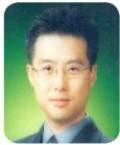
터널 막장면 RMR 가중평가현장관리 방안
1. 서론
본 기사는 현재 건설 중인 합천-창녕 고속도로의 “지질특성을 고려한 비탈면, 터널현장 관리방안, [한국 지반공학회, 기술기사 2020. 9. Vol.36, No. 5]”(1)의 내용 중 터널 막장면 RMR 평가시 천단부 가중평가에 대한 세부적인 자료로서 터널 암판정 시 가중평가의 중요성을 기술하기 위해 작성하였다.
최근 고속도로 노선의 터널비율이 증가하고 장대 터널화 추세로 터널 낙반 등에 의한 안전사고 위험이 증가하고 있다. 안전사고 예방을 위한 터널 막장상태를 효과적으로 평가 할 현장관리 방안이 절실하다.
터널 막장면 평가는 Bieniawski(1989)(2)의 RMR 분류법을 주로 적용하고 있으며, 평가 시 암반강도, 암질계수, 절리면, 지하수상태 등 정량적 평가가 시행되나, 천단부 낙석, 낙반사고가 끊임없이 발생하고 있는 실정이다(사진 1, 2 참조).
「고속도로 터널공법(Ex-TM) 가이드라인」에 서는 “터널 안정성의 저하를 일으킬 수 있는 취약부(천단부, 어깨부)에서 낙석, 붕괴, 지하수 유출 등 암반등급 평가시 안정성을 감안한 가중치 평가”가 언급되어 있다. 터널 천단부 안정성 강화를 위한 가중평가를 보다 객관적이고 명확하게 적용하기 위한 관리방안에 대해 기술하고자 한다.
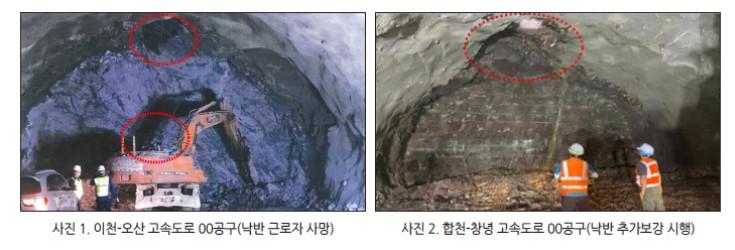
2. 사고유형 분석
2.1 터널 붕괴사고 유형
국내 46개소 터널 붕괴 사고 중 80%가 [그림 1]과 같이 천단부·우각부 낙석 등에 의한 붕괴유형(3)으로 터널사고의 대부분이 터널 막장면 천단부에서 발생하는 실정이다.
막장면사고의 원인 중 용수출현·파쇄대·풍화에 의한 붕괴가 약 76%이며, 절리교차 및 기타 낙반 등에 의한 것이 24%에 이른다.
중력의 영향을 받는 상부 천단부에서 붕괴가 주로 발생하는 것이 당연한 결과이겠지만 현재의 막장면의 평가는 막장 전체면의 평균적인 개념으로 접근하고 있다. 이에 사고예방에 보다 효율적인 평가를 위해서는 위험단면에 대해서는 터널 막장면 가중평가를 통해 안정성 제고 및 사고예방을 도모할 필요성이 있다.
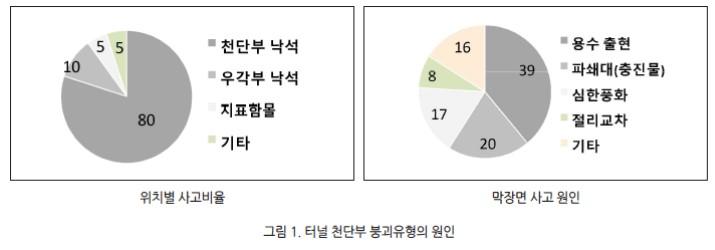
2.2 터널 천단부 사고사례
본 노선의 굴착 중 발생한 낙반사고를 분석한 결과 암판정시 지보패턴이 RMR=55점인 C-1 타입으로 시공 중 천단부 낙반발생으로 보강구간은 L=14.0m로 손실은 공기지연(보강 8일), 붕락부 보강(금액=숏크리트+Wire Mesh, R/B추가 등=0.4억원)과 부가적인 경제적 비용이 약 0.8억원 총 1.2억원 손실이 발생하였다. 막장면 RMR 가중평가로 재분석시 암반강도와 절리군 항목에 가중평가한 결과 RMR 47점인 C-2타입으로 평가된다. 따라서, 해당 막장면에 천단부 안전성이 높은 지보타입과 보조공법을 적용하였다면 낙반사고를 예방하여 안전성과 효율성을 도모할 수 있었을 것이다.
2.3 RMR 평가시 가중평가 필요성
현재 시행중인 암판정은 막장면에 대한 평균값 적용으로 RMR 평가가 이루어지고 있는 실정이다. 터널 막장면 천단부의 안전사고 예방을 위하여 터널 암판정 시 낙석, 낙반을 고려한 가중치 평가를 반영하여 안전사고에 대비하고자 관리방안을 수립하였다. RMR 가중평가는 터널 굴착 중 하부보다 상부 천단부 낙반 및 붕괴사고를 선제적으로 예방하기 위하여 가장 취약한 상단부 막장상태를 최우선으로 고려하여 암판정을 시행할 수 있는 현장 관리방안으로 판단된다.
2.4 RMR 평가시 가중평가 현장 적용성
국내에서 RMR 평가를 위한 많은 연구와 고찰이 수행되어 있으며, “암반변수 민감도 RMR 분류점수 세분화(4)(장욱태, 2015)”, “현장 RMR값과 천단 연약대 RMR값을 산정, 천단부에 RMR에 가중치를 주는 W-RMR 방법(5)(장형두, 2011)”등 여러 연구에서 RMR 평가 방법을 제안하였으나, 본 노선 현장은 RMR 평가시 막장면에 적용 할 수 있는 평가인자를 고려하여 위험성이 높은 터널 상단부에 가중치를 주는 방법을 제안하고자 한다.
3. RMR 가중평가시 현장 관리방안
3.1 RMR 가중평가 개념
터널 암판정시 RMR분류법은 무결암의 강도(R1), 암질계수(R2), 절리면 간격(R3), 절리면 상태(R4), 지하수(R5)와 절리방향에 따른 RMR 보정치(R6)로 평가하고 있으며, 한국도로공사 Ex-TM 설계는 RMR 평가시 A-타입을 제외한 RMR점수가 10점 단위로 지보패턴을 구분하고 있다. 따라서, [그림 2]와 같이 RMR 평가시 막장면의 (1/2)H 상부 막장면을 평가하며, 암반강도, 암질계수, 불연속면 간격, 절리면 및 지하수 상태가 하부보다 상부가 불량할 시 가중평가를 수행할 수 있도록 현장관리 방안을 제시하고자 한다.
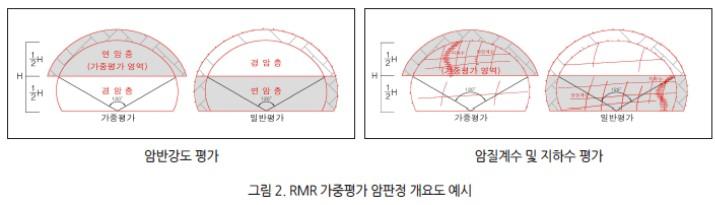
3.2 RMR 가중치 평가절차
(1) 막장면 가중평가 순서도
막장면 가중평가 순서도는 표 1과 같다.
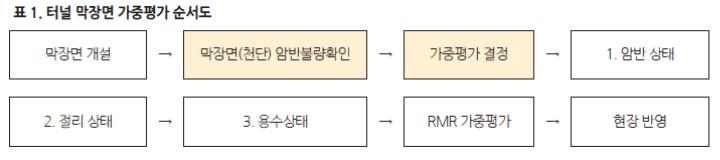
(2) RMR 가중평가 방법
RMR 가중평가는 매막장 실시되는 상황은 아니며, [그림 3]과 같이 후속 막장면 천단부에 위험구간이 발생할 경우 시공 중 안전성 강화를 위하여 시행한다.
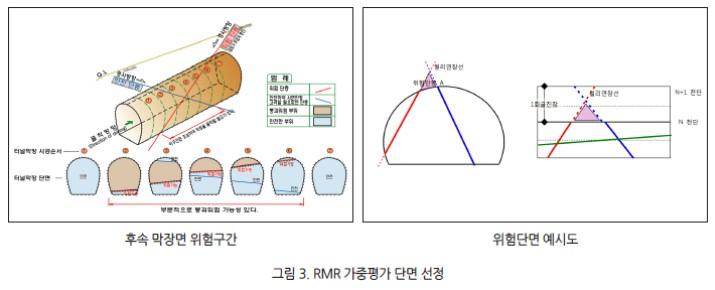
① 암종 교호구간 막장면 출현시 암반강도가 낮은 암종으로 암반강도 하향평가(그림 4)
② 막장면 절리군이 다수로 분포할 시 암질계수 하향평가(그림 5)
③ 막장면 용출수 출현시 용수량 및 분포도에 따라 지하수 하향평가(그림 6)
④ RMR 평가→위험성 가중치 지보패턴 적용막장면 RMR 가중평가로 적용된 지보패턴은 현장 천단부 위험군에 안전성을 확보함.
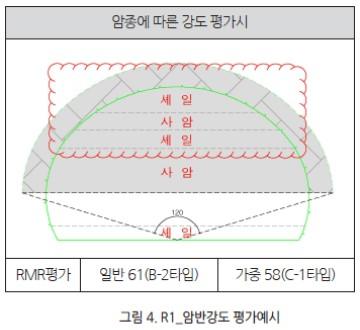
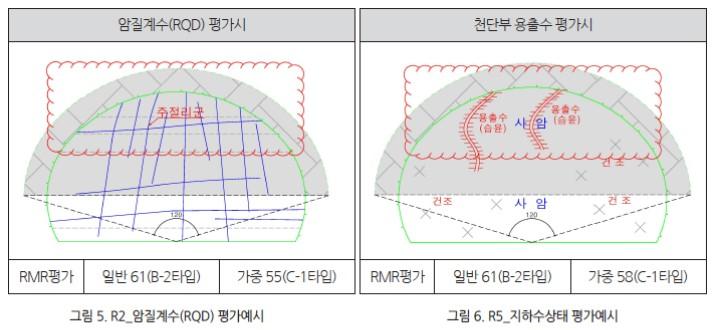
3.3 RMR 가중평가 사례
(1) RMR 가중평가 실제사례
실제 현장 RMR 가중 평가시 [그림 7]과 같이 현 막장면에서 상부 셰일층과 하부 사암층으로 교호하며, 막장면 상부 파쇄절리가 발달하고 있고 습윤상태로 조사되어 R1, R2, R5에 가중 평가시 RMR=54점, C-1 타입이나, 일반적으로 막장면 전체 평가시 RMR=63점으로 B-2 타입으로 적용된다.
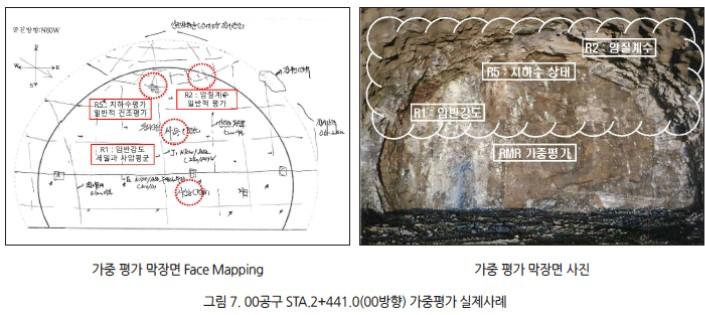

(2) 가중평가의 안전 관리방안
본 노선은 일률적 보강방안을 개선하여 하단부가 상단부 보다 양호한 암반으로 출현시 [그림 8]과 같이 하단부 R/B를 공제하여 천단부 위험구간인 절리불량 또는 용출수 구간에 R/B 추가 설치 및 절리방향을 고려한 보강재 시공각 조정 등 현장 지질상황을 감안한 안전한 보강패턴을 적용하여 탄력적으로 운영 중이다.
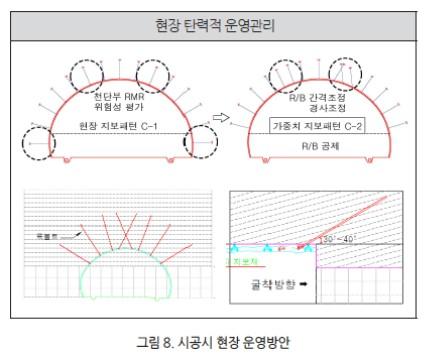
(3) RMR 일반평가와 가중평가 비율
본 노선의 현재(2020년 12월 기준) 터널굴착 공정율은 평균 37.0%로 각 공구별 굴착 공정율은 0.6~62.3%이다. [표 3]과 같이 터널 굴착시 RMR 가중평가 비율은 약 2.5%로 가중평가 시행에도 지보패턴은 미변경 되는 경우도 다수로 판정되었다. 분석결과 지보패턴은 B-2에서 C-1이 10.7%, C-1에서 C-2가 10.1%로 암반상태 평가 시 RMR점수 경계부에서 지보패턴 변경이 다수 이루어진 것으로 분석되는 바이다.
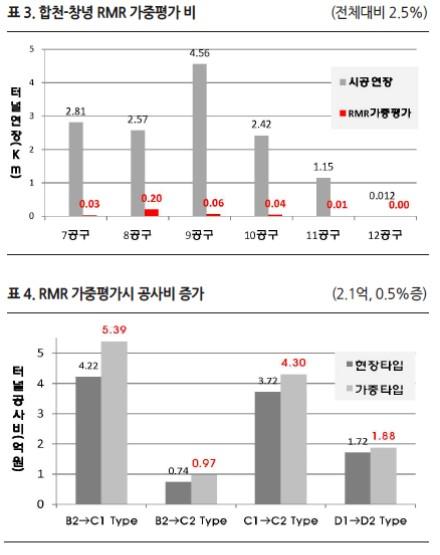
(4) RMR 가중평가 기대효과
2019년 11월 낙석사고 발생 후 시행한 RMR 가중 평가시 [표 4]과 같이 굴착 공사비는 약 2.1억원 증가하였으며, 굴진 완료시 5.6억원 증액이 예상된다. 가중평가 적용 이전(2020년 3월) 3.2km 굴진 중 낙석사고는 2회 발생하였으나, 적용 이후(2020년 12월 기준) 10.3km 추가 굴진 시 낙석, 낙반사고는 발생하지 않은 것으로 조사 되었다. 굴진율 감소, 공기 증가 등 부가적 경제적 손실은 발생하나, 막장면(천단부)위험구간 보강과 굴진장 축소, 여굴 감소 등에 의한 낙석사고 예방 및 안전성 증대의 기대효과가 있다고 판단된다.
4. 결 론
1) 합천-창녕 고속도로의 지질특성은 경상분지 퇴적암으로 낙반 및 붕괴사고에 유연한 대처를 위하여 암판정 RMR 평가시 막장면에 위험성 가중치를 부여하는 관리방안을 제안하였다.
2) 막장면 암반불량 판단시 RMR 위험성 가중치 평가방안은 암반강도, 암질계수, 지하수상태 항목 등에 배점을 하향평가 하였으며, 상단부와 하단부의 암반상태에 따라 R/B 지보는 추가 및 간격, 경사조정으로 현장상황에 맞는 보강이 되도록 현장관리를 탄력적으로 운용하고 있다.
3) 또한, 검측자의 습관적인 기술상태를 탈피하고자 공구 순환평가제, 검측자의 정기평가 등 사업단입회하에 암판정 검수를 실시하여 전체 노선의 막장면 지질상태 및 특이사항 등을 공유하여 담당 공구의 문제점에 대해 보다 안전한 시공을 위하여 검측자의 경험을 상향하고자 하는 바이다.
4) 막장면 위험성 가중치에 의해 안전한 지보패턴을 현장에서 적용할 수 있도록 경험적 데이터 축적 및 시공시 지보패턴 등 추가연구, 지침개정 등이 수립되어야 할 것이다.
참고문헌
1. 지질특성을 고려한 비탈면, 터널현장 관리방안, 2020년 “한국지반공학회 Vol 36, No.5” pp24~36
2. Bieniawski, Z. T.(1989), “Engineering Rock Mass Classification”, John Wiley & of Sons, New York, pp.29~34 pp.51~59, p.139
3. 터널 붕괴사례집, 2010년 배규진 등 pp377~383
4. 암반변수의 민감도에 따른 RMR,분류법 개선에 관한 연구, 2015년
5. 터널 붕괴 위험도에 따른 RMR 연구, 2011년 한국암반공학회
6. 지질조건을 고려한 RMR 인자값 추정을 위한 선형회귀식 제안, 2007년 “The Journal of Engineering Geology Vol 17, No.4” pp.555~566
7. 국내 터널 암판정 문제점 분석 및 개선방안 연구, 2015년 “한국위기관리논집 제11권” pp.147~155
8. 고속도로 터널공법(Ex-TM) 가이드라인, 2016년 한국도로공사
9. 고속국도 제14호선 합천~창녕간 건설공사 지반조사 보고서, 2017년 한국도로공사
[본 기사는 저자 개인의 의견이며 학회의 공식 입장과는 관련이 없습니다]
IoT 기반 스마트 사면 계측 시스템(SCS_Ver. 2.0) 소개
1. 서 론
최근 10년간 여름철 자연재해 중 산사태 등 사면 붕괴로 인한 피해가 41%를 차지하고 있으며, 우면산 산사태(2011년)로 58명의 인명 피해와 3,768억원의 재산피해를 초래하는 등 사면 붕괴로 인한 피해가 심각한 실정이다.
기존의 사면 붕괴 계측 시스템들은 가격이 비싸고, 설치 및 유지관리가 어려운 문제가 있으며, 다양한 센서와 네트워크를 채용하여 시스템 구조가 복잡하고 관리자가 계측된 자료를 바탕으로 1차 분석한 후 경보를 발령하는 느린 위기대응체계도 비효율적이다. 지방자치단체에서 운용중인 급경사지 계측 시스템은 GPS센서, 광섬유센서, 함수비센서, 간극수압계, 강수량계 등 많은 센서를 복합적으로 설치하고 각각의 센싱된 값을 바탕으로 붕괴위험을 판단하기 때문에 분석에 시간이 오래 걸리고 초기 붕괴 징후인 전조정보 제공이 곤란한 경우가 있으며 활용할 수 있는 분야도 제한적인 경우가 있다. 기존의 센서 네트웍은 센서노드와의 거리가 짧고, 상용망에 연결되어 사용하여 통신과금이 발생하며, 네트웍 구조가 복잡하고 설치비 및 유지보수 비용이 많이 발생한다.
본 기사에서는 지표에서 계측하는 기존 방식과 다르게 지중에서 발생하는 미세 지반 변형을 스마트센서로 감지하고, 사물인터넷 전용 시스템인 LoRa 모듈을 사용하여 저속 장거리 통신에 효율적이며, 비용이 저렴하고 자체 판단 알고리즘이 적용된 선진형 시스템인 IoT 기반 스마트 사면 계측 시스템(Smart Slope Collapse Alarm System, SCS_Ver.2.0)을 소개하고자 한다.
2. IoT 기반 스마트 사면 계측 시스템
본 고에서 소개하고자 하는 스마트 사면 계측 시스템 기법(SCS_Ver.2.0)은 사면에 설치되는 GFRP(Glass Fiber Reinforced Plastic) 봉 센서를 활용하여 사면의 변형을 계측하고, 설정된 알고리즘에 따라 변위속도에 대한 기준치에 사면 변위가 도달하면 경보를 발생하여 관리자에게 알려주는 IoT 기반 계측 기술이다.
사면의 변형을 관리자가 실시간으로 스마트폰을 통해 확인할 수 있고, 사면의 변형 및 붕괴발생 시 관리자가 해당 지역을 명확하게 파악하여 신속한 대응을 수행할 수 있다. 특히 지역 주민들도 스마트폰으로 사면의 변형을 실시간으로 모니터링 할 수 있기 때문에 붕괴 전 주민의 사전대피가 가능하다. 아울러, 이 기술은 무선 시스템을 이용하기 때문에 유선 시스템에서 발생하는 센서의 고장 및 유선 절단으로 인한 미작동 현상을 방지할 수 있고, 설치 및 유지관리가 간단하여 보급률을 높일 수 있는 장점이 있다. IoT 기반 스마트 사면 계측 시스템은 GFRP 봉 센서, IoT EndDevice, IoT Gateway, IoT Server로 구성된다.
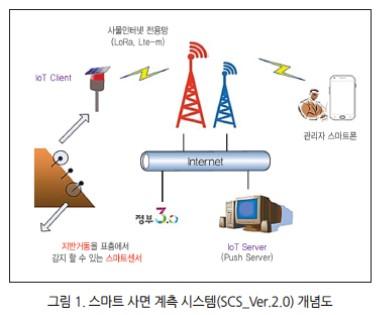
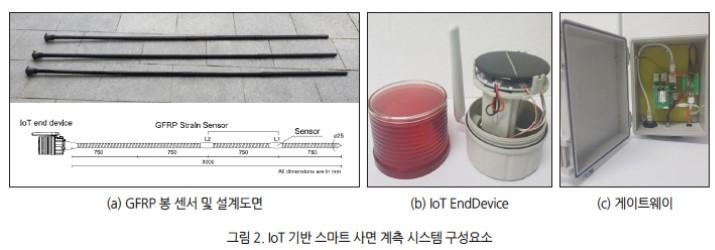
3. 사면 붕괴 모사 실험을 통한 센서의 성능 검증
활동면의 접선에 평행한 변위는 활동면의 근처에서 변화가 크며, 활동면으로부터 떨어진 위치에서는 지반 변형이 작고, 지표와 가까운 얕은 사면부분에서도 전단변형이 미소하게 발생하는 것으로 알려져 있다. 본 연구진은 사면에 봉을 관입하여 설치하고(3∼8m 관입), 휨변형에 따라 전단변형율의 증가를 포착할 수 있는 스마트 센서 기술을 개발하였다. 봉 센서는 사면붕괴 시 사면의 활동면 부근(3∼8m 내외)에서 증가하는 변형을 손쉽게 계측하기 위한 장치로서 그림 2에 나타낸 바와 같다.
그림 3에서 보는 바와 같이 사면 거동 발생 시 봉 센서 계측결과의 절대값 및 부호에 근거하여 사면 붕괴시 지반거동의 정성적 파악이 가능하다. 지반거동 발생시 상단 또는 하단부의 변위가 상대적으로 미소하다면 봉 센서에는 휨 변형이 발생하게 된다. 이에 따른 변위(d)와 변형율(ε)의 관계를 실험을 통해 구하는 경우, 변형율의 응답에 의해 사면의 상대적 변위를 구할 수 있게 된다.
사면의 역학적 변형을 스트레인게이지의 저항변화에 의한 전압검출을 기본원리로 IoT End Device의 실시간 계측을 통해 사면 붕괴 시 시간에 따른 전단변형률 증가패턴을 기반으로 붕괴를 예측할 수 있는 전조 신호를 검출하는 기술이며, 이는 많은 실험 데이터에 기반한 과학적인 패턴 인식 기법이다.
센서의 검정은 한 쪽을 고정단으로 하고, 자유단에 하중을 가하여 변위를 측정하는 방식의 캔틸레버 보 조건을 부가한 검정방법을 사용하며 하중부가에 의해 발생하는 변형과 응답변형율을 측정한다.
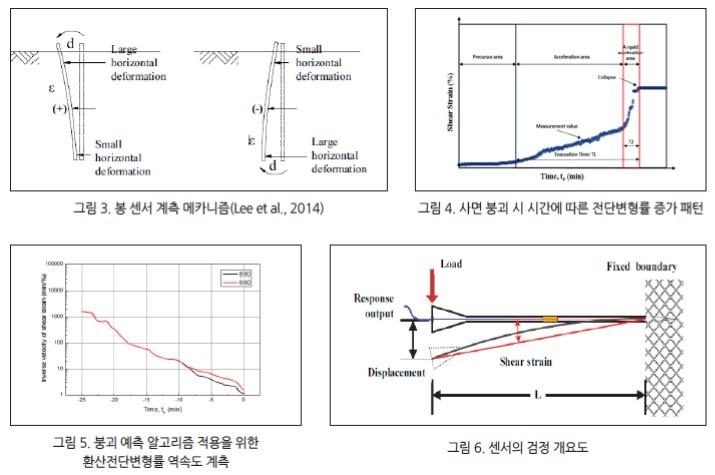
4. 사면 붕괴 모사 실험을 통한 센서의 성능 검증
4.1. 사면 붕괴 모사 실험
암반 버력을 성토하여 모형사면을 축조하고 Steel 및 GFRP 재질의 봉 센서를 매설한 후 절토 굴착하여 사면을 붕괴시키는 실험을 수행하였으며 사면의 굴착 깊이와 간격은 수치시뮬레이션을 통해 검토하고 실대형 현장모형실험에서는 그 결과를 반영하여 실험 방법을 설계하였다.
모형사면 축조작업에는 백호우를 사용하였고 버켓에 의한 다짐 축조 후 기울기는 56°, 천단부 높이 8.0m로 사면을 조성하였다(그림 7). 굴착 깊이 및 구간은 실험 Case 별 동일한 조건을 적용하였으며, 굴착에 따른 사면의 거동 계측을 위해 굴착구간별 대기시간을 부여하였고, 록볼트 센서의 설치 위치는 천단부 시점으로부터 1.5m 이격된 위치에 설치하였으며, 각 센서 간 수평간격은 약 1.5m로 설치하였다(그림 8∼그림 10).
현장실험 계측결과, 일정값의 변위를 나타낸 후 급가속적으로 증가하여 좌측사면 붕괴가 시작하였고 이어서 약 8분 후 전체 사면붕괴가 발생하였으며, GFRP 센서의 경우 나사철근형(steel) 센서보다 변위 감도가 높은 것으로 나타나 IoT 기반 스마트 사면 계측 시스템 구축에 유리할 것으로 사료된다.
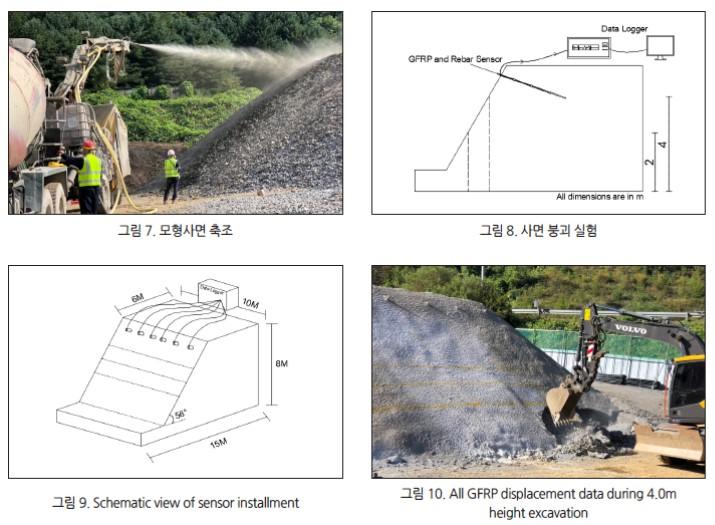
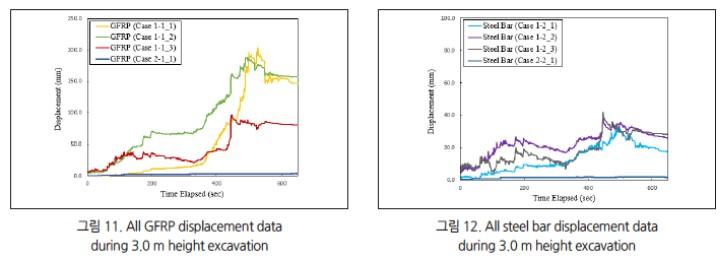
4.2. 수치해석에 의한 스마트센서의 적용성 검토.
본 연구진들은 개별요소 해석법과 시공과정, 굴착단계별 해석이 가능한 범용 유한요소해석(General-purpose FEM Program) 프로그램인 ABAQUS ver.6.14와 3차원 불연속체 해석이 가능한 개별요소 프로그램인 3DEC를 사용해 수치해석을 수행하고, 지반의 변형 및 사면 파괴 거동에 대해 검토하였다.
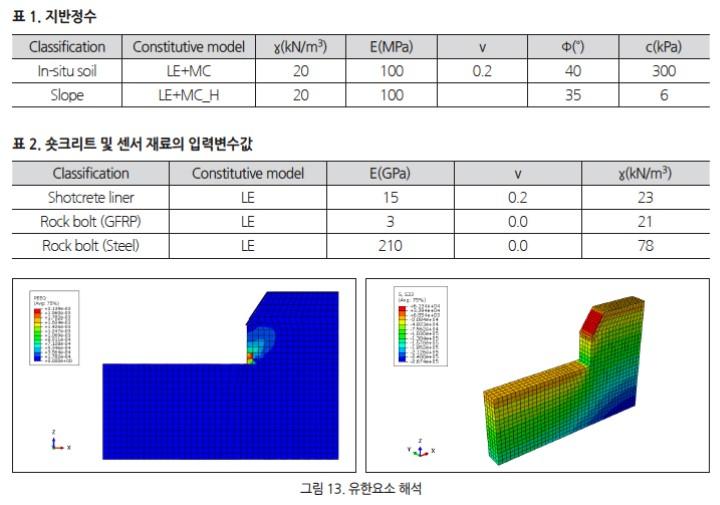
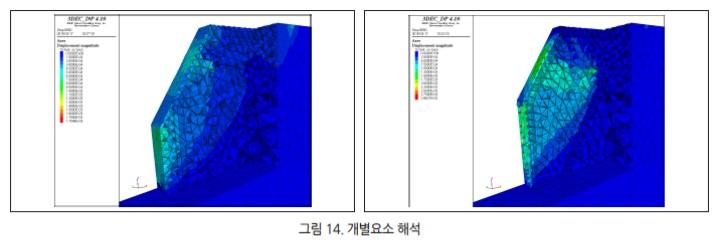
수치해석 결과는 실제 현장에서 측정한 스마트센서의 변위값과 비슷한 경향을 나타내었는데 변위 감지 성능은 동일한 조건에서 나사철근형 봉 센서보다 GFRP형 봉 센서가 높은 것으로 사료되어 GFRP형 봉 센서가 시공성 및 유지관리성 측면에서 IoT 기반 스마트 사면 계측 시스템 구축 시 유리 할 것으로 판단된다.
5. 스마트 센서의 전단거동 특성
본 연구진들은 GFRP 록볼트를 이용하여 사면붕괴를 모니터링하기 위한 봉 센서를 제작하였으며, 그 성능을 평가하기 위해 이면 전단시험을 수행하였다. 암반에 시멘트 밀크로 충진된 상황을 상정하고 시멘트 페이스트로 충진된 조건에서 변형률계를 보호하기 위하여 GFRP 봉 센서를 열수축튜브로 코팅하고 실험을 수행한 후 코팅하지 않은 경우와 비교하였다.
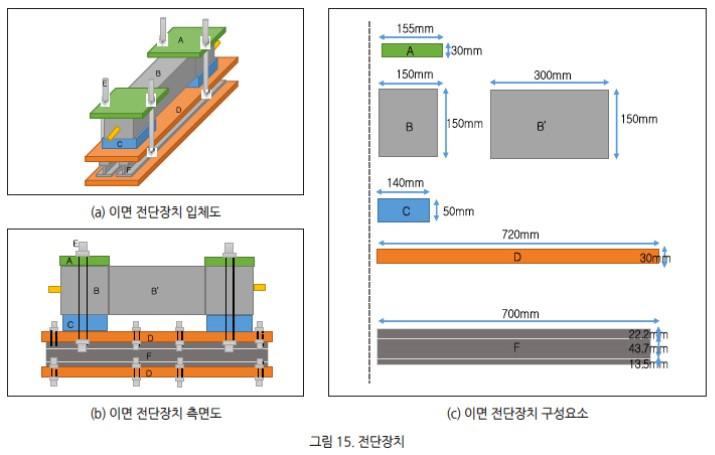
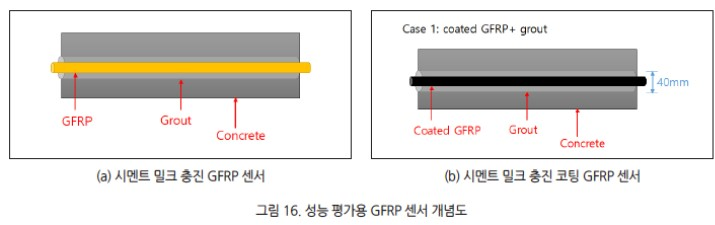
전단시험 장치는 500kN의 하중에 버틸 수 있도록 제작하였는데, 구성요소 중 철판 A는 콘크리트 블록(B)을 고정하여 전단하중 재하시 휨이 발생하지 않도록 하는 역할을 하고, A는 강봉(E)을 이용하여 하부판(D)에 고정되며, 철판 C는 전단에 의해 변위가 발생할 수 있도록 콘크리트 블록을 D로부터 일정 간격 띄워 주는 역할을 하고, F는 I-beam로서 전단하중에 의해 D가 변형되지 않도록 하는 역할을 하며, 콘크리트 볼록(B)을 제외한 전단시험 장치의 모든 구성요소는 스테인레스 스틸로 제작되었다.
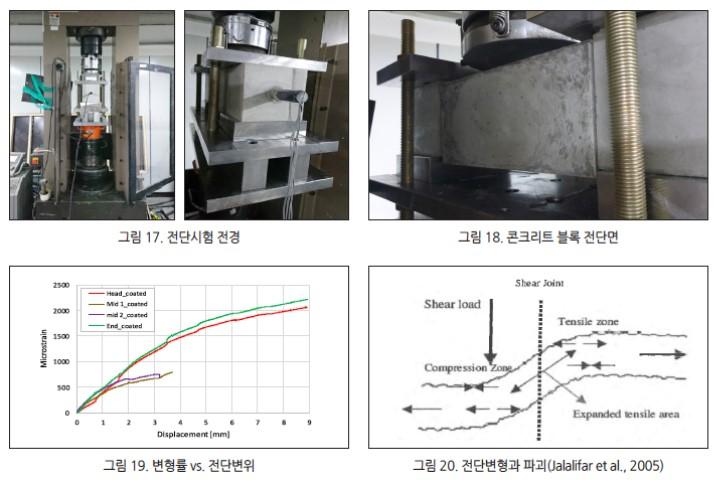
GFRP 센서가 암반에 시멘트 밀크로 충진된 것을 모사하기 위하여 콘크리트 블록에 시멘트 밀크로 충진하여 GFRP 센서를 셋팅하고, 전단하중은 일축압축시험장치에 설치된 로드셀로 측정하였다. 로드셀로 측정되는 하중과 변형률계로 계측되는 변형률은 데이터로거를 이용하여 수집하였고 측정 데이터는 데이터로거를 이용하여 초당 1회씩 수집하였으며, 실험 종료 후 PC에 저장하였다.
실험결과 GFRP 센서의 전단변위에 따른 변형률은 두부와 선단부에서 계측된 변형률이 서로 유사하였고, 중간부 1과 중간부 2에서 계측된 변형률이 유사하였다. 하지만, 두부와 선단부에서 계측된 변형률이 중간부에서 계측된 변형률보다 전단변위가 더 크게 나타났다. 이는 두부와 선단부는 인장이 발생하고 중간부는 압축에 영향을 받기 때문으로 사료된다.
열수축튜브로 코팅된 GFRP 센서를 시멘트 밀크로 고정한 경우, 코팅하지 않은 경우보다 전단변위에 따른 변형률이 덜 만감하게 반응하였다. 하지만, GFRP 센서에 변형이 발생할 시 시멘트 밀크와 함께 변형률계가 손상되는 현상이 감소하여 좀 더 큰 전단변위까지 변형률을 측정할 수 있었다.
본 연구진들은 코팅된 GFRP 센서를 암반사면에 설치하는 방법이 전단변위에 대한 민감도도 우수하고 큰 전단변형에 대해 변형률을 측정할 수 있어 암반사면 모니터링을 하는데 유용하게 적용될 수 있는 방법임을 알 수 있었다.
6. IoT 기반 스마트 사면 계측 시스템의 현장 성능 검증
스마트 사면 계측 시스템의 성능을 검증하기 위해 강원도 횡성군에 위치한 암반사면에 스마트 사면 계측 시스템을 설치한 후 사면붕괴 실험을 수행하였다.
6.1. 센서의 검정
본 연구진들은 GFRP 센서의 변위-변형률 응답 검정을 수행하였는데, 오른쪽 끝에서1/4길이의 위치를 고정단으로 하고, 자유단에 하중을 가하여 변위를 측정하는 방식으로 캔틸레버보 조건과 같은 검정방법을 사용하였으며, 하중 부여에 의해 발생하는 변형과 응답변형률을 측정하였다.
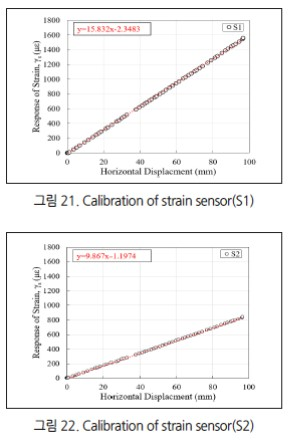
그림 21과 그림 22는 각각의 검정결과를 도식화하여 나타낸 것으로 S1은 센서의 1/4 지점, S2는 센서의 1/2 지점에서의 GFRP 센서의 검정결과이다.
검정결과의 추세선은 현장 계측 값의 효율적 활용을 위하여 Eqs. (1), Eqs. (2)와 같이 1차함수로 표현하였으며 하중부가에 따른 스마트센서 자유단의 변형에 따른 응답변형률이 비교적 명확하게 판별되어, 지반 변형거동의 분석에 적용이 가능할 것으로 판단된다.

6.2. 발파실험 사면 조성
암반사면에서 GFRP 센서의 성능을 검증하기 위해 강원도 횡성군 횡성읍 학곡리에 위치한 암반사면에 천공 후 GFRP 센서를 설치하고 붕괴 실험을 수행하였다(그림 23).
암반사면은 높이 8.0m 경사는 55°~75°로 전체적인 풍화도는 보통풍화(M.W)가 우세하며, 상부비탈면은 수평으로 완만한 형상으로 실험발파 사면 조성을 위해 장약위치 0.5m, 센서 설치 위치 3.6m, 4.2m, 5.1m 높이에 천공을 실시하였다(그림 24).
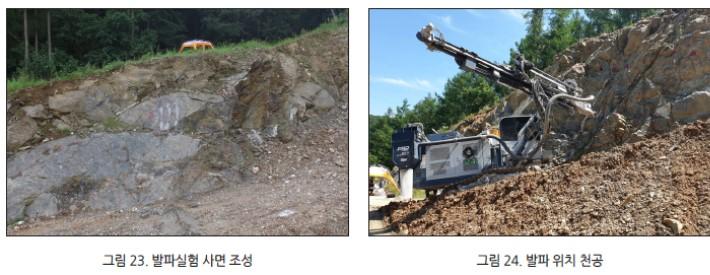
6.3. 센서 설치
센서 설치 위치 3.6m, 4.2m, 5.1m 높이에 IoT Client가 장착된 GFRP 센서와 통신케이블이 연결 가능한 GFRP 센서를 수직간격 0.9m, 0.6m, 수평간격 0.6m로 설치하였다(그림 25∼그림 26).
1㎥당 시멘트 880㎏, 물 730ℓ의 비율로 시멘트 밀크를 제작하였으며 소성수축 및 침전현상 방지를 위해 팽창제를 시멘트 중량의 1% 첨가한 뒤 센서가 설치된 위치에 시멘트 밀크를 주입하였다(그림 27∼그림 28). 사면 붕괴 과정에서 계측된 데이터는 상단부 데이터 케이블 통하여 Data logger에 연결하여 수집하는 방법과 IoT Client와 Lora통신망을 통해 Gateway로 계측데이터를 무선으로 수집하는 방법을 비교·분석하였다(그림 29∼그림 31).
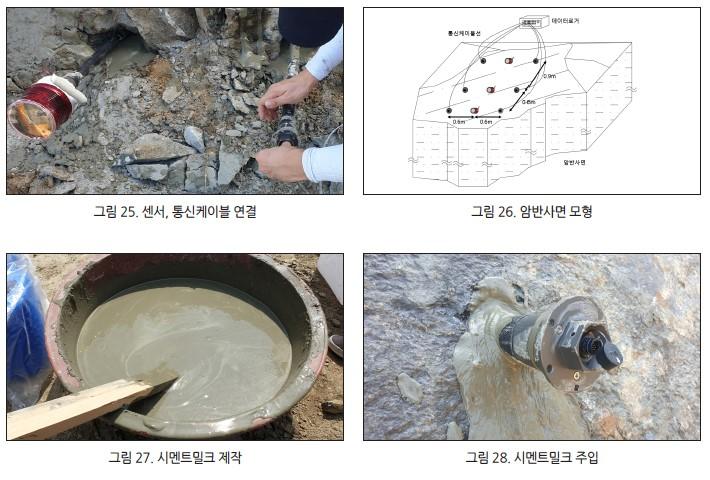
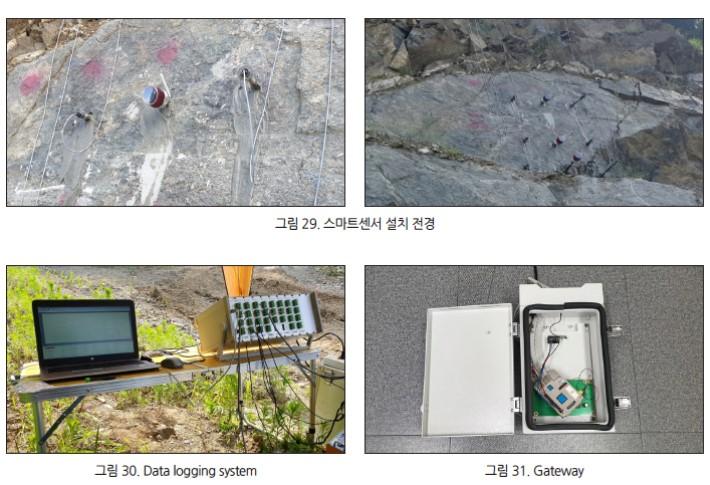
6.4. 암반사면 붕괴실험
본 연구진들은 그림 32와 같이 지반에서 50cm 높이에 천공 및 장약 후 발파하여 암반사면의 붕괴거동을 관찰하였으며 발파는 같은 천공 위치에서 총 3번 나눠서 발파하였고 각 발파마다 30분 동안 데이터 수집을 하였다.
그림 33은 첫 번째 발파 시 센서 설치 우측 암반 블록이 발파의 영향으로 무너진 것을 나타내며 그림 34는 두 번째 발파 전경으로 이 때 스마트센서가 설치 된 맨 하단부에 암석이 무너지면서 일부 스마트센서의 케이블선이 끊어졌다. 세 번째 발파 전경으로 좌측 암반사면이 무너지면서 센서가 설치된 사면 좌측으로 커다란 크랙이 발생하였고 발파의 충격으로 의해 두 번째 가운데 IoT Client가 떨어져서 파손되었다(그림 33∼그림 36).
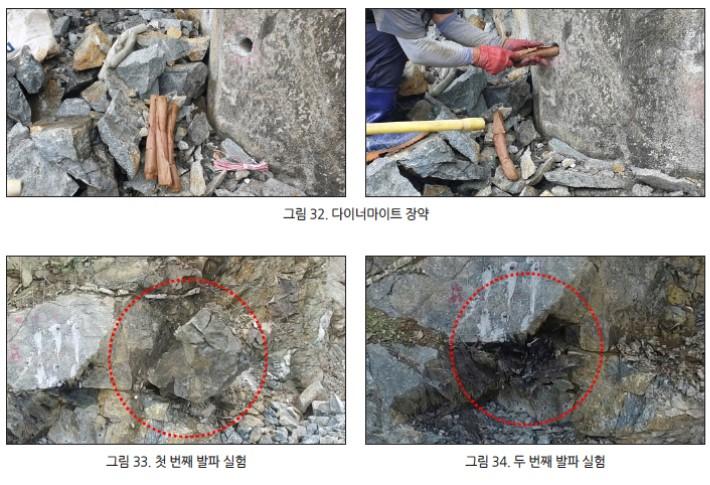
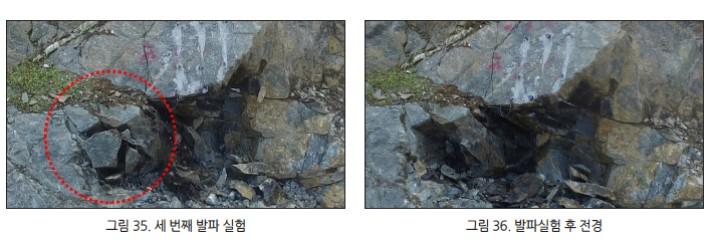
6.5. 실험 결과 및 고찰
표 3과 그림 37은 데이터로거를을 통해 얻은 발파 실험에서의 시간 경과에 따른 변위값을 나타낸다. 첫 번째 발파 이후 변위값은 Sensor1 s1, s2는 모두 -1mm로 나타났으며, Sensor2 s1, s2는 +4.23mm, +82.27mm, Sensor3 s1, s2는 +41.61mm, -3.04mm의 변위가 발생하였다.
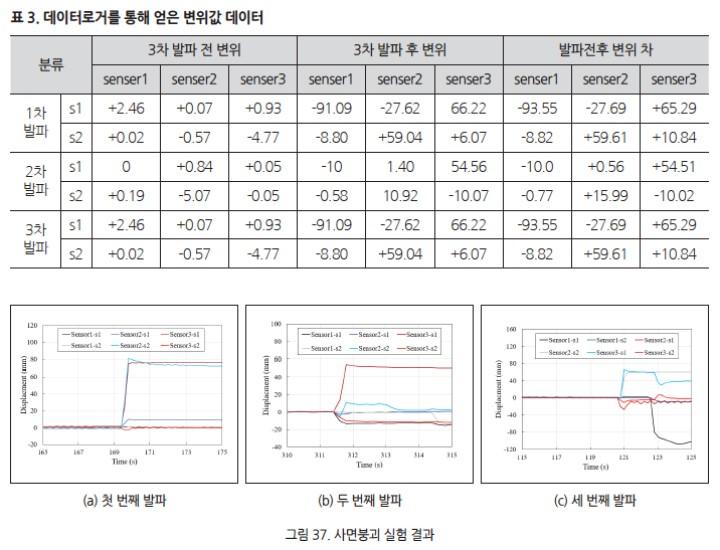
6.6. 현장발파시험 수치해석
현장발파시험을 수행하여 얻은 계측결과의 적정성을 검토하기 위해 3차원 유한요소모델을 작성하여 수치해석을 실시, 계측결과와 비교분석을 수행하고, 진동속도에 영향을 미치는 각각의 Parameter 해석을 수행하여 Critical parameter 및 범위를 선정하였다(그림 38∼그림 39).
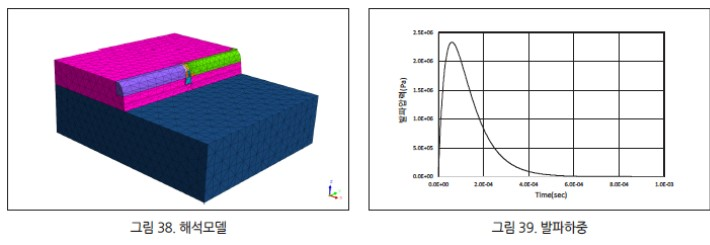
대상구조물에 비하여 주변 매질 영역이 상대적으로 더 큰 경우, 이들 상호간에 미치는 영향을 고려하기 위해서, MIDAS GTS NX의 점성경계는 경계에 일정한 각도를 갖는 물질파를 흡수할 수 있는 경계조건이므로 해석하려는 구간에서 하나의 요소가 무한대 방향으로 퍼져나가는 응력파의 외부영역 거동을 잘 모사할 수 있다. 대상 구조물 및 주변 지반 모델링시 MIDAS GTS NX에서 지원하는 경계조건인 점성경계를 적용하여 발파하중의 소산 영향을 고려하였다.
발파에 영향을 미치는 인자 및 변수를 분석하기 위한 해석을 수행하였으며, 지반의 탄성계수, 점착력, 내부마찰각, 단위중량을 원지반 물성치를 기준으로 10%씩 감소시켜 각 Case 별로 해석을 수행하여 발파속도에 미치는 영향을 비교·분석하였다. 매개변수는 동탄성계수, 내부마찰각, 점착력, 단위중량을 표 4에 나타낸 바와 같이 총 24 Case로 구분하여 수치해석을 수행하였다.
3차원 유한요소 모델을 작성하여 수치해석을 실시한 결과, 첫 번째 발파에서 센서위치의 최대변위는 약 16mm, 두 번째 발파에서에서 센서위치의 최대변위는 약 61mm, 세 번째 발파에서 센서위치의 최대 변위는 약 102mm로 나타났으며 통신 케이블을 통해 얻은 변위 계측결과와 잘 부합하는 것으로 나타났다.
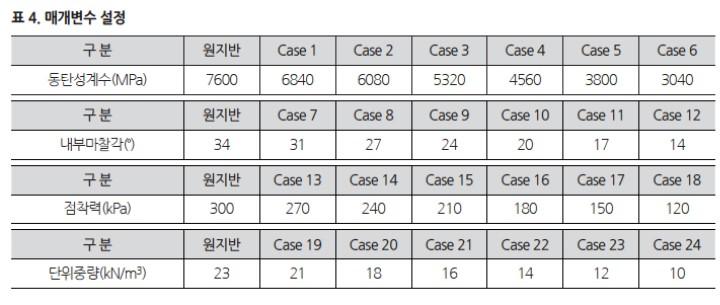
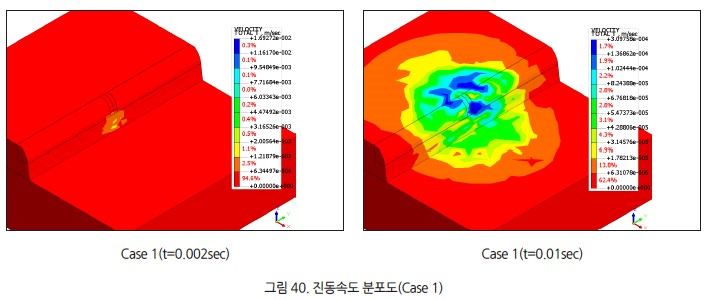
수치해석 결과(그림 40∼42), 동탄성계수가 점차 감소할수록 진동속도는 증가하는 경향을 나타내고, 동탄성계수가 60% 감소시에는 진동속도가 0.001377m/sec로 나타나며 원지반과 비교하였을 때 진동속도가 약 42% 증가하는 경향을 보인다. 또한, 단위중량이 점차 감소할수록 진동속도는 증가하는 경향을 나타내며, 단위중량이 60% 감소시에는 진동속도가 0.001480m/sec로 나타나고 원지반과 비교하였을 때 진동속도가 약 52% 증가하는 경향을 보이며 단위중량의 변화가 발파 후 매질의 진동속도에 영향을 가장 크게 미치는 매개변수인 것으로 판단된다. 점착력과 내부마찰각에 대한 매개변수 해석 결과, 점착력과 내부마찰각의 인자들을 점차 감소시키더라도 진동속도가 원지반의 진동속도와 차이가 크게 나지 않는 것으로 나타났기 때문에 점착력과 내부마찰각이 진동속도에 미치는 영향은 크지 않은 것으로 판단된다.
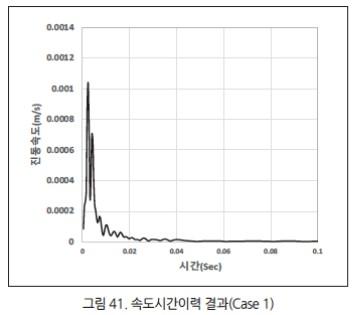
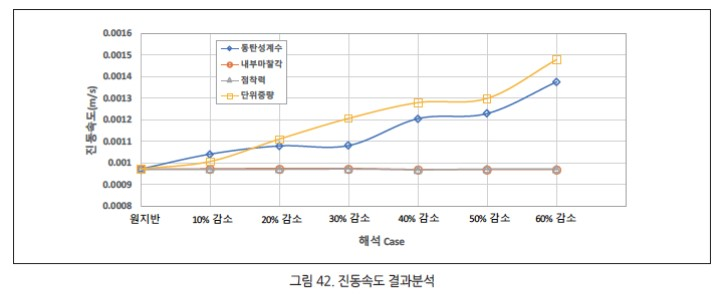
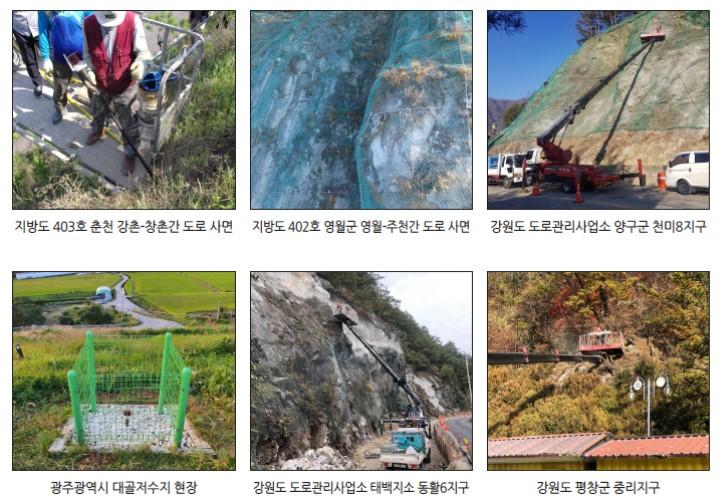
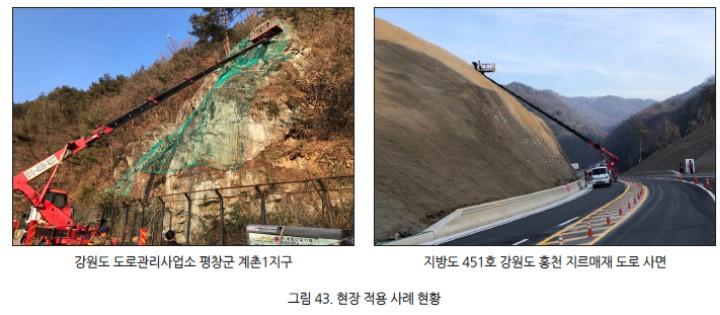
7. 결론
본 기술은 기존의 사면 계측시스템과는 다르게 활동면과 가까운 거리에서 지반의 거동을 정밀하게 감지하여 사면 붕괴 전에 미소 변위 계측을 통해 전조정보 단계에서 변위 발생을 관리자에게 전달하여 미리 사전 조치가 가능하도록 하는 충분한 재난 대비 시간을 제공할 수 있다.
전단변형률 증가를 사전 감지할 수 있는 변위센서를 다수 장착하고 있으며, IoT 자가망 구축을 통한 통신비용 절감 및 장거리 저전력 시스템으로 직접 서버나 관리자의 스마트폰으로 위험 상태 정보를 실시간 확인이 가능하다. 또한 기존 계측시스템의 비용 상승 요인인 계측 및 분석, 유지관리에 알고리즘 적용을 통한「붕괴 위험의 자체 판단 기술」도입으로 별도의 인력이 불필요하다.
기존의 시스템은 소단에 설치되는 경우가 많고 급경사면에는 설치하기 곤란한 경우가 있는데, 이 기술은 급경사면을 포함한 모든 현장에 적용될 수 있어 기술의 적용 범위가 넓다. 특히 적은 인력으로 센서 설치가 가능하고, 실시간으로 사면의 변형을 파악 할 수 있는 장점이 있기 때문에 그 수요는 앞으로도 지속적으로 확대될 것이라 전망된다.
This research was supported by a grant(20TBIPC144286-03) from Technology Business Innovation Program funded by Ministry of Land, Infrastructure and Transport of Korean government.
[본 기사는 저자 개인의 의견이며 학회의 공식 입장과는 관련이 없습니다]