증가로 강섬유와 동등 이상의 숏크리트 품질 확보 가능(표 2).
o 터널 방수포 시공시 섬유의 돌출부에 의한 방수포의 훼손이 없음.
o 터널 굴착간 섬유의 돌출부에 의한 작업자 안전위해 요소가 제거됨.
o PET 합성섬유는 비중(1.2~1.5g/㎤)이 몰탈의 비중에 근접함으로써 분산성 우수하며, 섬유의 유연성으로 숏크리트 시공 시 시공성 향상에 의한 리바운드가 감소 됨.
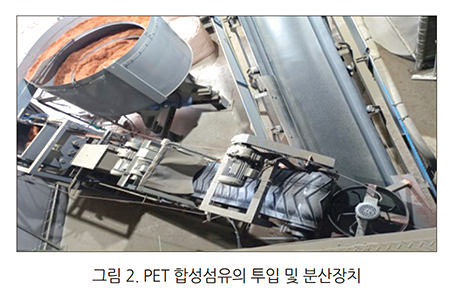
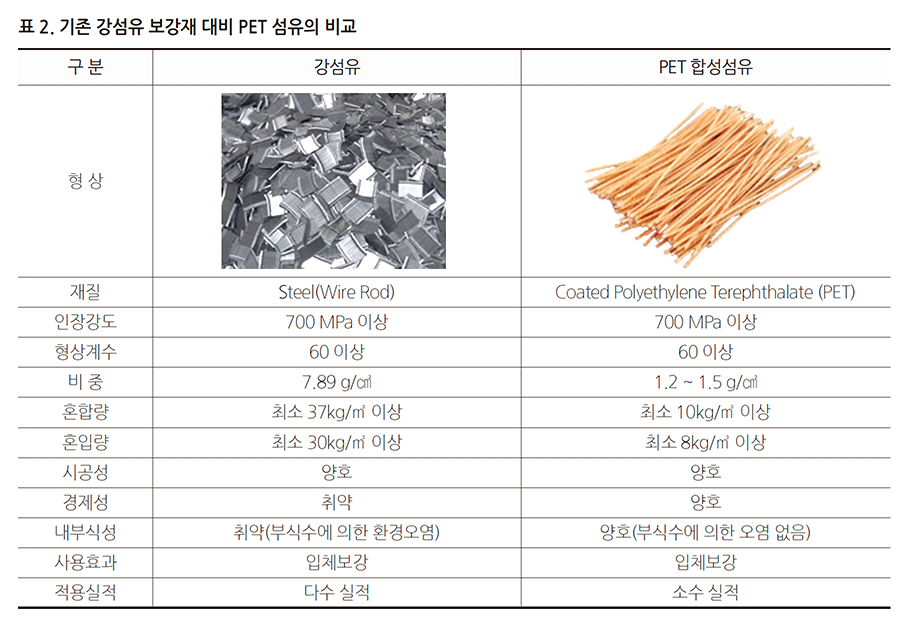
3. PET 합성섬유 보강재 시공현황
현재 PET 합성섬유 보강재를 이용한 숏크리트는 기존 강섬유 보강 숏크리트와 동일한 혼합방식으로 국내 철도 및 도로터널 현장에 적용하여 시공중에 있다.
또한, PET 합성섬유 보강 숏크리트의 현장 적용에 있어 숏크리트 배합의 결정은 기존 강섬유 보강 숏크리트와 동일한 조건으로 실제 현장에서 배합 후 숏크리트의 품질 기준인 재령 28일 휨강도(4.5MPa) 및 재령 28일 등가휨강도 기준(3.0MPa)의 충족 여부를 확인 후 시공 중에 있다.
현재까지 국내 터널 현장에서 숏크리트 섬유보강재로 합성섬유의 현장 적용이 이루어지지 못했던 가장 큰 요인은 앞서 기술한 바와 같이 명문화된 기준의 부재의 요인과 Polyolefin계 합성섬유의 낮은 비중( < 1.0g/㎤)에 의한 혼합시 섬유의 부유 현상에 의한 뭉침현상 및 합성섬유의 투입, 분산 방식의 부재로 숏크리트 섬유보강재로 적용이 어려웠다.
하지만, 내화학적 특성의 친수성 복합수지로 코팅된 PET 합성섬유는 몰탈과 근접한 비중(1.2~1.5g/㎤)을 유지하며, 기존 강섬유의 최소 인장강도(700MPa 이상)를 보유하며, 기존 강섬유와 동일한 섬유의 투입 및 계량 방식을 적용하며, 혼합과정에서 합성섬유의 뭉침을 방지하기 위하여 2단계 분산방식을 적용함으로써 숏크리트내 합성섬유의 뭉침 현상을 최대한 억제함으로써 시공성이 향상되도록 하였다(그림 3).
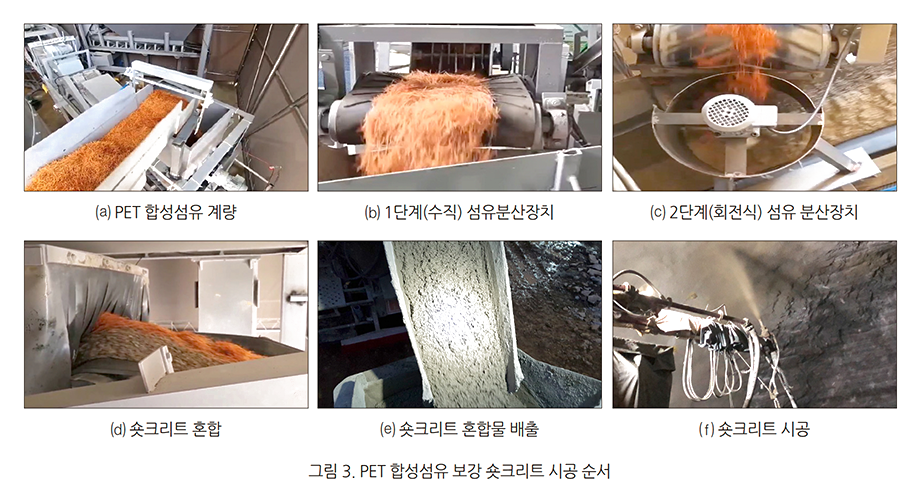
4. PET 합성섬유 보강 숏크리트 품질성능
현재 국내 적용중인 PET 섬유보강 숏크리트의 품질성능에 대하여 숏크리트 품질기준 충족 여부 확인을 위해 PET 합성섬유 10 kg/㎥을 혼합하여 실제 현장에서 시험체를 제작하여 재령 28일 휨강도 및 등가휨강도 시험을 진행하였으며, 그 결과 품질기준인 4.5MPa, 등가휨강도 기준인 3.0MPa 이상을 충족함을 확인할 수 있었다(그림 4)(표 3).
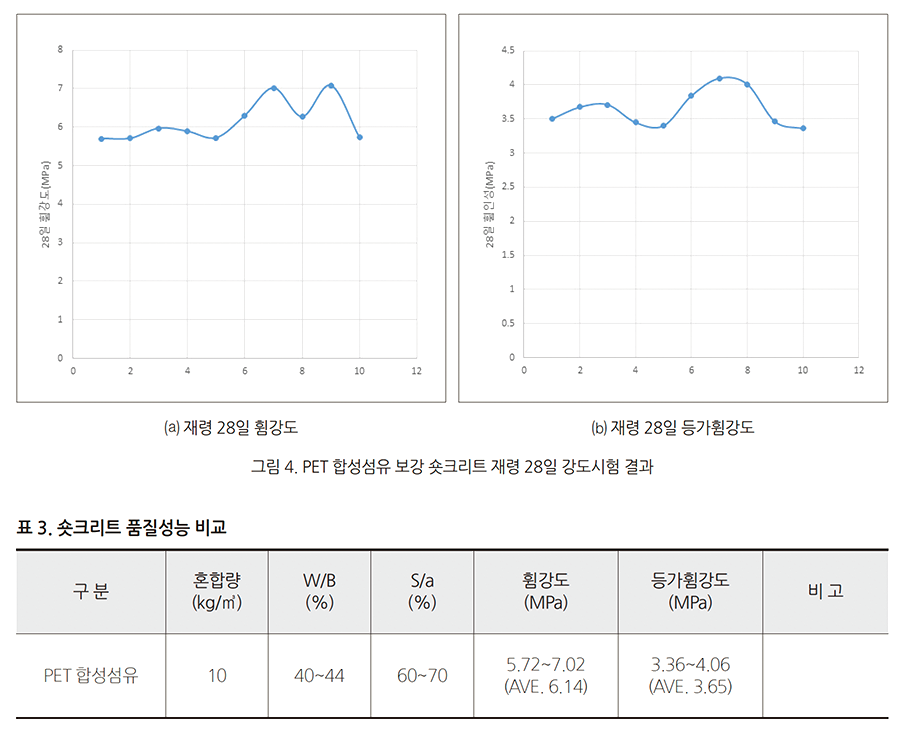
5. 맺음말
터널굴착시 굴착지반 안정화를 위해 시공되는 섬유보강 숏크리트에 있어 기존 강섬유의 경우 부식에 의한 토양의 산성화 및 지하수의 오염을 발생시키며, 굴착 지반의 용출수 또는 하저, 해저구간 시공시 부식에 의한 숏크리트의 장기강도 저하 및 방수포 설치시 섬유의 돌출부에 의한 방수포 훼손 등 터널 방수효과를 저해함으로써 최종 라이닝콘크리트 시공 후 방수효과 저하에 따른 콘크리트의 미세균열부 백화현상 등 유지보수비의 증가의 요인으로 작용되나, 내화학적 친수성 복합수지로 코팅된 PET 합성섬유의 경우 이러한 강섬유의 단점 요소를 보완할 수 있을 것으로 판단된다.
특히, 합성섬유를 적용함에 있어 섬유의 투입 및 계량, 뭉침현상 방지대책 등 해결해야 할 과제에 대하여 해결함으로써 보다 숏크리트의 품질 기준을 충족하면서 환경 친화적이며 경제적인 숏크리트 시공을 기대할 수 있을 것으로 판단된다.
참고문헌
1. 터널설계기준 개정 연구 보고서(1차년도), 2016, 한국터널지하공간학회
2. 터널설계기준 개정 연구 보고서(최종), 2017, 한국터널지하공간학회
3. 김주석, 유상건, 이용준, 신현승, 김은겸, “PET FIBER를 혼입한 콘크리트의 숏크리트 터널 적용에 관한 연구”, 2008, 한국철도학회 2008년 추계학술대회논문집
4. 김성배, 김현영, 이나현, 김장호, “재생 PET 섬유가 혼입된 보의 휨 거동에 관한 연구”, 2008, 대한토목학회 정기학술대회
5. 김성배, 김현형, 이나현, 김장호, “재생 PET 섬유가 혼입된 섬유 보강 콘크리트의 강도 및 균열저항 특성”, 2010, 구조물진단학회
6. 서태석, 공민호, 권해원, “재생 PET섬유 보강 고강도 콘크리트 원형 기둥의 내화성능”, 2016, 한국건축시공학회지 16권 6호
7. Venu Malagavelli, Neelakanteswara Rao Paturu, “Polyester Fibers in the Concrete an Experimental Investigation”, Advanced Materials Research Vols. 261-263 (2011) pp 125-129
8. PET 단섬유 보강 콘크리트 보강 특성, 2020. 일본토목학회 전국 대회 제74회 연례 학술 강연회
*본 기사는 저자 개인의 의견이며 학회의 공식 입장과는 관련이 없습니다.