국내 LNG선 접안 Jacket 구조물 기초설계
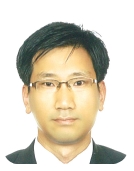
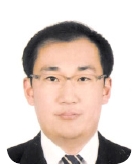
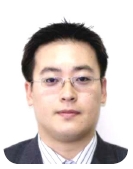
1. 서 론
세계적으로 친환경 천연에너지연료의 성장은 수요측면에서 가파를 것이다. 우리나라의 경우, 최근 정부에서 LNG 수요 증진정책으로 LNG 수요가 계절적 요인과 무관하게 꾸준히 증가하고 있으며 유사한 수입 의존도를 보이는 주요국과 비교하면 설비규모가 상당히 낮은 수준 뿐만 아니라, 에너지원 전량을 수입하고 있는 우리나라 입장에서는 적기 물량 공급 운송을 위한 대규모 LNG 저장시설과 항만시설 필요성이 증대되고 있다. 이에 2012년 12월에 GS에너지와 SK E&S가 공동 투자하여 설립한 보령 LNG 터미널(주)는 LNG선의 접안 및 하역 그리고 저장시설 및 설비를 갖춘 국내최고의 기업이라 할 수 있다. 보령 일대에는 현재 2017년 1월부터 운영 중인 3기와 현재 건설 중이 1기에 더해 20만㎘ 규모 LNG 저장탱크 2기가 추가로 건설되고 있다. 산업통상자원부로부터 LNG 터미널 5,6호기에 대한 시설계획을 승인받음으로서 보령 LNG 터미널은 LNG 저장탱크 건설사업자(EPC)와 접안시설 건설사업자(EPC)를 선정하고 현재 실시설계를 진행하여 2018년 1월에 본격적인 공사에 들어갈 예정이다. LNG저장탱크 건설에 약 42개월(3년 6개월)이 소요된다는 점을 감안하면 2021년 10월쯤에는 20만㎘ 규모의 저장탱크 총 6기가 운영돼 120만㎘ 규모의 저장시설을 갖게 된다. 이는 저장탱크 1기에 약 9만톤의 LNG를 저장할 수 있다고 볼때 연간 약 600만톤의 LNG를 저장할 수 있는 규모다.
현재 GS건설은 SK건설과 공동으로 “보령 LNG 터미널(1단계) 항만건설공사”를 성공적으로 마치고 “보령 LNG 터미널(2-2단계) 항만건설공사”를 EPC 입찰방식으로 수주하여 실시설계를 마무리하고 2019년 01월부터 공사를 진행 중에 있다. 공사내용 및 공사 평면도는 Table 1과 그림 1과 같다. LNG선박의 접안시설은 선박의 소요수심과 기초지반의 조건, 현장의 시공여건 등을 종합적으로 고려하여 Caisson식이 아닌 Jacket Dolphin식으로 설계되었다. 단일 대상선박을 위한 국내 LNG선의 접안시설 구조물과는 달리 다양한 대상선박(45K~180K CBM급)의 접안을 위해 Working Platform에 접안시설인 Fender가 설치되어 있다. Jacket 구조물의 기초설계는 대부분 API code를 기준으로 설계되고 있으며 이는 가스공사 Jacket 구조물 설계시 주로 사용하는 설계기준을 준용함에 따른 것이다. 하지만, API code의 적용시 불합리한 문제를 갖고 있으며 이는 지반의 종류가 국내여건에 불리하게 작용되고 있다. 이를 본 기술기사에서 설계시 고려한 내용을 중심으로 공유하고자 한다.
2. 설계기준 분석
말뚝 지지력의 안전율은 Operation & Extreme 조건으로 구분하여 안전 2.0과 1.5로 적용되었다. Extreme 조건은 지진시에 해당되며, 설계기준인 API code에 대한 말뚝지지력 설계기준을 간략히 요약하면 다음과 같다.
개정 API code에서는 모래지층에 대한 주면마찰인자와 선단 지지력 계수를 모래의 상대밀도에 따라 상세히 구분하여 적용토록 설계정수를 Table 3과 같이 제시하고 있다. 기반암에 그라우팅된 말뚝의 주면 및 선단 지지력에 대하여, API code에서는 단위주면 마찰력은 기반암 내지 그라우트의 일축압축강도 절반 값을 넘지 않으며(물론, 감소계수는 천공홀의 Roughness, 암반의 불연속면 존재 등에 의존), 보통 이 값보다 적게 나타난다고 언급되어 있다. 단위선단 지지력은 기반암내지 그라우트의 암반 타입에 따른 지지력 계수를 곱한 일축압축강도 값을 넘지 않으며, 일반적으로 단위 선단지지력은 이 값보다 적게 나타난다고 언급되어 있다(API 2A-WSD, 선단지지력은 9.6MPa 넘지 않는다). 또한, 인발 지지력은 압축시의 주면 마찰력으로 적용하고 말뚝의 무게와 흙의 폐단(soil plugged) 무게를 고려하여야 한다고 언급되어 있다. 이러한 API code의 내용을 보면 국내 지반의 특성이 중동지역과 달리 연암 이상의 기반암이 조기에 출현하거나 말뚝을 기반암에 상당한 심도로 근입해야 하는 조건이 상당함에도 불구하고 기반암 내 설치되는 Jacket or Pin Pile의 주면마찰지지력의 산정이 모호하다 할 수 있다. 이에 비해 선단지지력은 매우 보수적인 접근을 하고 있다.
이번 프로젝트 설계시에서는 접안구조물이 Jetty type으로서 LNG선박의 접안시 및 운영시 파랑 등의 영향으로 압축과 인발력을 동일 Dolphin에서 동시에 지지되어야 하나, 근입말뚝의 심도는 압축력 보다는 인발력에 의존하여 결정되었다. 따라서, 선단지지력의 산정시에는 구조물의 중요도를 고려하여 API에서 제시하는 매우 조밀한 모래의 한계값을 적용하였으며 주면마찰력의 경우는 기존문헌, API code, 그리고 실내시험값을 비교 검토하여 설계에 적용할 필요가 있었다.
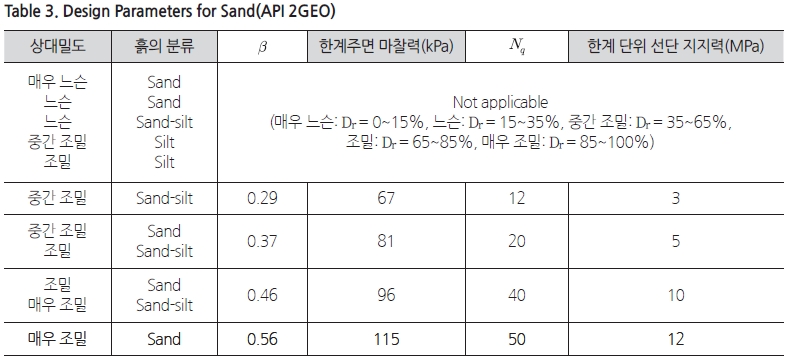
3. 지반조사결과 분석
Jacket & Pin Pile의 설계지지력 산정을 위한 지반조사는 각 Dolphin마다 1공의 시추조사를 원칙으로 하였으며, 특히 WP와 BD 구조물은 선박의 접안/계류의 안전성 검토를 위해 총 5공의 시추조사를 면밀히 수행하였다. Dolphin구조물에 실시한 총 10공의 시추조사의 결과인 지층도는 그림 2와 같으며, 대부분은 상부에 토사 및 풍화암층이 5~10 m이상 존재하고 일부에서는 연암 또는 경암이 1~2 m의 토사층 밑에 조기 출현하는 지층분포를 확인하였다. 현장 조사된 연/경암의 단위중량은 20.3~27.3 kN/㎥, 전단파 속도는 1,026~1,667 m/s, 일축압축강도는 11.6~114.1 MPa로 확인되었다.
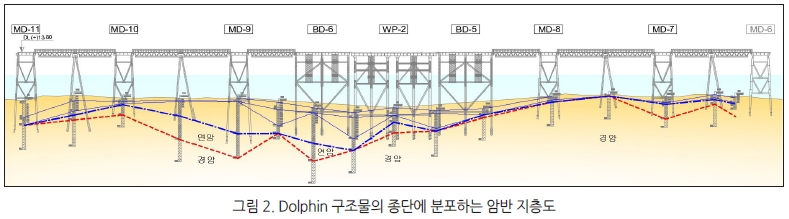
앞서 언급한 것과 같이 Jacket 구조물의 기초는 인발(Pullout)에 의존하고 있어, 당 현장과 같이 Pin Pile이 연/경암 지층에 근입되는 Grouted pile의 경우 Pile-Grout 및 Grout-Rock간의 마찰력에 의한 비교를 통해 Pre-failure 조건의 값을 고려할 필요가 있었다. 이에 Pile-Grout간의 마찰력은 API code에서 추천하고 있어 Grout-Rock간의 마찰력을 실내시험으로 확인하고자 접촉면 마찰시험을 실시하였다. 시험방법은 국제기준을 참고하여 Standard Test Method for Performing Laboratory Direct Shear Strength Tests of Rock Specimens Under Constant Normal Force (ASTM D 5607-08)와 Suggested Methods for Determining Shear Strength(ISRM suggested method)를 참고하여 시험을 수행하였다. Grout - Rock의 접촉면 상태는 Roughness계수(JRC)에 따라 JRC=0인 경우와 JRC=8~10인 경우로 구분하고 Roughness가 있는 경우는 실 시추한 절리면 Core를 시편으로 제작하여 시험하였다. 실제 RCD천공시 Rock 표면은 암반상태에 따라 달라지겠지만 JRC=0인 상태는 거의 발생하지 않는다고 볼 수 있다. 그림 3과 4는 각 Roughness 조건에서의 구속응력-전단응력 관계를 보여주고 있다.
시험 결과에서와 같이, Peak시 Grout-Rock간 단위 마찰력은 JRC=8~10인 경우(0.08 ~ 0.43 MPa)가 JRC=0인 경우(0.05 ~ 0.27 MPa)에 비하여 1.6배 크게 나타났다. Jacket구조물 기초의 평균 설치 심도인 GL(-)25 m지점의 전단응력은 JRC=8~10인 경우 0.31~0.34 MPa 로 분석되며, JRC=0인 경우 0.20~0.21 MPa로 나타났다.
4. 설계기준과 실험결과 비교분석
해당 프로젝트의 경우 Jacket 구조물 기초는 경제성 및 시공성을 고려 Jacket Leg를 Seabed Line에 위치시키고 상부 토사층 및 풍화암 구간은 Jacket Pile을, 암반구간 부터는 Pin Pile을 설치하는 공법으로 시공되며, 상부 작용하중을 1차적으로 Jacket Pile의 주면마찰력으로 감당 후 2차적으로 내부에 설치되는 Pin Pile의 선단지지력 및 Pin Pile 외부에 충진되는 그라우팅의 주면마찰력으로 연직력에 저항한다.
API code내 사질토 지층의 설계변수는 주로 화성암을 기반암으로 갖는 지질의 풍화에 의한 규산질 흙(Siliceous soil)인 실리카 성분을 가진 지반에 해당되나, 상대밀도는 표준관입시험 결과에 근거하여 반영하였다. 이들 변수는 암반지반에 대한 분류 없이 상대밀도에 따른 지층으로만 구분되어져 있다. 하지만 국내의 말뚝 지지층은 얕은 토사층 하부에 연암 이상의 기반암이 조기 출현하는 지층조건이 많으며 당 현장도 이러한 경우이다. 따라서 암반지반에서의 말뚝은 그라우팅처리가 수반되며 이 경우의 단위 선단지지력과 주면마찰력의 적용값이 기초 공사비의 경제성을 좌우한다 할 수 있다.
설계기준인 API는 기반암이 대심도에서 출현되는 구간에 적합하며, 국내 현장과 같이 조기 기반암 출현시 암지반의 마찰력 및 선단인자 값은 모호하며 보수적 수치를 제시하고 있어 경제성 측면에서는 적용을 고민하게 한다. Limiting Unit End Bearing(in Rock)값을 API 2A-WSD에서는 9.6 MPa, API 2GEO에서는 암종별 지지력 계수를 곱한 일축압축강도로 제시하고 있으나, 그라우트된 말뚝의 선단지지력은 보링공의 굴삭제거 정도 및 암반의 불연속면의 존재로 지지력이 적거나 무시할 수 있으며 선단지지력의 한계값은 그라우트와 말뚝의 응력에 의해 결정된다고 언급하고 있다.
앞서 언급한바와 같이 Jetty 형식의 접안시설물에서는 말뚝의 근입심도는 압축보다는 인발에 의존하며 인발시에는 말뚝주변의 그라우팅으로 인해 Pile-Grout 또는 Grout-Rock간의 마찰력이 상이함으로 문헌에서 제시하는 Pile-Grout간 마찰력과 당 현장의 Jacket 구조물의 Pin Pile 시공 평균심도에 해당하는 실내시험을 수행한 Grout-Rock간 마찰력을 확인한 결과, Pile-Grout간 마찰력이 작아서 이를 설계에 적용하는 단위 주면 지지력으로 사용하였다. 국내적용사례 및 문헌과 기준들을 고려하여 경제적인 설계를 위해 적용된 설계 계수 값들은 Table 4와 같다.
5. Jacket별 Pin Pile 근입심도
암반에 근입된 말뚝의 지지력 산정에 있어 단위선단지지력은 암반강도, 불연속면 간격, RQD, 현장시험값 등을 활용하여 산정하고 있으나, 아직도 많은 설계기준에서 단위 주면마찰지지력은 모호하고 보수적으로 접근하고 있으며 이는 해안구조물 특히 인발력에 지배되는 Jetty구조물에서는 안정성 뿐만 아니라 경제성에도 많은 영향을 미친다고 할 수 있다. 당 현장에서 접근한 단위 선단 및 주면마찰 지지력을 적용할 경우 말뚝의 근입길이가 API code에만 의존하는 경우와 비교하여 최소 8% 이상의 절감을 가져 온다는 결과를 확인하였다.
암반에 근입되는 Pin Pile의 경제성은 단위 선단지지력 보다는 주면마찰 지지력에 더 의존하여 영향을 받는다. 동일한 단위 주면마찰지지력에서 단위 선단지지력의 증가는 최대 33%의 Pin Pile 근입깊이 감소를 가져왔으며 이는 외적응력에서 수직방향 비중이 매우 큰 WP에서 나타났다. 이와는 반대로 Mooring Dolphin에서는 단위 선단 지지력의 증가에 의한 Pin Pile 근입깊이 감소는 9~11%정도만 나타났다. 또한, 동일한 단위 선단지지력에서 단위 주면마찰지지력의 증가로 인하여 대부분의 Dolphin 구조물이 마찰 하중에 의존하여 대략 50%의 Pin Pile 근입깊이 감소를 가져왔다. Table 4의 기존 API code값을 적용한 근입심도에 대한 Design Value를 적용한 Pin Pile의 근입심도의 감소비를 각 Dolphin에 대하여 나타내면 그림 5와 같다.
6. 결 론
당 현장은 국가보안 “가”급 시설물로서 외적 조건에 충분한 안정성을 지녀야 한다. 하지만, 기반암이 조기출현하고 대부분의 기초가 암반에 근입해야 하는 지반여건인 우리나라에서 LNG터미널 해안구조물에 자주 적용되는 API code의 Design Value의 합리적 접근이 필요한 현실이다. 이는 구조물의 안정성을 만족하며 사업자의 경제성을 충족시켜줄 수 있는 방법으로의 접근을 말한다.
Design Value의 합리적 접근은 단계적으로 이루어져야 하며 이들 값들은 실내시험의 결과들과 비교되고 최근 연구문헌들과도 비교되어 적용되어야 한다고 사료된다. 또한 보령현장에서는 Design Value의 적용성이 인접한 #1부두 운용으로 일부 검증되어 금번 실시설계에서는 현장시험과 실내마찰시험 결과들을 함께 비교 검토하여 설계값으로 적용되었다. 향후 #2부두 시공시 현장재하시험 및 부두 운용으로 최종 검증될 이들 값이 국내 연안에 계획될 Jetty 구조물의 기초 지지력 검토에 유용하게 적용되어지기를 기대한다.
참고문헌
1. “광양 LNG터미널 건설공사 실시계획 보고서” 2000년.
2. “보령 LNG터미널 2-2단계 항만건설공사 실시계획 보고서” 2018년
3. API Recommended Practice 2A-WSD, 2GEO, 2014년.
4. McClelland, B. and Reifel, M.D., 1986,“Planning and Design of Fixed Offshore Platforms” Van Nostrand Reinhold Company.
[본 기사는 저자 개인의 의견이며 학회의 공식 입장과는 관련이 없습니다]
볼트수직이음PHC말뚝 시공법에 관한 기술적 고찰(II)
- 이음말뚝 성능 검증실험을 중심으로 -
1. 개요
5월호에 게재된 기술기사(I)에서는 국내에서 사용이 급증하고 있는 볼트식 수직이음 PHC말뚝에 대한 기술적 수준을 현장 시공안전성능 검증실험 결과를 중심으로고찰하였으며 해당 말뚝의 시공 안전성 성능을 확인할 수 있는 올바른 검증 시험 방법론을 살펴보았다. 김명학 & 최용규(2018)은 최근 발표한 학술논문에서 볼트식 수직이음 PHC말뚝은 이음말뚝의 성능에 크게 미달된다는 것을 밝혔다.
말뚝기초는 국내에서 가장 많이 사용하는 기초형식중 하나이며 구조물의 하중을 상대적으로 깊은 양호한 지지층까지 전달하거나 마찰 저항력을 이용하여 구조물을 안전하게 지지하기 위해 사용된다. 연약지반이나 해안지대의 경우 지반강도가 작고 지지층의 심도가 매우 깊어 말뚝의 길이를 길게 하여야 한다. 하지만 국내에서는 생산성과 운반성을 고려하여 현재 생산되는 말뚝은 1본의 길이를 최대 15m로 제한하고 있다. 따라서 말뚝의 길이가 15m 이상 요구되는 현장에서는 2본 이상의 말뚝을 이음 하여 시공하여야 한다.
국내에서는 표준이음방식으로 용접이음 방식을 규정하고 있으나 볼트 수직이음 방식도 현장에서는 적용되고 있다. 용접이음 방식은 국내에서 일반적으로 사용하는 공법으로 직경이 동일한 상부말뚝의 선단과 하부말뚝의 두부부분을 용접을 통해 길이를 연장하는 공법이다. 볼트 수직이음 방식은 상부말뚝의 선단과 하부말뚝의 두부부분 사이에 볼트 수직이음구를 삽입하여 이음볼트로 수직방향으로 체결하는 방식이다. 기술기사(I)에서 현행 볼트수직이음 방식은 볼트-너트 체결의 기본 개념에 미달되었으며 시공 시 안전성에 심각한 문제가 발생하였고 작업소요시간 및 비용 측면에서도 불리하였다는 것을 고찰하였다.
이 기술기사에서는 볼트 수직이음 PHC말뚝이 이음말뚝의 성능을 충족시키는지 여부를 고찰하였다. 아울러 표준이음방식인 용접이음 PHC말뚝의 성능도 고찰하였다.
2. PHC말뚝 이음 시공 표준 고찰
(1) 이음 표준 분석
말뚝의 지중 근입길이가 15m 이상으로 길어지면 PHC말뚝의 이음은 필수적으로 필요하게 된다. PHC말뚝의 이음관련 표준 규정을 표 1에 요약하였다. PHC말뚝의 이음은 아크용접이음으로 실시하고 수동 또는 반자동용접을 실시하도록 규정하였다.
(2) 이음말뚝이 가져야 할 기본 성능
KS F 4306 해설에서는 ‘2.3.5 이음부의 휨 강도(본체의 4.5) 이음부의 휨 강도는 몸체의 휨 강도와 동등 이상인 것이 원칙이지만, 이음부는 이음 철물 등으로 보강되어 있고 강성도 높고 몸체의 균열 휨 모멘트에 대해서 안전하므로 여기에서는 파괴 휨 모멘트만을 대상으로 하고 있다.’라고 규정하고 있다. 아래에 원문을 첨부하였다.
KS F 4306 해설 2.3.5항에서 설명한 내용에는 다음의 의미를 내포하고 있다. KS F 4306 및 KS F 7001에서 표준이음방식으로 정하고 있는 용접이음 PHC말뚝은 이음하지 않은 말뚝(즉 단본 말뚝)과 동등 이상의 성능을 가지기 때문에 말뚝 성능 자체에 대한 품질 시험은 실시하지 않고 파괴 휨 모멘트 품질 시험만 실시하도록 규정한 것이다. 따라서 파괴 모멘트를 대상으로 품질 검사 시험을 실시하기 이전에 볼트 수직이음 PHC말뚝이 말뚝임을 입증하여야 한다.
이음말뚝은 기본적으로 이음하지 않은 말뚝과 동일한 거동을 나타내어야 한다. 즉 이음말뚝은 1개의 말뚝으로 일체화 거동을 나타내어야 하며 콘크리트 제품이므로 탄성재료의 거동을 나타내어야 한다. 또한 아크용접이음을 표준 이음방식으로 정하고 있으므로 그 외의 이음 방법은 용접이음과 동등 이상의 성능을 가져야 한다.
이음 PHC말뚝은 다음의 3가지 기본 성능을 만족하여야 한다. 이음말뚝의 일체화 거동 및 탄성 거동은 동영상이 첨부되어 있는 그림 1을 통하여 이해할 수 있을 것으로 보인다.
② 탄성 재료 성능(splicedpile.avi)
③ 용접이음과 동등 이상의 품질 성능
3. 이음말뚝의 성능 검증 실험
볼트 수직이음 PHC말뚝의 이음말뚝 성능 검증 시험의 구체적인 계획을 표 2에 나타내었다. 여기서 표준 이음 방식인 용접이음 PHC말뚝의 성능 검증시험도 계획도 함께 실시하였다. 길이 7m의 직경 500mm인 A종 PHC말뚝 2개를 이음하여 시험말뚝으로 사용하였다. 여기서 볼트 수직이음 PHC말뚝을 직항타 또는 경타 시공 후에는 볼트가 풀려 체결력이 심각하게 저하하여 체결력은 80% 이상까지 감소하는 것으로 나타났다(김명학, 2018a; 2018b). 볼트 수직이음 방식의 자체 시방에서는 기준 체결력을 80∼120N·m로 제시하고 있으므로 시공 전 최초 체결력을 100N·m로 하였을 때 직항타 또는 경타 시공 후 잔류 토크치는 20N·m 이하로 남아 있게 되었다. 따라서 잔류 토크치를 20N·m로 하여 체결한 후 시험을 실시하였으며 직항타 또는 경타 시공 후 볼트 수직이음 PHC말뚝의 이음말뚝으로서의 3가지 성능을 분석하기 위함이었다. 이는 이음볼트가 풀린 상태를 모사하여 휨강도 시험을 실시한 것이었으며 이 때 20N·m의 볼트 체결력은 현장 시공 안전성능 검증시험 시 측정한 이음볼트에서 측정한 잔류 토크치보다는 평균적으로 다소 큰 값이었다.
시험은 국토교통연구인프라운영원 첨단재료시험센터에서 실시하였다. KS F 4306에 규정된 휨강도시험 방법에 따라 시험을 진행하였으며 그 개요도를 그림 2에 나타내었다. 국토교통연구인프라운영원 첨단재료시험센터에서 진행한 시험 모습을 그림 3에 나타내었다.
4. 볼트 수직이음 PHC말뚝의 이음말뚝 성능 분석
(1) 시공 전 기준 토크치 이상으로 체결한 볼트 수직이음 PHC말뚝
보통 작업원의 인력으로 체결할 수 있는 토크치로 이음볼트를 체결하였으며 이 때 평균 토크치는 200N·m 이상으로 나타났다. 볼트 수직이음 말뚝에 하중을 단계적으로 증가시켜 파괴상태까지 재하 하였으며 그 결과를 그림 4에 나타내었다. 가장 낮은 하중단계인 20kN에서도 볼트 수직이음 PHC말뚝에서는 볼트 수직이음구에서 V형으로 꺾인 변형 양상이 나타났으며 PHC말뚝 본체는 완전한 직선 형태를 유지하고 있었다. 즉 2개의 별개의 말뚝으로 거동하는 양상을 나타내었으므로 일체화 거동은 전혀 관찰되지 않았다. 그 이후의 하중단계인 40, 60, 80kN의 하중 단계에서는 하중 단계가 증가할수록 V형으로 꺾어진 변형 양상은 더욱 심화되었으며 별개의 직선화된 2개 말뚝 양상은 확연하게 관찰되었다. 즉 볼트 수직이음 PHC말뚝은 일체화 거동을 나타내지 않았고 1개의 말뚝이 아닌 것으로 나타났으므로 이음말뚝의 성능을 전혀 만족시키지 못하였다.
그림 4(a)에서 다음과 같은 변형 양상을 관찰할 수 있었다. 볼트 수직이음 부위의 왼쪽 편 말뚝은 하중의 크기에 상관없이 완전하게 직선 선형으로 변형하였다. 볼트 수직이음 부위에 인접한 오른쪽 편 말뚝 부위에서는 60kN의 재하 하중 이상에서 급격한 변위 상태가 나타났으나 그 이외 말뚝 부분은 직선 선형 형상으로 변형하였다.
(2) 시공 후 이음볼트가 풀린 조건을 모사한 볼트 수직이음 PHC말뚝
그림 5로 부터 이음볼트가 풀린 조건을 모사한 볼트 수직이음 PHC말뚝의 이음 말뚝 성능을 분석하였다. 각 하중 단계에서 볼트 수직이음 PHC말뚝은 이음부위에 대하여 양쪽으로 대칭된 직선 상태의 변위 양상을 나타내고 있었다. 즉 이음부를 기준으로 V형으로 꺾어진 채 2개의 별도의 말뚝으로 거동하는 것을 알 수 있었다. 각 하중 단계에서 하중 제거 시 이음말뚝은 하중 재하 전의 상태로 돌아가지 않는 것을 알 수 있었다. 즉 이음볼트가 풀린 조건을 모사한 볼트 수직이음 PHC말뚝은 탄성체로 거동하지 않는 것을 알 수 있었다. 즉 볼트 수직이음 PHC말뚝은 일체화 거동을 나타내지 않았고 1개의 말뚝이 아닌 것으로 나타났으므로 이음말뚝의 성능을 전혀 만족시키지 못하였다.
(3) 용접이음 PHC말뚝
그림 6으로 부터 용접이음 PHC말뚝의 말뚝성능을 분석하였다. 각 하중 단계에서 용접이음 PHC말뚝은 이음부위에 대하여 양쪽으로 대칭된 곡선 상태의 변위 양상을 나타내고 있었다. 즉 PHC말뚝과 용접이음부가 일체화 되어 1개의 말뚝으로 거동하는 것을 알 수 있었다. 60kN 재하 후 하중 제거 시 약 1.6mm의 미소한 잔류변형이 남아 있으나 용접이음 PHC말뚝이 탄성 거동을 보여 주는 자료로 활용가능한 것으로 판단되었다. 즉 용접이음 PHC말뚝은 탄성체로 거동하는 것을 알 수 있었다. 요약하면 용접이음 PHC말뚝은 1개의 말뚝이었으며 탄성 재료인 것으로 나타났으므로 이음말뚝의 성능을 만족시켰다.
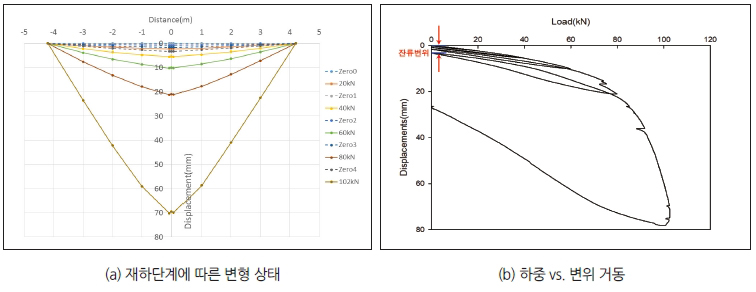
(4) 잔류변위 분석
시공 전 볼트 수직이음 PHC말뚝의 잔류변위는 60kN의 하중 단계에서도 6.0mm 정도까지 나타났다. 시공 후 이음볼트가 풀린 조건을 모사한 볼트 수직이음 PHC말뚝의 누적 잔류 변위는 60kN에서 11.4mm 정도 발생하였으며 하중이 증가하여 80kN의 재하 단계에서는 누적 잔류변위가 15.6mm 정도까지도 나타났다. 용접이음 PHC말뚝의 잔류 변위는 60kN의 하중단계까지는 1.8mm 정도 발생하였으며 그 이후 파괴하중에 접근하는 경우 즉 80kN에서는 3.6mm정도까지는 발생하였다.
시공 후 이음볼트가 풀린 조건을 모사한 볼트 수직이음 PHC말뚝의 잔류 변위는 용접이음 PHC말뚝의 잔류 변위보다 4.3 ∼ 6.0배만큼 크게 나타났으며 이는 이음품질 성능 측면에서 볼트 수직이음 PHC말뚝이 용접이음 PHC말뚝에 크게 미달되는 것을 의미하였다(그림 7 참조).
(5) 재하 단계에 따른 이음부 변위
2가지 이음 PHC말뚝에 대하여 재하 단계에 따른 볼트 수직이음부와 용접이음부 중앙의 변위를 측정하여 그림 8에 나타내었다. 200N·m 이상의 토크치로 체결한 볼트 수직이음 PHC말뚝의 경우 80kN까지, 시공 후 이음볼트가 풀린 상태를 모사한 20N·m의 토크치로 체결한 볼트 수직이음 PHC말뚝의 경우 80kN(일부 말뚝에서는 60kN)까지, 용접이음 PHC말뚝의 경우 100kN 단계까지 이음부 변위를 측정할 수 있었다. 시공 전 200N·m 이상의 토크치로 체결한 볼트 수직이음 PHC말뚝과 시공 후 이음볼트가 풀린 조건을 모사한 볼트 수직이음 PHC말뚝의 변위는 비슷한 수준이었다. 볼트 수직이음 PHC말뚝의 파괴하중인 재하 하중 80kN까지는 용접이음 PHC말뚝의 변위는 볼트 수직이음 PHC말뚝의 1/3(40kN이하의 하중 단계)∼1/2(60kN이상의 하중 단계) 수준이었으며 그 이후 하중 단계에서는 변위는 크게 증가하여 소성변형단계에 도달하였다.
(6) 이음말뚝들의 변형 상태 분석 및 PC 강봉의 정착
용접이음과 볼트 수직이음을 변형 상태를 비교하였다. 변위가 유사하게 발생한 하중 단계를 중심으로 이음말뚝들의 변형 상태를 비교하였다(그림 9 참조). 여기서 용접이음에서는 80kN의 재하 단계와 볼트 수직이음에서는 60kN에서 변위가 유사하게 발생하였으며 두 개의 그래프를 비교하면 용접이음은 아래로 볼록한 곡선 형상으로 변형하였으며 볼트 수직이음은 직선 선형형상으로 변형하는 것을 관찰할 수 있었다.
볼트 수직이음 PHC말뚝의 변형 상태가 아래로 볼록한 형상으로 변형되지 않고 직선 형상으로 변형되는 것은 PC강봉이 볼트 수직이음구의 상부판 또는 하부판에 정착되어 있지 못하기 때문이었다. 즉 용접이음을 위하여 생산된 PHC말뚝의 PC너트 또는 마밀라슈의 탭경에 볼트 수직이음구의 상부판 또는 하부판을 이음볼트로 체결시키게 되므로 PC강봉이 정착될 수가 없다.
KS F 4306의 ‘8. 제조 방법 8.6 이음부 b) PC강재의 끝부는 이음부에서 이음 철물에 정착되어야 한다.’고 명확하게 규정하고 있다. 볼트 수직이음 PHC말뚝의 경우 PC강봉이 볼트 수직이음철물에 정착되어 있는지를 입증해야 한다. 참고로 ‘정착(anchorage)은 철근 끝이 콘크리트에서 빠져나오지 않도록 고정하는 것을 말한다.’라고 정의되어 있다.
(7) 이음말뚝들의 이음 성능 종합 분석
KS F 4306 해설 ‘2.3.5 절에서 규정하고 있는 바와 같이 KS F 4306 및 KS F 7001에서 표준이음방식으로 정하고 있는 용접이음 PHC말뚝은 이음하지 않은 말뚝(즉 단본 말뚝)과 동등 이상의 성능을 가지기 때문에 말뚝 성능 자체에 대한 품질 시험은 실시하지 않고 파괴 휨 모멘트 품질 시험만 실시하도록 규정한 것이다. 따라서 파괴 모멘트를 대상으로 품질 검사 시험을 실시하기 이전에 볼트 수직이음 PHC말뚝이 말뚝임을 입증하여야 한다. PHC말뚝은 콘크리트가 주재료이므로 탄성 성능을 가져야 하고 휨 강도 시험 시 곡선 형상으로 변형하여야 하므로 볼트 수직이음 PHC말뚝도 이러한 성능을 기본적으로 만족시켜야 한다.
볼트 수직이음 PHC말뚝과 용접이음 PHC말뚝의 휨 강도 품질 성능을 분석하여 참고로 수록하였다. 표 3에서 알 수 있듯이 볼트 수직이음 PHC말뚝은 이음말뚝의 성능을 만족시키지도 못하였으며 휨 강도 품질 측면에서도 일부 시험체에서는 기준값에 미달되는 것으로 나타났다.
PHC말뚝의 이음에서 가장 취약한 부분은 PC너트와 PC강봉의 헤드 부분이다. 볼트이음의 체결력에 관련 없이 파괴는 대부분 PC강봉 헤드부에서 발생하였으며 극히 일부 PC너트가 파괴되는 현상이 발생되기도 하였다. 즉 PC강봉의 헤드부는 PC너트에 고정되어 있으며 PC강봉에 도입된 긴장력을 모두 부담하고 있었으며 따라서 휨 강도 시험 시 PC강봉 헤드부가 절단되어 휨 파괴가 발생하는 것이 관찰되었다. 따라서 이음볼트의 체결 상태가 휨 강도 시험 시 파괴모멘트와는 직접적인 관계는 없는 것으로 분석되었다. 다만 휨 강도 시험 시 발생하는 변위는 이음볼트의 체결 상태와 직접적인 관련이 있었으며 체결력에 약할 시 변위가 많이 발생하였고 탄성 복원도 적게 발생하게 되었다.
용접이음에서는 볼트이음보다 동일한 하중단계에서 변위가 작게 발생하였고 높은 파괴모멘트가 나타났다. 이것은 여러 개의 PC강봉이 휨에 저항하였으므로 높은 휨 모멘트가 나오는 것으로 판단되었다. 즉 휨 강도 시험 시 파괴는 PC강봉 헤드부의 절단에 의해 발생하기 때문이었다.
5. 결언 및 제언
(1) 시공 전 기준 토크치 이상으로 체결한 볼트 수직이음 PHC말뚝에서는 가장 낮은 하중단계인 20kN에서도 볼트 수직이음구에서 V형으로 꺾인 변형 양상이 나타났으며 PHC말뚝 각각의 본체는 완전한 직선 형태를 유지하고 있었다. 그 이후의 하중단계인 40, 60, 80kN의 하중 단계에서는 하중 단계가 증가할수록 V형으로 꺾어진 변형 양상은 더욱 심화되었으며 별개의 직선화된 2개 말뚝 양상이 확연하게 관찰되었다. 따라서 200N·m 이상의 토크치로 체결한 볼트 수직이음 PHC말뚝은 일체화 및 탄성 거동을 나타내지 않았으므로 말뚝 또는 이음말뚝의 기본 성능을 전혀 만족시키지 못하였다.
(2) 시공 후 이음볼트가 풀린 조건을 모사한 볼트 수직이음 PHC말뚝은 각 하중 단계에서 이음부위에서 V형으로 꺾어진 변형 양상을 나타내었으며 PHC말뚝 본체는 각각 직선 상태의 변위 양상을 나타내고 있었다. 각 하중 단계에서 하중 제거 시 이음말뚝은 하중 재하 전의 상태로 돌아가지 않는 것을 알 수 있었다. 20N·m의 토크치로 체결하여 시공 후 이음볼트가 풀린 조건을 모사한 볼트 수직이음 PHC말뚝은 일체화 거동을 나타내지 않았으며 탄성 재료도 아닌 것으로 나타났으므로 볼트이음 부위에서 V형으로 꺾어진 말뚝일 뿐이었다. 즉 말뚝 또는 이음말뚝의 기본 성능을 전혀 만족시키지 못하였다.
(3) 재하단계에 따른 이음부 변위 및 재하 하중 제거 후의 잔류 변위, 이음 PHC말뚝의 파괴하중 및 3가지 기본 성능 등을 비교하였는데 볼트 수직이음 PHC말뚝의 이음 품질은 용접이음 PHC말뚝의 이음 품질에 크게 미달되었다. 또한 1개의 볼트 수직이음 PHC말뚝의 휨파괴모멘트는 기준값에도 미달되었다.
(4) KS F 4306 해설 ‘2.3.5 절에서 규정하고 있는 바와 같이 표준 이음방식이 아닌 볼트 수직이음 PHC말뚝에서는 파괴 모멘트를 대상으로 품질 검사 시험을 실시하기 이전에 볼트 수직이음 PHC말뚝이 말뚝임을 입증하여야 한다. PHC말뚝은 콘크리트가 주재료이므로 탄성 성능을 가져야 하고 휨 강도 시험 시 곡선 형상으로 변형하여야 하므로 볼트 수직이음 PHC말뚝도 이러한 성능을 기본적으로 만족시켜야 한다. 그 다음 단계로 용접이음 부위의 휨 강도를 검토해야 한다. 따라서 이 같은 규정은 용접이음 이외의 이음 방식 경우에도 동일하게 적용되어야 하며 어떠한 이음방식도 표준 방식인 용접이음과 동등 이상의 품질이어야 한다는 것을 의미한다.
(5) 볼트 수직이음 PHC말뚝의 시공법을 사용하고 있는 5개사에서는 볼트 수직이음된 PHC말뚝이 일체화 거동을 하고 탄성 거동을 하며 용접이음된 PHC말뚝의 성능과 동등 또는 그 이상의 성능을 가진다는 것을 실증적으로 검증하여야 한다.
참고문헌
1. 김명학 (2018a), 확장판선단부착PHC말뚝 및 볼트수직이음PHC말뚝의 안전한 시공법 개발 프로젝트 최종보고서, 2018. 9., pp. 1 ∼ 341.
2. 김명학 (2018b), 확장판선단부착PHC말뚝 및 볼트수직이음PHC말뚝의 안전한 시공법 개발 프로젝트 최종보고서 부록, 2018. 9., pp. A-1-1 ∼ A-13-48.
3. 김명학 & 최용규 (2018), 볼트 수직이음 PHC말뚝과 용접이음 PHC말뚝의 이음부 거동 비교, 한국지반공학회 논문집, 제34권 제12호, 2018년 12월, pp. 107-119.