■ 제8강을 시작하며
2018년 9월 12일 오전 11시경 [그림 1]에서 보는 바와 같이 호주 Perth의 Forrestfield 공항철도 공사중 TBM 터널이 침수되고 상부 도로에 싱크홀(sinkhole)이 발생하는 사고가 발생했다. 본 사고는 호주 도심지 터널공사 공사에 적용되어 왔던 TBM 터널공사에 심각한 영향을 미쳤다. 본 사고를 통해 TBM 터널공사에서 지반 그라우팅과 배면 그라우팅의 품질관리와 피난연락갱(cross passage) 시공상에 여러 가지 문제점이 확인되었다. 특히 도심지 구간을 통과하는 TBM 터널에서의 사고는 조사, 설계 및 시공상의 기술적 문제점을 제기하는 계기가 되었으며, 도심지 TBM 터널구간에서 피난연락갱 사고 원인 및 발생 메커니즘을 규명하기 위하여 철저한 조사를 진행하게 되었다.
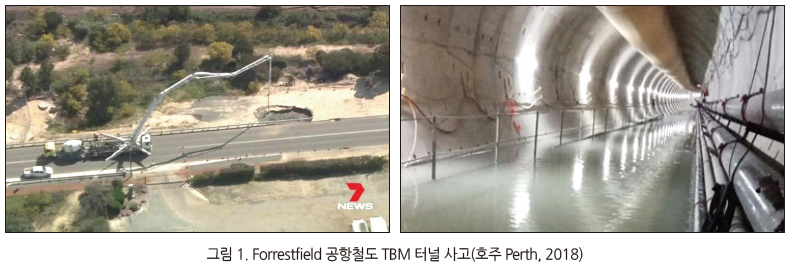
본 고에서는 Forrestfield Airlink 공항철도 프로젝트의 TBM 터널구간에서의 터널침수 및 싱크홀 사고사례로부터, 도심지구간 TBM 터널공사시 피난연락갱 구간의 지반그라우팅, TBM 터널에서의 배면그라우팅, 피난연락통로 시공 등 시공관리상의 문제점을 종합적으로 분석하고 검토하였다. 이를 통하여 본 TBM 터널 사고로부터 얻은 중요한 교훈을 검토하고 공유함으로서 지반 및 터널기술자들에게 기술적으로 실제적인 도움이 되고자 하였다.
1. Forrest-Airport Link 프로젝트
2018년 9월 22일 토요일 오전 11시 45분 경, 피난연락갱(Cross passage) Dundas와 제1터널 라이닝 링인버트 사이의 경계에서 누수(leak)가 발생했다. 누수는 Forrestfileld 역에서 북쪽으로 약 200m 떨어진 피난연락갱 Dundas(CP12) 굴착과정에서 발생했다. 지하수 유입을 막기 위해 즉각적인 노력을 기울였지만, 상당한 수압으로 인해 유입량은 초당 약 50리터로 증가했고 그 결과 200m3 이상의 모래와 토사가 터널로 유입되었다.
9월 23일 일요일 아침, Dundas 도로에 인접한 지표면에 싱크홀이 형성되었다. Dundas 도로의 일부 구간은 폐쇄되었고, 예방 조치로 두대의 TBM이 모두 중단되었다. 그날 늦게 전문시공자가 인접한 TBM 터널 주변 인버트에 그라우트를 주입하기 시작했고, 며칠 후 유입량이 크게 감소했으며, 지하수 유입은 10월 3일 수요일에 완전히 멈추게 되었다. 지하수의 압력과 관련 하중으로 인해 피난연락갱 지점 근처에서 약 16개의 터널 링 약 26m구간이 변형되었다.
피난연락갱 Dundas의 시공과정은 지반 조건과 기술 분석에 기초한 협의된 과정을 따랐다. 피난연락갱에 대한 시공기술은 일반적인 것으로 사고 이후 시행된 관련 조치의 범위도 적절해 보이지만, 다양한 전문가들이 사고에 대한 조언을 제공하기 위해 철저한 조사를 수행하였으며, 향후 피난연락갱 시공을 위한 추가 예방지침을 제공하고자 하였다.
본 고는 이번 TBM 터널사고에 대한 관련 정보(설계 및 시공), 사고 당시 및 사고이후 시행된 조치를 정리 분석하고자 하였다. 또한 작업자의 안전이나 사고기간 동안 이해관계자들이 어떻게 처리되었는지와 같은 인적 요인보다는 지질리스크 등을 지반공학적 특성과 같은 기술적 요인에 초점을 맞추고자 하였다. 중요한 점은 이미 발생한 터널 사고에 대하여 정확한 원인을 규명하고 적절한 복구대책 방안을 수립함으로서 향후 이와 유사한 터널 사고가 발생하지 않도록 기술적 교훈을 남겨서 관련기술자들에게 도움이 되어야 한다는 것이다.
1.1 프로젝트 개요
Forrestfileld-Airport Link 공항철도는 호주와 서호주 정부가 공동으로 자금을 지원하며 Perth 동부 교외에 새로운 철도 서비스를 제공을 목적으로 계획되었다. [그림 2]에서 보는 바와 같이 공항 연결철도에는 Perth 공항 1개 역을 포함해 3개 역 신설과 기존 육상·도로망에 차질이 최소화될 수 있도록 병설 터널 8km가 포함돼 있다. 이와 함께 설계에는 비상시 승객들이 한 터널에서 인접한 터널로 대피할 수 있도록 12개의 본선터널을 연결하는 피난연락갱을 시공하는 내용이 포함되었다. 또한 터널과 3개의 비상대피용 수직구사이에 피난연락갱 연결이 있어 노선상에 정렬을 따라 총 15개의 피난연결통로를 제공하였다. 2016년 4월 PTA는 Salini Impregilo-NRW JV(SI-NRW)와 설계, 시공 및 유지보수 계약을 체결했다.
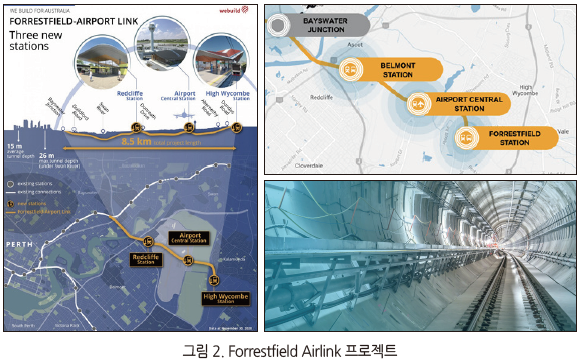
본선터널은 [그림 3]에서 보는 바와 같이 TBM 터널공법으로 계획되었으며, 발주처는 터널 굴진을 위해 Herrenknecht사의 직경 7.1m의 Variable Density Multi Mode TBM 2대(TBM 장비명 Grace와 Sandy)를 지정하였으며, 공항내 사이트에서 고밀도 슬러리를 사용하여 TBM 장비를 슬러리 모드로 작동하도록 하였다. 본 TBM은 카르스트 지형조건에 적용하기 위해 개발되었으며, 본 현장의 하저구간을 통과하는 지질 및 지반조건을 고려하여 성능이 우수하고 안전한 옵션으로 본 장비를 선정하였다.
1.2 지반 특성
본 프로젝트는 터널링을 위한 독특한 지질 조건을 제시하며, 다양한 지반 조건에 TBM을 적용하는 데 있어 일부 불확실성 요소가 예상되었다. 지반 조건은 [그림 4]에 나타나 있으며, 일반적으로 다음과 같은 지반 조건으로 구성된다.
● Fill - 일반적으로 미세하고 거친 모래로 구성되며, 때때로 실트, 점토 및 유기 물질이 포함된다.
● Sandy Alluvium - 주로 스완강에 의해 퇴적된 모래 퇴적물로 구성되어 있으며 현재 스완강 계곡과 범람원에 국한된다.
● Swan River Alluvium - 매우 부드럽고 단단하며 검은색 유기 포화 실트 및 고가소성 점토로 구성되어 있으며, 이는 종종 조개껍질과 조개껍질 조각을 포함하고 있다. 이 부드러운 진흙들은 여전히 스완강 내에 퇴적되어 있으며 압축성이 높다.
● Bassendean Sand - 제안된 대부분의 노선에 걸쳐 지표면에 노출되며 미세~중간 입자의 느슨함~중간 밀도가 높은 모래로 구성된다. 본 모래층은 원래 해안 사구시스템으로 퇴적되었지만 ‘Coffee Rock’으로 알려진 얇고 밀도가 높은 철이 풍부한 수평층을 포함하고 있다.
● Guildford Formation - 호층을 이루는 모래, 실트 및 점토로 구성되며, 느슨한 모래에서 매우 밀도가 높고 부드러운 모래에서 매우 단단한 점토까지 다양하다.
● Ascot Formation - 석회질 모래와 호층 모래와 쉘 층 사이에 있는 약하고 잘 굳은 칼레나이트로 구성된다. 본 층은 또한 시멘트 층 사이 또는 그 안에 모래로 채워진 빈 공간과 작은 구멍을 포함하고 있으며, 일반적으로 동쪽에서 서쪽으로 나이가 감소하면서 점진적으로 디그래이딩되는 해안선을 따라 형성되었다.
● Osborne Formation - 검은색, 강도가 매우 낮은 사암, 주로 미세한 입자로 구성된다. 오스본 층은 본 프로젝트의 목적을 위해 이 지역에서 효과적인 기반암층을 형성하였다.
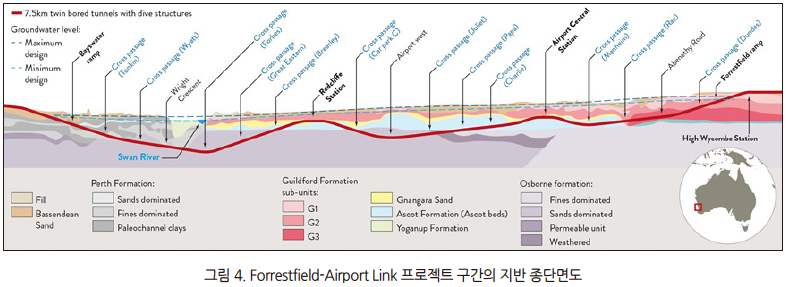
PTA(Public Transport Authority)와 정부는 어려운 지반조건을 인식하고 광범위한 지반 조사를 실시했다. 지반공학적 리스크는 Forresfield-Airport Link 프로젝트 계획에 요약되어 있다. PTA의 지반조사 결과는 SI-NRW와 공유되었으며, SI-NRW는 PTA의 결과를 확인하기 위해 추가적인 지반조사를 수행했다. 프로젝트 계약이 체결시, 관련된 모든 당사자들은 터널링과 관련된 잠재적인 문제점에 대하여 공유하였다.
피난연락갱 Dundas 위치에 있는 최초 30m의 지반은 Bassendean 모래와 Guildford 층으로 구성되어 있으며, [그림 5]에 나타난 바와 같이 세 가지 주요 단위로 나눌 수 있다.
● Sub-unit G1 - Bassendean 모래 바로 아래에 위치하고 미립분 함량이 높은 점토질 모래로, 투수성이 낮은 매우 단단하고 단단한 모래질 점토층이다.
● Sub-unit G2 - G1에 비해 미립분 함량이 낮은 점토질 모래층으로, 시험결과 낮은 투수성에서 높은 투수성까지 다양한 층이 존재하는 점착력이 높은 조밀한 모래층이다.
● Sub-unit G3 - 약간의 미립분을 포함한 실트질 모래층으로서 시험결과 매우 조밀한 모래층의 투수성이 있는 압밀층이다. 피난연락갱 Dundas 위치에서 TBM 터널은 약 9미터의 토피고를 가지며, [그림 5]에 지표면 및 다양한 지반층에서의 Dundas의 위치가 나타나 있다.
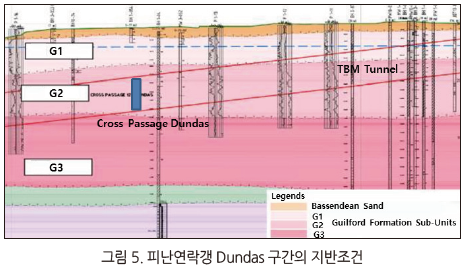
1.3 프로젝트 보험
발주처인 PTA는 Forresfield-Airport Link 프로젝트를 위해 Principal Controlled Insurance 접근 방식을 채택했다. 이는 기본적으로 PTA가 다음과 같은 의사결정 또는 조치로 이어지는 의사결정 프로세스를 통제한다는 것을 의미한다.
● 가입한 보험의 종류
● 가입한 책임 한도
● 보증 범위
● 공제 수준
● 클레임 관리
또한 PTA가 컨트롤하는 보험정책은 Perth Airport Pty Ltd(PAPL) 및 SI-NRW(모든 하도업체 포함)를 포함한다. 발주처(PTA)와 시공자(SI-NRW)간의 리스크 공유 접근방식을 통하여 지반조건 불확실성에 대한 체계적인 리스크 관리전략을 채택하였으며, 이러한 리스크 관리는 대형 지하 인프라 건설 계약의 조달 및 관리에 적용되고 있다. 이전의 계약 관행은 지반조건에 대한 리스크를 시공자에게 이전하는 경향이 있었다.
보험적용을 위한 최상의 조건을 얻기 위해 PTA는 보험사들에게 리스크 관리와 특히 지반 조건의 불확실성에 대해 체계적이고 엄격한 접근 방식을 적용하고 있음을 입증해야 한다. 국제 터널링 보험그룹(ITIG, International Tunnelling Insurance Group)의 실무방칙에 따르면, 이는 제안서 요구 단계에서 기준 지반조건 문서를 이용하는 시공자에게 지반공학적 정보를 완전히 공개함으로써 리스크 공유 접근방식이 가장 잘 달성될 수 있다.
프로젝트에 가장 유리한 보험조건을 찾기 위해 여러 명의 프로젝트 직원이 2016년 런던을 방문하여 주요 보험사를 만나 리스크 저감 전략을 강조하고 프로젝트에 대한 문의에 응답했다. 리스크 공유 접근방식은 이전의 두 개의 Perth 철도 터널 프로젝트뿐만 아니라 서호주의 주요 도로 프로젝트에서 정기적으로 채택되었다. 이와 같은 리스크 공유 접근방식을 통해 프로젝트 공사와 관련된 보험 비용을 예측하는 데 상당한 절감 효과를 얻었다.
피난연락갱 Dundas 사고와 가장 관련이 있는 보험정책에는 계약 공사보험-재물 피해(Material Damage) 특약과 시공 리스크 일반 책임 보험이 포함된다. 근본적으로 본 사고와 관련하여 재물 피해 특약은 공사장과 주요 설비 및 장비(터널 포함)의 공사에 적용된다. 일반배상 책임보험은 제3자의 이익(제3자 유틸리티 및 Dundas 도로에 대한 보강작업에 대한 잠재적 영향 포함)을 포함한다.
본 프로젝트의 보험 담당자들은 사고 발생한 직후 연락을 받은 첫 번째 이해 관계자들 중 한 명으로 현장조사를 통하여 목격자들의 진술과 공유된 기술 보고서를 바탕으로 사고 보고서를 작성했다. 프로젝트 팀이 보강 요구사항과 방안을 검토하는 동안 발주처 PTA와 시공사 SI-NRW가 계속 적극적으로 참여하였다.
2. 피난연락갱 Duncas 시공 개요 및 특성
2.1 피난연락갱 시공 기술
오스본층의 암반층 이외 지반에서 피난연락갱을 안전하게 시공하기 위해서는 굴착 작업을 시작하기 전에 지반을 개량해야 한다.
Wyatt, Forbes 및 Great Eastern 피난연락갱은 Osborne 층 구간에 계획되어 있으므로 사전 지반 안정화작업(prior ground stabilization)이 필요하지 않는다. 반대로 피난연락갱이 공항부지 외부 또는 랜드사이드(공항 부지내에서 공항 제한구역에 바깥)에 위치한 경우에는 터널위 지상에서 제트 그라우팅을 수행하기 위해 특수 장비가 적용된다. 안정화된 지반 블록을 만들기 위해 피난연락갱을 둘러싼 지반(터널의 중심선에서 중심선까지)을 개량하게 된다.
참고로 지반 안정화 작업은 에어사이드(공항부지의 제한구역내 구간)내에 피난연락갱 구간에서는 적용할 수 없다. 이러한 경우 지상접근에 대한 제한 때문에 교차로 주변의 지반은 터널내에서 지반동결로 처리되어야 한다. 또한 피난연결갱은 공항 활주로와 유도로 아래에 위치하는 것이 제한된다.
기본적으로 안정화된 지반은 피난연락갱 위와 아래로 최소 2m 확장되며 터널 중심선에서 중심선까지 확장되어 피난연락갱 굴착구간을 캡슐화하게 된다. 터널 및 피난연락갱이 부분적으로 Osborne 층에 위치하기 때문에 지반 안정화가 부분적으로만 적용되는 경우가 있으며, 이 경우 지반 안정화가 필요하지 않는다. 굴착이 발생하는 피난연락갱의 중심부는 피난연락갱 및 터널의 상하로 안정화된 지반에 의해 밀폐되어 있어 일반적으로 안정화되지 않는다. 안정화된 지반은 피난연락갱의 양쪽으로 최소 2m 이상 연장된다.
피난연락갱에 대한 공사를 시작하기 전에 본선터널 굴착과 터널 라이닝의 바깥면(배면) 사이의 간극(gap)을 이중요소의 컨택그라우트로 처리하여 빈 간극을 채워야 한다. 이러한 처리를 배면 그라우트(annuls grout)라고 하며 세그먼트 링을 설치하는 동안 시공된다.
피난연락갱 입구는 각 터널의 터널 라이닝에 볼트로 고정된 반달형 강재 프레임(half-moon steel frame)의 설치를 통해 보강된다. 이 프레임은 터널을 지지하고 피난연락갱 오픈에 필요한 터널 라이닝 섹션을 제거할 수 있다. 그런 다음 프리캐스트 터널 세그먼트는 원형 콘크리트 톱을 사용하여 피난연락갱 입구에서 절단되고 기계식 암반브레커를 사용하여 분리된다.
피난연락갱 굴착은 [그림 6]에서 보는 바와 같이 지반상태에 따라 약 1.2m 전방으로 굴진하게 되고, 굴진 후에 격자지보(강지보)를 설치하고 지반은 1차 라이닝 역할을 하는 강섬유 보강 숏크리트 200mm로 지반을 보강한다. 지반상태가 양호하지 않은 경우, 격자지보 설치전에 숏크리트 25mm 실링층을 적용하고 격자지보 간격을 줄일 수 있다. 이 프로세스는 굴착작업이 다른 터널에 도달할 때까지 반복되며, 이때 이전에 절단된 세그먼트는 교차로 내부에서 기계식 암반브레커를 사용하여 제거된다.
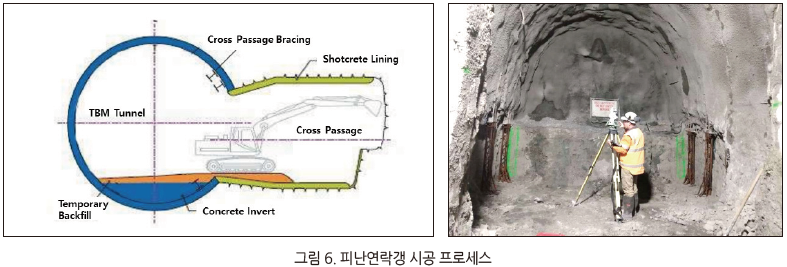
피난연락갱 굴착이 완료되면 굴착기와 기계식 브레커의 조합을 사용하여 피난연락갱의 인버트를 굴착하게 되며, 강섬유 보강 숏크리트가 피난연락갱 인버트에 적용되어 일차 라이닝 적용이 완료되며, 이후 방수포과 부직포로 구성된 방수시스템이 설치된다. 그 다음에는 영구 지보재로서 최종 라이닝을 형성하는 숏크리트 또는 현장타설 콘크리트 라이닝을 적용하게 된다. 그런 다음 동일한 프로세스가 피난연락갱 측벽과 천단부에 대해 반복됩니다. 마지막 단계는 피난연락갱이 본선 터널과 접하는 철근 콘크리트 칼라의 시공으로 칼라가 완성되면 터널에서 반달 강재프레임이 제거되어 피난연락갱 구조가 완성된다.
[그림 7]에는 Duncas 피난연락갱의 단면이 나타나 있다. 그림에서 보는 바와 같이 피난연락갱은 마제형 단면으로 NATM 공법으로 굴진하도록 설계되었다.
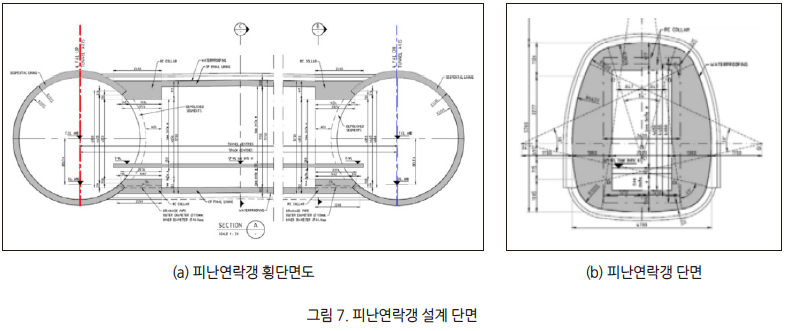
2.2 지반그라우팅 및 피난연락갱 시공
Dundas 사고지점의 지반개량공사는 2017년 말에 진행되었다. 지반보강공법으로 제트 그라우팅공법이 적용되었으며[그림 8], 그라우팅홀은 매립된 유틸리티의 존재로 인해 지상에서 경사져 있었다. 또한 [그림 9]에 나타난 바와 같이 피난연락갱 주변의 지반보강을 위해 지반동결공법이 적용되었다. [그림 10]에는 지반동결공법 시공장면이 나타나 있다.
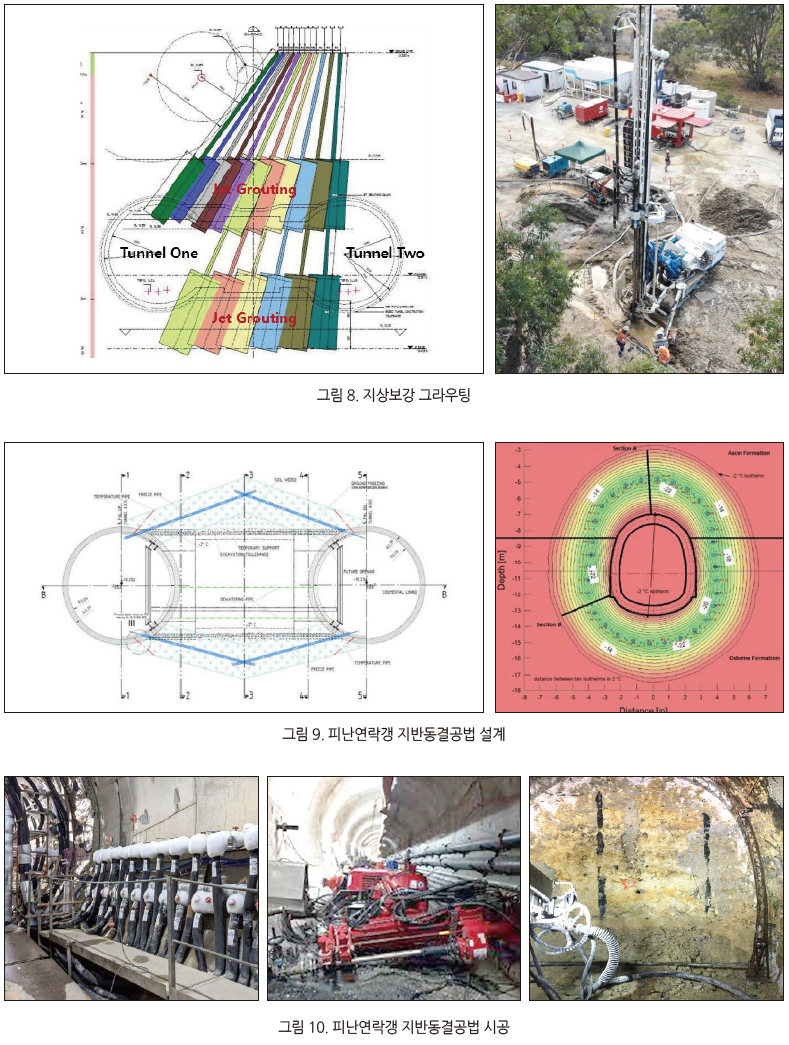
피난연락갱 굴착이 시작되기 전에 반달 모양의 강재프레임은 각각 6월 27일과 7월 16일에 두 터널에 설치되었다. 1번 터널의 세그먼트 라이닝은 7월 9일에 절단(119링)되어 9월 10일에 분해되었고, 2번 터널의 세그먼트 라이닝은 7월 23일에 절단(118링)되어 9월 11일에 분해되었다. [그림 11]에는 사고지점의 본선터널과 피난연락갱의 단면이 나타나 있으며, [그림 12]에는 사고지점의 본선터널과 피난연락갱의 횡단면이 나타나 있다.
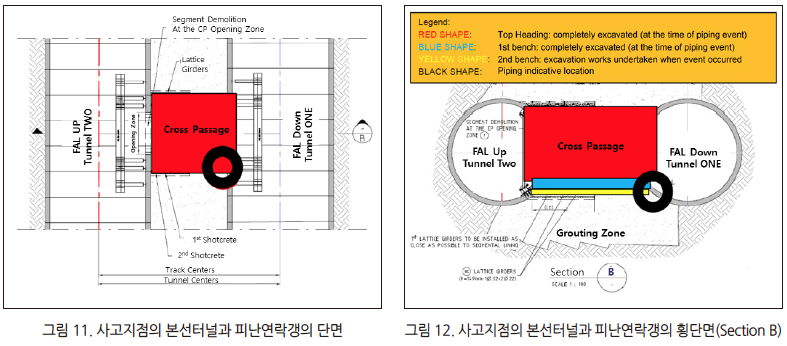
피난연락갱 Dundas의 상반 굴착은 9월 11일 2번 터널에서 시작되었다. 각 굴착 라운드마다 숏크리트와 격자지보를 설치하여 위에서 설명한 NATM 공법을 이용하여 굴착을 진행하였다. 상반 굴착 및 숏크리트는 9월 21일에 완료되었으며, 그 후 9월 22일에 첫 번째 하반 굴착(제트그라우팅된 지반내)이 완료되어 남은 두께 200-300mm 정도만 제거되었다. 사고이전까지 어떠한 문제도 발생하지 않았으며 특이한 것도 관찰되지 않았다.
3. TBM 터널 사고 현황
3.1 사고 개요
9월 22일에 제트그라우팅 지반에서 두 번째 하반 굴착이 시작되었다. 피난연락갱의 90%가 성공적으로 굴착되었을 때, 약 오전 11시 45분에 118번 링의 1번 터널 라이닝 인버트에서 지하수와 진흙이 피난연락갱으로 유입되기 시작했다.
시공사는 누수(leak)를 막기 위해 즉각적인 조치를 취했다. 처음에는 헤센 재료와 모래주머니로 구멍을 막아서 흐름을 막았다. 이러한 조치들은 성공적이지 못했고 지하수와 진흙이 1번 터널로 계속 흘러 들어갔다. 시공사는 지반 교란을 감시하기 위해 현장관리자를 지상에 즉시 배치했다.
용수는 10mm 직경에서 100mm 직경으로 점차 크기가 증가하여 지하수와 실트가 추가로 유입되어 분당 약 50L의 최고 속도에 도달했다. 예방 조치로 두 TBM 모두 약 1주일간 모든 작업이 중단되었다. 토요일 오후 늦게 사고 주변에 300m 배제 구역이 설정되었고, Dundas 도로는 Sorenson 도로와 북쪽 교차로 사이의 교통이 통제되었다. 일요일 이른 아침 Dundas 도로 옆의 지표면에 싱크홀이 형성되었다.
[그림 13]에는 사고직후의 터널 내부가 완전히 침수된 모습과 배수후의 터널 내부의 모습으로 현장에서 응급조치로 사용한 고무보트를 볼 수 있다.
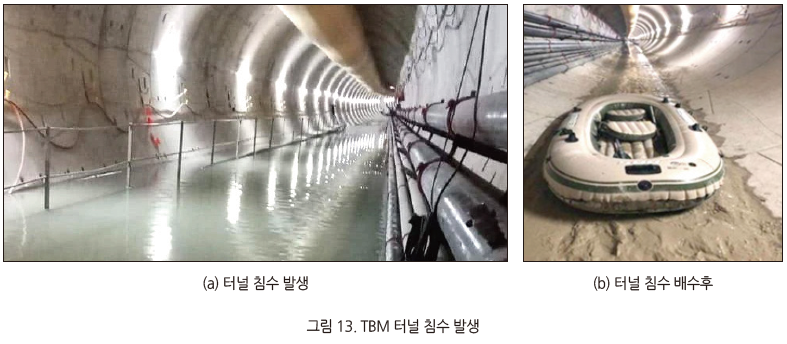
3.2 싱크홀 발생
누수가 처음 발생한 지 약 16시간 후인 9월 23일 일요일 이른 아침(오전 4시경)에 1번 터널 위 지표면에 114번 링에서 120번 링까지 확장된 싱크홀이 나타났다. 싱크홀은 Dundas 도로와 평행하게 형성되었으며 처음에는 길이 약 8m, 폭 약 3m, 깊이 약 3.5m 였다. 싱크홀은 처음에는 도로가 가라앉지 않았지만, 나중에는 도로 표면 아래 지지대가 없어 도로 가장자리까지 부서졌다.
[그림 14]에는 Dundas 도로에서 발생한 싱크홀 모습이 나타나 있다. [그림 15]에는 6] TBM 터널과 피난연락갱 및 싱크홀의 현황을 보여주고 있으며, [그림 16]에는 보다 상세한 현황이 나타나 있다.
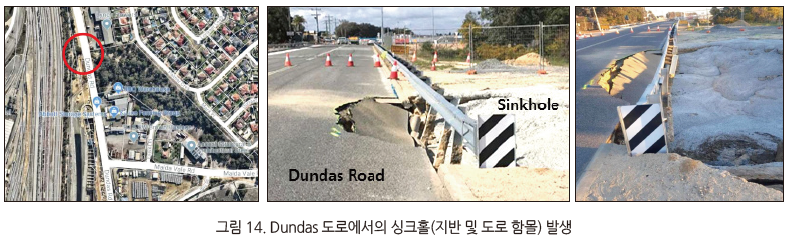
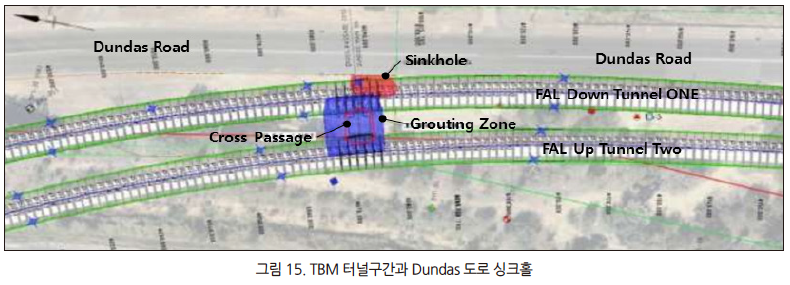
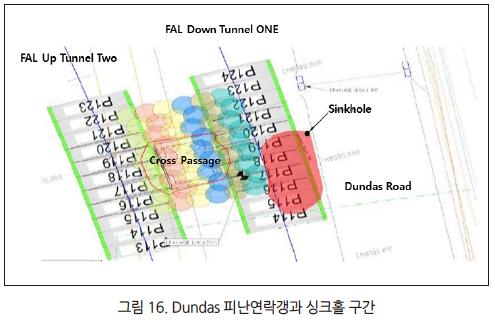
더 이상의 지반 함몰을 제한하기 위해, 특수 실링 혼합물이 믹스된 약 90m2의 린콘크리트(lean concrete)를 여러 대의 콘크리트 트럭에 부착된 콘크리트 펌프를 사용하여 지표면에서 구멍으로 펌핑했으며(그림 17), 이 결정은 시당국과 협의하여 수행되었다.
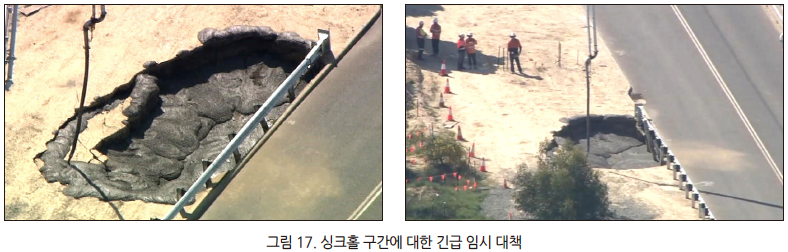
3.3 터널 손상
9월 23일 초부터 여러 가지 시멘트 및 러버 혼합물이 누출에 인접한 터널 세그먼트의 인버트에 주입되었다. 이것은 지하수의 흐름을 초당 10L에서 12L 사이로 안정시켰다. 그 후, 지하수의 흐름이 이전에 존재했던 실트를 더 이상 포함하지 않는 동안 저압 그라우팅이 계속되었다. 10월 3일에는 용수가 상당히 깨끗해졌고 용수를 완전히 차단하기로 결정했다. 긴급 유입수 완화(emergency water relief)가 필요한지를 결정하기 위해 피에조미터는 (압력을 줄이기 위해) 지하수위와 피난연락갱의 인버트 하부 압력을 계속 모니터링했다.
사고의 결과로 터널 라이닝의 일부 변위가 발생했다. Dundas 피난연락갱의 굴착에 앞서 피난연락갱 시공의 다양한 단계에서 내공단위 수렴을 계측하기 위해 5개의 프리즘이 설치되었다. 이 프리즘은 피난연락갱을 굴착하는 동안 안쪽으로 1mm부터 사고가 발생한 후 7mm, 9월 29일 최대 변위 133mm까지 다양한 값이 계측되었다.
라이닝에 대한 상세 조사결과 피난연락갱의 가까운 쪽에 있는 110번 링까지, 그리고 피난연락갱의 먼 쪽에 있는 125번 링까지, 세그먼트가 잘 배치되어 사고 후 과응력이나 불리한 변형의 징후는 보이지 않았다. 114번 링과 122번 링 사이에 원래 원형 터널 단면은 터널의 왼쪽 상단과 오른쪽 하단 사이의 직경이 증가하고 반대쪽 경사 직경이 짧아지는 타원형으로 변형되었다. [그림 18]의 다이어그램은 손상된 단면을 통해 터널 형태의 변형을 보여주고 있다.
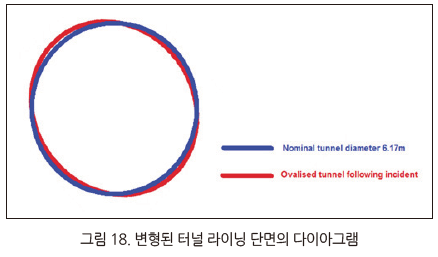
터널 직경에 대한 계측은 레이저 거리계를 사용하여 수행되었다. 예를 들어, 115번 링에 대한 계측에서 필요한 길이가 6.17m인 것과 대조적으로 왼쪽 위에서 오른쪽 아래로 6.31m, 오른쪽 위에서 왼쪽 아래로 6.11m의 측정값이 나왔다. 1번 터널의 단면 변화는 113번 링에서 123번 링 사이에서 가장 크게 나타났다. 피난연락갱 근접부(링 111과 113 사이)과 피난연락갱 이후 구간(링 123과 124)에는 변형된 구간과 변형이 되지 않은 구간으로 변화하는 전환 영역이 확인되었다. 이러한 찌그러짐(ovalization)은 터널 라이닝면에 인장 균열, 터널 세그먼트 사이의 단차 또는 깨짐 등 다양한 변상에 영향을 미쳤다.
[그림 19]에는 사고구간 주변에서 관찰된 콘크리트 세그먼트 라이닝의 손상 및 변상의 모습이다.
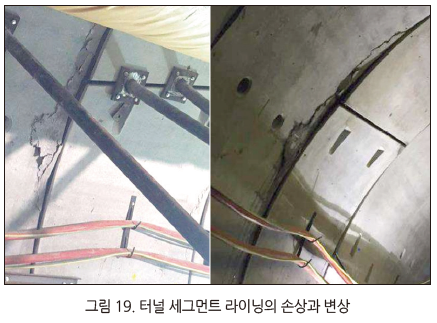
면밀한 모니터링을 통하여 1번 터널 축의 추가 이동 또는 균열, 단차 및 깨짐을 포함한 터널 라이닝 링의 변형과 손상을 계속 기록하였다. 또한 2번 터널 및 피난연락갱 Dundas는 터널 세그먼트에서 과도한 응력이나 예상치 못한 변형의 징후는 확인되지 않았다.
3.4 주변 지장물 손상
사고 당시 인접한 2개의 고압 가스관이 충격을 받았을 수 있다는 우려가 제기되었지만, 상세 조사결과 사고이후 가스관에서 약 2mm 정도의 변위가 발생하였고 전반적으로 가스관에는 이상이 없는 것으로 확인되었다. 468mm APA 파이프라인과 200mm ATCO 가스 파이프라인이 터널에 근접해 있기 때문에 시공사(SI-NRW)는 추가 거동여부를 확인하기 위해 두 파이프라인과 인근 Vocus 광섬유 케이블을 계속 모니터링하였다. 이러한 주변 지장물의근접성은 피난연락갱 굴착 이전에 진행된 제트 그라우팅 오버레이에 나타나 있으며, [그림 20]에는 터널 노선주변의 주요 지장물 현황이 나타나 있으며, 주요 특징은 다음과 같다.
● Vocus 광섬유 케이블은 Dundas 도로 서쪽 10m 지점에 있으며, 100mm PVC
● APA 파르멜리아 고압 가스관은 Dundas 도로에서 서쪽으로 13m 떨어진 곳에 있으며, 직경 450mm의 강재
● ATCO 가스 파이프라인은 Dundas 도로에서 서쪽으로 16m 떨어진 곳에 있고, 터널 중앙 위에 있으며, 파이프라인은 200mm 강재
4. 응급 조치 및 복구 방안
4.1 임시 보강 조치
초기 임시 지지시스템은 터널 라이닝 세그먼트의 추가 손상을 완화하기 위해 설치되었다. 여기에는 두께 5.5mm, 직경 75mm의 강재 그라우트 파이프 6개가 포함된다. 강관의 양 끝을 보강재가 장착된 20mm 두께의 강판에 용접하여 추가 이동 시 하중을 더 잘 분산시켰다. 이것들은 반달 모양의 강재 프레임의 수직 기둥에 기대어 세워졌다.
또한 C자형 강재 프로파일과 Hilti 앵커 볼트를 사용하여 각 링의 세그먼트를 봉합하고 균열 또는 경미한 상대적 움직임이 관찰된 영향을 받는 영역의 각 인접 링에 연결했다. 또한 기존에 설치되었던 파이프 및 플레이트 시스템을 교체하기 위해 터널링 작업과 충돌하지 않도록 배치된 종방향 빔 및 추가 임시지지 강재의 설치를 고려하였다.
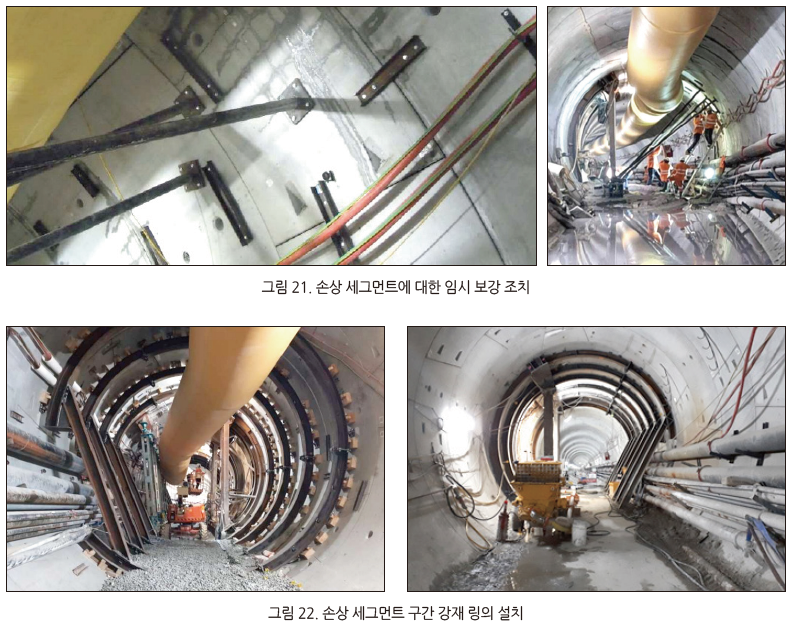
이후 시공사(SI-NRW)는 Dundas 피난연락갱의 양쪽에 일련의 완전한 강철 링을 설치하여 터널의 손상 부분을 정확한 선형과 수준으로 복원하는 최선의 방법에 대한 결정이 내려지는 동안 터널을 더욱 상당히 보강하였다. 피난연락갱의 입구에는 접근이 차단되지 않도록 부분 강재 링을 사용하였다.
4.2 갱내 보강 및 지상 보강
싱크홀의 보강과 도로 및 주변 지역에 대한 보강작업은 1번 터널의 손상에 대한 보강 설계에 따라 확정되었다. APA 고압 가스라인의 위치를 모니터링한 결과 최대 허용침하한도인 3mm 내에 있는 것으로 나타났으며, 피난연락갱 Dundas는 안정적인 것으로 평가될 수 있으며 압축 그라우팅 및 도로 보수를 포함한 복구 조치를 시작할 수 있었다.
최종적으로 싱크홀은 되메움토와 콘크리트로 채워졌고 11월 15일에 지표면으로부터 압축 그라우팅이 시작되었다. 압축 그라우팅은 싱크홀 주변이 보강될 것으로 예상되며, 압축그라우팅은 12월 중순에 완료되었고 Dundas 도로를 따라 있는 두 개의 좁은 임시차선이 12월 말에 운영되었으며. 향후 영구적인 도로 공사가 진행될 예정이다.
TBM 터널 주변 지반에 대한 갱내 보강은 규산나트륨을 사용한 침투 그라우팅 용액을 사용하여 시공되었으며, TAM(Tube-A-Manchette) 파이프를 사용하여 약 4개월에 걸쳐 처리를 수행했다. [그림 23]은 지상보강 그라우팅과 갱내 보강그라우팅을 수행하는 모습을 보여주고 있다.
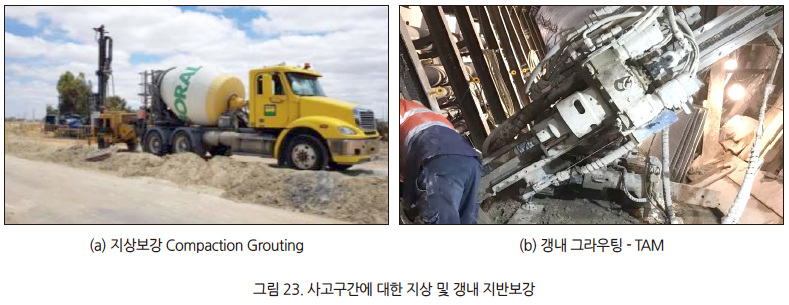
4.3 피난연락갱 재굴착
피난연락갱 Dundas는 지하수와 모래/실트의 유입으로 인하여 손상되지 않았으며, 강재 거더는 과도한 응력이나 변형의 징후를 보이지 않았다. 예방대책으로 두 번째 벤치 굴착이 완료되기 전에 피난연락갱에 근접한 세그먼트에서 두 터널의 인버트에 저압 그라우팅이 적용되었다.
1차 숏크리트 라이닝 및 인버트에 대한 방수막 설치가 완료된 상태에서 피난연락갱 공사가 계속되고 있다. 다음 단계는 콘크리트 인버트/바닥부 시공과 피난연락갱 측면 및 천단부에 방수재 설치, 콘크리트 라이닝 측벽 및 천단부 시공 등이다. 최종 단계는 피난연락갱과 본선 TBM 터널 사이의 경계면에 콘크리트 칼라를 시공하는 것으로 구성된다. [그림 24]에는 피난연락갱을 재굴착하는 모습이 나타나 있다.
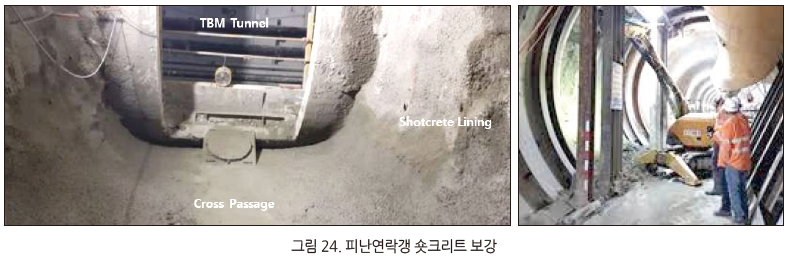
5. 사고 원인 분석
안전한 피난연락갱 굴착을 위해서는 그라우트된 지반, 주면 배면 그라우팅, 주변 지반 및 세그먼트 라이닝이 모두 전체적으로 안정적이고 불침투성이어야 한다. 이를 위해서는 다음이 필요하다.
1. 지반 그라우팅(제트 그라우팅)의 수밀성(Watertightness)
2. 배면 그라우팅의 수밀성
3. 지반 그라우트와 배면 그라우팅 사이의 수밀성
4. 지반 그라우트와 배면 그라우트의 충분한 역학적 강도(재료 특성 성능)
5. 지반 그라우트, 배면 그라우트 및 세그먼트 사이의 변형
따라서 본 TBM 붕락사고의 가능한 원인은 다음과 같은 측면 중 하나 이상과 관련이 있을 가능성이 높다.
a. 제트 그라우팅의 시공 결함
b. 배면 그라우트의 시공 결함
c. 배면 그라우트와 제트 그라우트 사이의 인터페이스의 파괴
d. 세그먼트 라이닝과 배면 그라우트 사이의 인터페이스의 파괴
약 12개월 전에 완료된 TBM 굴진중 제트 그라우팅과정에서의 지반 교란, 균열과 파손 및 피난연락갱 굴착에 따른 진동 효과도 원래의 국부적 약점을 증폭시켰을 수 있다.
다음 [그림 25]에는 가능한 경로와 그에 따른 유입, 특히 파이핑(piping)을 유발하는 경로를 보여준다. 그림에서 보는 바와 같이 제트 그라우트(a) 또는 배면 그라우트(b) 내의 시공 결함/파괴을 통한 누출(leakage), 배면 그라우트와 세그먼트 라이닝(c) 또는 제트 그라우트와 배면 그라우트(d) 사이의 경계면에서의 시공 결함/파괴를 통한 누수를 보여주고 있다.

본 사고의 잠재적인 시공 결함/파괴의 원인은 다음과 같이 될 수 있다.
1. 그라우트 지반의 역학적 강도 문제
2. 배면 그라우트의 역학적 강도 문제
3. 그라우트 지반의 투수성 문제
4. 배면 그라우트의 투수성 문제
5. 제트 그라우팅을 이용한 지반의 효과적인 완전 처리 불량
- 그라우트 컬럼사이의 갭 발생
6. 배면 그라우트 인터페이스의 효과적인 완전 그라우팅 불량
- 세그먼트 라이닝과 배면 그라우트 사이에 갭 발생
7. 세그먼트 라이닝과 제트 그라우팅 사이 인터페이스에 대한 효과적인 씰링 불량
- 인터페이스의 충분한 채움(closure) 불량
위에는 파이핑을 유발하고 지반침하/싱크홀을 발생시켜 터널내로 지하수가 쉽게 유입될 수 있는 7가지 가능한 문제점이 열거되어 있다. 현재까지 입수 가능한 정보로는 파이핑의 원인이 될 수 있는 시공 결함의 증거는 확인되지 않았다.
시공사(SI-NRW)와 엔지니어링 컨설턴트가 참여하는 사고조사위원회는 피난연락갱 Dundas 사고를 분석하기 위한 초기보고서를 작성했다. 보고서에서는 제트 그라우팅에 의한 지반보강처리가 Guildford 층의 매우 조밀한 모래층 하부 3m까지의 약 18.5m 깊이에 도달했음을 확인하였다. 그러나 이론적으로 제트 그라우트 컬럼이 서로 충분히 교차하고 있지만, 실제로는 특히 조밀한 Guildford 층을 통해 우선적인 침투 경로(seepage path)가 존재할 가능성이 있다는 점을 지적하였다. 또한 터널 라이닝의 배면 그라우팅에도 불구하고 그라우트된 지반을 통과하는 터널의 보링과 결과적으로 지반의 비압축(decompression)으로 인해 터널 라이닝과 그라우트 처리된 지반 사이의 접촉면을 따라 우선적인 유로(flow path)가 생겼을 수 있음을 강조했다.
피난연락갱의 인버트 굴착이 조밀한 Guildford 모래층의 상부에 도달함에 따라 Guildford 상층에서 침투 패턴(seepage pattern)이 발생했을 것으로 추측된다. 하지만 터널내부로 유입된 지하수로 인한 토사 운반이 왜 그렇게 빨리 지상에 도달했는지 불분명하며, 터널이 짧은 구간에 걸쳐 확실하게 침하되어 싱크홀이 발생한 것은 지반중에 싱크홀의 형성을 일으킬 수 있는 예상치 못한 지질 특징이 있었을 것으로 생각하였다.
요약하자면, 피난연락갱 Dundas에서 발생한 지하수/토사가 터널내로 유입되는 사고의 원인은 아직 명확히 규명되지 않았지만, 사고 중 지하수/토사의 유입으로 인해 터널 라이닝이 손상되고 터널상부에 싱크홀이 형성된 것으로 분석되었다.
6. 터널 복구 및 보강 대책
사고조사위원회는 향후 피난연락갱 시공을 위한 대책으로서 시공방법에 대한 검토를 완료했으며, 시공방법의 변경 사항은 다음과 같다.
피난연락갱 인접구간의 터널 링에 추가 볼트를 설치하고, 피난연락갱의 칼라부와 그라우트 지반과 터널 라이닝 사이의 인터페이스를 따라 터널 바깥구간에 추가 그라우팅을 적용하도록 하였다.
향후 지하수 침투(water ingress)가 발생할 경우를 대비하여 여러 가지 추가 대책으로서 숏크리트, 폼 및 시멘트 그라우트를 사용하도록 하고, 지하수 유입제어 전문기술을 보유한 전문업체도 포함된다. 다음 피난연락갱은 공항부지내 공터아래에 있으며, 굴착작업은 2019년 초에 시작되었다.
6.1 사고구간의 터널 복구 대책방안 검토
터널 사고로 인해 발생한 터널 주변의 지반 이완과 공동(void)을 보강하는 것은 Tunnel ONE의 장기적 안정성에 가장 중요하다. 손상된 터널 세그먼트가 보강될 때까지 터널 라이닝 주변에 공동이 여전히 존재하는지 여부와 이러한 공동이 터널 라인을 따라 얼마나 확장되었는지 정확히 확인하도록 해야 한다.
사고조사위원회는 이제 터널의 장기 내구성을 유지하면서 손상된 구간의 길이에 걸쳐 터널을 복구/재시공하는 방안에 대한 다양한 대책방안을 고려하였다. 발주처와 협의를 통하여 터널 보강작업의 최종 설계가 어느 정도 시간이 소요될 것으로 예상하고 우선적으로 다양한 대책방안을 검토하도록 하였다. 피난연락갱 Dundas 인접구간의 Tunnel ONE의 라이닝의 손상정도를 고려하고, 라이닝 변상조사 결과를 분석하여 가능한 장기 보강 대책방안에 대한 검토를 수행하였다. 이러한 보강 대책방안은 장기적인 구조 및 내구성 요구사항을 충족할 뿐만 아니라 설계, 시공 및 시간을 포함한 관련 리스크를 충분히 고려하였다. 검토된 보강 대책방안은 다음과 같다.
(a) Tunnel One의 손상 라이닝에 대한 보수 및 강화
(b) 제트 그라우팅 지반안정화 기법을 사용한 Tunnel One의 손상 구간 재시공
(c) 지반동결 안정화기법을 이용한 Tunnel One의 손상 구간 재시공
(d) D-wall 공법을 이용한 Tunnel One의 손상 구간 재시공
6.2 터널 복구 방안 검토
다양한 보강대책방안에 대한 장점과 단점에 대한 예비 분석을 정리하여 [표 1]에 나타내었다. 표에 제시된 내용은 가장 중요한 항목을 요약한 것이다.
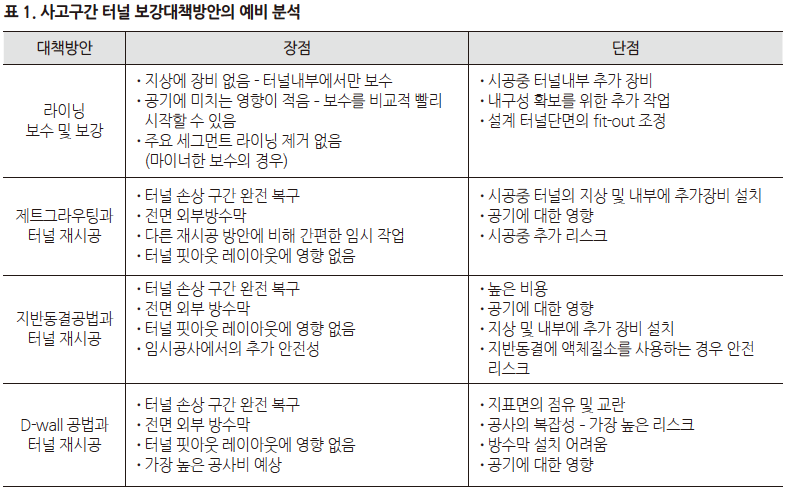
또한 다음을 포함하는 종합적인 분석을 통하여 보강대책 방안과 이에 따른 선형 검토, 단면 검토, 구조 및 방재 성능을 재검토하였으며, 종합적인 재시공 방안을 수립하였다.
1. 터널의 설계 및 시공에 관한 서류의 검토
2. 터널 사고 및 임시 조치의 검토
3. 사고 터널구간에 대한 지질 모델 및 3D 지반조사
4. 보강공사를 위한 손상된 터널구간 주변 지반 안정화 처리 설계
5. 제약 조건을 결정하기 위한 터널 노선 및 단면 요구사항 검토
6. 보강 대책방안에 대한 구조적, 내구성 및 방재성능 평가
7. 보강 대책방안에 대한 설계
8. 프로젝트 범위에 맞춰 제안된 보강 대책방안의 선형 분석
9. 시공 준비 및 모니터링
10. 리스크 식별과 리스크 완화를 설계의 안전성 검토(Safety in Design)
11. 운영 및 유지관리 요구 사항 검토
[그림 26]은 손상된 라이닝에 대한 보수/보강방법이 나타나 있으며, [그림 27]에는 제트그라우팅 공법을 적용한 터널 재시공방안, [그림 28]에는 지반동결공법을 적용한 터널 재시공방안, [그림 29]에는 D-Wall 공법을 적용한 터널 재시공방안이 나타나 있다.
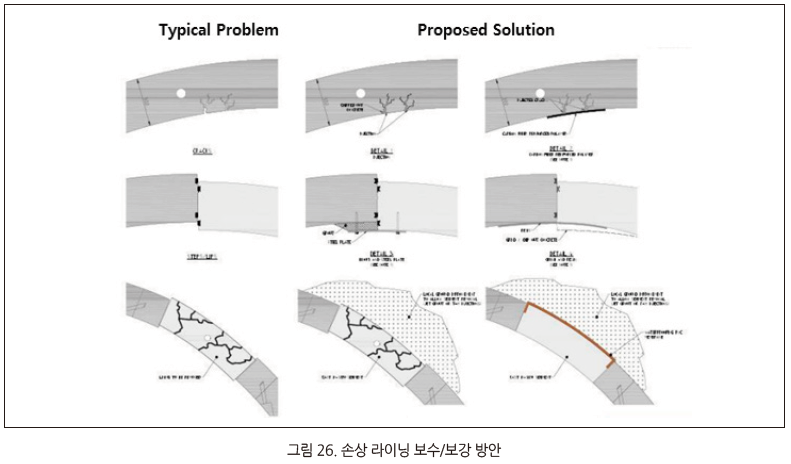

6.3 최종 복구방안 - 강재(SGI) 라이닝 적용
본 TBM 터널에서는 콘크리트 세그먼트 라이닝 프로세스가 채택되었다. 본 사고구간과 같이 터널의 다른 단면에 대한 대체 라이닝 타입이 적용될 수 있다. 사용되는 라이닝 타입은 완전히 새로운 터널인지 기존 터널에 대한 수정 또는 확장인지 여부를 포함한 여러 요인에 의해 결정된다. 이러한 대체 터널 라이닝 시공기법 중 하나는 강재(SGI) 라이닝 링을 사용하는 것을 포함한다. 강재 라이닝 세그먼트를 공장에서 생산한 현장에서 조립 시공한다는 점에서 생산 및 설치 기술은 콘크리트 터널 라이닝 프로세스와 유사하다. 터널 라이닝 링을 형성하기 위해 강재 세먼트는 볼트로 고정되며, 궁극적으로 콘크리트 터널 구조와 유사한 구조를 가진 자체 지지형(self-supporting) 터널 구조를 형성한다(그림 30).
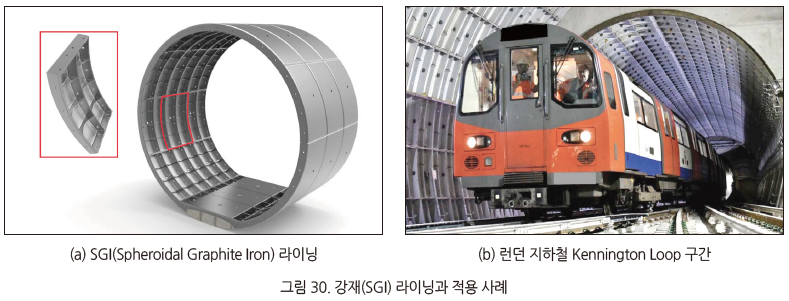
터널의 손상된 구간에 대한 권장 보강 제안은 손상된 콘크리트 라이닝 내부에 강재(SGI) 세그먼트 터널 라이닝을 설치하는 것이다. 강재 라이닝은 자체 지지하며 기존 콘크리트 터널 라이닝 내에서 지지대 역할을 한다. 이는 근본적으로 손상된 터널 구간 주변의 지반이 안정화 될 수 있으며, 기존 콘크리트 세그먼트는 제자리에 유지되지만 현재 손상 및 변상에 유의하여 강재(SGI) 터널 라이닝 구조의 설치에 필요한 공간과 적절한 면을 만들기 위해 절삭 연마하도록 한다.
강재(SGI) 터널 라이닝을 적용하기 위해 기존 콘크리트 터널 라이닝을 절삭했음에도 불구하고 손상된 터널 구간에 약간의 공간 제약이 가져오게 된다. 터널 내공감소는 레벨(열차 바닥/문 높이)에서 선로와 평행하게 달리는 비상 출구/유지보수 통로의 폭(공칭 850mm, 국부적으로 836mm)을 14mm 줄이는 것 외에는 운영상 큰 제약을 가하지 않는다.
마찬가지로 재료의 변화(콘크리트 대신 SGI)와 기존 터널내에서 인력으로 강재(SGI) 라이닝을 설치해야 하는 필요성으로 인해 원래 터널 요구조건에서 벗어난 방수 및 내화성 요구 사항에 다른 제약 조건이 필요하게 된다. 강재(SGI) 세그먼트 체결 또는 결합에는 콘크리트 세그먼트 터널과 다른 대체 조인트 시스템 및 개스킷 유형이 필요하지만, 이는 내구성에 영향을 미치지 않으며 방수에도 영향을 미칠 가능성이 낮다.
강재(SGI) 라이닝은 콘크리트 라이닝보다 화재 사건 동안 손상되거나 구조적으로 파괴될 가능성이 더 높기 때문에 리스크가 허용가능한 허용범위 내에 있는지 여부를 판단하기 위해 제안된 강재(SGI) 보강대책에 대한 화재 안전 정성적 리스크 평가(QRA)가 수행되었으며, 본 평가 강재(SGI) 라이닝에 스프레이를 적용하는 경우에도 강재(SGI) 라이닝에 미치는 영향을 고려했다. 이를 통하여 본 사고구간에 적용되는 강재(SGI) 라이닝이 터널 화재 사건의 가능성 또는 결과의 변화가 매우 적음을 검증하였다. 이는 사고 구간이외 구간에 비해 강재(SGI) 라이닝 보강 구간이 상대적으로 짧은 26m 구간을 고려할 때 예측가능한 것으로 평가되었다.
또한 강재(SGI) 라이닝 구간에 방재용 스프레이를 적용하는 경우 비용편익부분에 있어 적절한 개선이 달성되지 않았다. 또한 보호 코팅에 스프레이를 뿌리면 터널내 공간적 제약(터널 내공두께 35mm)이 가중되어 강재(SGI) 라이닝의 설치가 복잡해진다. 정기적인 육안 검사를 제약하는 고정 장치 및 장비의 유지보수 및 터널 내부 부착과 관련된 기타 문제가 발생할 수 있다.
이러한 이유로 발주처는 강재(SGI) 터널 라이닝이 설치된 후 적용할 수 있는 방화 옵션을 추가로 조사할 것을 요청했으며, 시공사는 다른 제약 조건을 부과하지 않고 강재(SGI) 라이닝의 구조적 안전성을 증가시킬 수 있는 대책방안에 대해 검토하였다. 터널내 코팅의 전주기(full cycle) 비용과 적용 및 재시공 리스크를 고려하는 것이 적절하여야 하며며, 이러한 리스크는 손상된 터널의 상대적으로 작은 구간을 고려할 때 유익하지만 필수적이지 않다는 점에서 대책방안이 허용 가능한지 여부에 대한 고려를 충분히 수행하여야 한다. [그림 31]에는 손상된 라이닝 구간에 적용된 강재(SGI) 라이닝과 스프레이가 시공된 라이닝 모습이 나타나 있다.
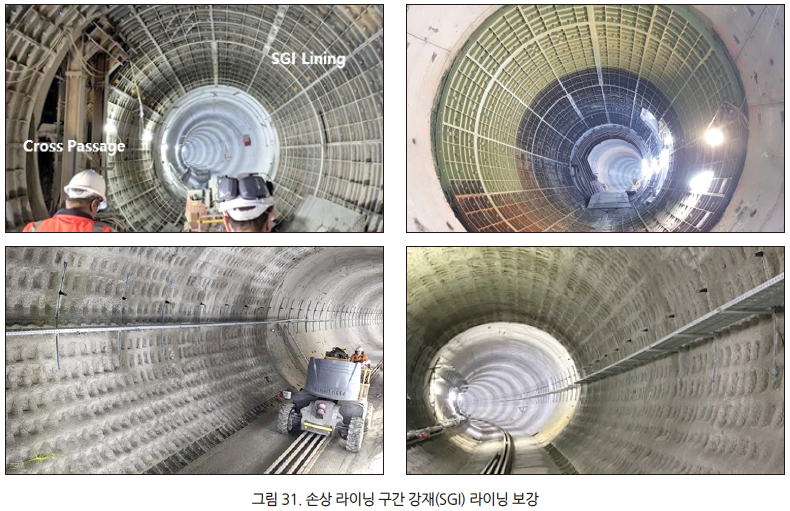
지금까지의 피난연락갱 Dundas 사고에 대한 사고조사위원회의 상세조사내용을 바탕으로 [그림 32]에 나타난 바와 공식적인 사고원인 및 복구공사보고서가 발간되었다.
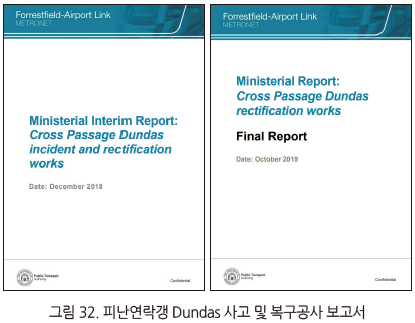
6.4 안전 대책강화 및 개통 그리고 소송
주정부는 공사 현장에서 안전의 중요성을 반복적으로 강조했으며, 새로 도입된 안전 대책에는 안전 준수 책임자를 2명에서 5명으로 늘리는 내용이 포함되어 있으며, 시공사는 터널 운영 감독관을 임명하여 더 큰 감독을 제공하고 안전에 중점을 두고 있다.
또한 발주처는 2018년 한 해 동안 안전 점검 658건, 안전준수검사 430건, 대상 공정검사 72건을 실시했으며, 안전직원들로 구성된 안전팀은 주간 및 야간 근무 모두에 대해 현장 안전을 모니터링하였다.
2018년 9월에 터널 사고이후 싱크홀 구간과 손상된 Tunnel ONE 터널 부분에 대한 보강공사가 2021년 3월에, 터널링은 2021년 4월에 완료되었다. 2022년 상반기에 첫 열차가 운행될 것으로 예상되었지만 코로나의 대유행의 영향으로 상당기간 지연되어 당초 개통예정인 2020년 12월보다 약 2년이 연기되어 마침내 2022년 10월 9일에 개통되었다. [그림 33]에는 Airport Line 개통당시의 모습을 보여주고 있다.
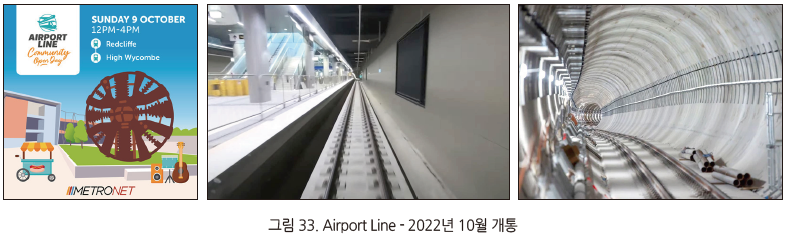
2023년 현재 개통 지연문제와 추가 공사비 문제로 법적 전쟁(legal battle)을 시작했다. 본 프로젝트는 당초 2020년 말에 완공될 예정이었지만, 터널 사고 등으로 인하여 2022년 10월까지 개통이 지연됨에 따라 이에 대한 책임이 누구인지를 법정소송을 통하여 가리고자 한 것이다. 현재 대법원에서는 두 개의 터널과 세 개의 역을 연결하는 12개 터널의 설계와 시공의 결함으로 인한 지연에 초점을 맞추고 있다고 한다. 이 소송은 발주처, 시공자 및 설계자의 책임(지반 리스크 포함)에 대한 복잡하고도 어려운 문제로 상당한 시간이 소요될 것으로 보인다.
참고문헌
1. Ministerial Interim Report: Cross Passage Dundas incident and rectification works, Forrestfield-Airport Link METRONRT, December 2018
2. Ministerial Report: Cross Passage Dundas rectification works Final Report, Forrestfield-Airport Link METRONRT, October 2019
3. Cross passage and emergency egress shafts, Fact Sheet, Forrestfield-Airport Link METRONRT, March 2019
4. Cross passage Dundas Accident Updat, Fact Sheet, Forrestfield-Airport Link METRONRT, December 2018
5. Jet Grouting and Artificial Ground Freezing, Forrestfield-Airport Link Project, Trevi Australia, 2018
6. Forrestfield-Airport Link (Within The Perth Airport Estate) Final Major Development Plan, Forrestfield-Airport Link, November 2015
7. https://www.forrestfieldairportlink.wa.gov.au/
8. https://www.perthnow.com.au/business/construction/
9. https://www.abc.net.au/news/2018-12-18/
10. https://www.geplus.co.uk/news/forrestfield-cross-tunnel-sinkhole-report/
11. https://www.perthnow.com.au/business/construction/sinkhole-brings-forrestfield-airport-link-project-to-standstill-ng
제8강 - 요점정리
제8강에서는 Forrestfield-Airport Link 공항철도 TBM 터널공사에서의 발생한 터널 침수 및 도로함몰 사고사례를 중심으로 사고의 발생 원인과 교훈에 대하여 고찰하였다. 본 사고는 도심지 구간에서의 TBM 터널의 피난연락갱 공사중 발생한 붕괴사고로서, 본 사고 이후 TBM 터널공사에서의 피난연락갱 사고를 방지하기 위한 설계 및 시공상의 다양한 개선노력이 진행되어 피난연락갱 시공기술이 발전하는 계기가 되었다. 본 TBM 터널 사고를 통하여 얻은 주요 요점을 정리하면 다음과 같다.
■ TBM 터널에서의 지반그라우팅 리스크
본 TBM 터널구간의 피난연락갱 시공시 지반개량효과를 증진하기 위하여 TBM 굴진전에 제트 그라우팅(jet grouting)을 적용하였으며, TBM 굴진 완료후 피난연락갱 굴착전에 피난연락갱 주변에 인공지반동결공법(artificial ground freezing)을 적용하였다. 사고가 발생한 구간은 하부에 모래층의 대수층이 분포하고 있어 피난연락갱 굴착시 피난연락갱 주변 지반 그라우트체의 결함과 갭을 통하여 지하수가 터널 내부로 급격하게 침투된 것으로 분석되었다. 따라서 토사지반구간에서의 지반그라우팅 및 배면 그라우팅공법 적용시 그라우트의 품질관리가 무엇보다 중요하므로 지반상태를 면밀히 관찰하고 이에 대하여 보다 적극적으로 대응하여야만 한다.
■ TBM 터널에서의 피난연락갱 시공 리스크
본 사고는 TBM 공법으로 시공된 상하행의 본선터널을 연결하는 피난연락갱 구간에서 발생하였다. 특히 토사지반구간에 NATM 공법으로 시공되는 피난연락갱은 시공리스크가 상대적으로 큰 취약한 구간이라 할 수 있다. 본 현장에서는 피난연락갱 주변 지반을 개량하고 차수성능을 확보하기 위하여 지반 보강그라우팅과 인공동결공법이 적용되었지만, 라이닝과 지반 그라우트체의 갭, 지반 그라우트체의 결함, 배면 그라우트의 결함 등으로 복합적인 문제가 생기면서 침수 사고로 이어진 것으로 판단된다. 따라서 피난연락갱 시공시 주변 지반에 대한 차수성능을 확인하고 누수 등의 문제발생시 보다 즉각적이고 능동적인 비상 대응체계가 요구됨을 알 수 있다.
■ 사고원인조사와 복구 방안 수립
본 사고가 발생한 직후 발주처에서는 사고조사위원회를 구성하여 설계 및 시공에 대한 철저한 조사를 통하여 사고 원인을 규명하고 복구방안을 제시하였다. 사고 원인은 피난연락갱 주변 지반의 갭(gap)과 내부 결함(defect)으로 인한 하부 모래층에서의 파이핑(piping)으로 물과 토사가 터널내로 급격히 유입되고 주변 지반이 유실됨에 따라 지상도로 함몰에 이르게 된 것으로 파악되었다. 복구 방안으로는 터널을 재시공하지 않고 손상된 라이닝을 보강하는 방안을 채택하였다. 보강공법으로는 내공한계를 심각하게 침해하지 않는 범위에서 손상된 라이닝을 절삭하여 강재(SGI) 라이닝을 설치하도록 하였으며, 터널화재 등에 대비한 방재성능을 확보하기 위하여 강재(SGI) 라이닝 표면에 스프레이를 타설하였다. 약 1년간의 복구공사를 성공적으로 마치고 당초 개통 예정인 2020년 말보다 약 2년이 연기되어 마침내 2022년 10월 9일에 개통되었다.
■ TBM 터널 사고와 교훈
본 사고는 토사지반의 TBM 터널에서 배면 그라우팅 품질관리, 피난연락갱 구간의 지반그라우팅 품질관리, 피난연락갱 주변 지반에 대한 지반동결공법의 시공관리 그리고 NATM으로 굴착되는 피난연락갱의 시공관리 상의 문제점 등을 확인할 수 있었고, 특히 TBM 터널공사에서의 설계변경 절차 및 시공관리방법 등의 건설공사의 관리상의 제반 문제점을 확인할 수 있는 계기가 되었다. 특히 발주처 및 사고조사위원회 등을 중심으로 철저한 조사와 검토를 진행하여 본 TBM 터널사고에서의 사고원인 규명과 복구방안 대책 등을 수립하여 호주에서 TBM 터널공사 안전관리 및 시공관리시스템을 개선시키게 되었다.
이제 제8강이 마무리되었다. 보다 자세한 내용은 참고문헌을 읽어주기 바란다. 호주 Forrestfiled-Airport Link 공항철도 TBM 터널 사고는 호주 토목공사의 안전문제에 대한 관리시스템을 전환하는 중요한 사고였다. 호주는 2000년대 이후 시드니, 멜보른, 퍼스 등과 같은 도심지에서의 지하인프라 건설의 급격한 증가로 인하여 공기 준수이라는 목적을 달성하기 위하여 체계적인 시공관리가 제대로 운영되지 못한 상태였다. Perth 도심지에서의 터널 침수와 도로 싱크홀 사고는 토목기술자뿐만 아니라 일반 국민들 그리고 시당국에게도 상당한 부담을 준 사고로 메스컴을 통하여 생중계되고, 부실시공에 대한 여론이 급증하는 계기가 되었다. 또한 사고구간에 대한 보강공사와 복구공사로 공항철도 개통이 상당히 지연되어 경제적 손실을 끼쳤던 TBM 터널공사에서의 사고사례라 할 수 있다.
또한 본 TBM 터널사고는 상당한 리스크가 있는 피난연락갱에서 발생한 사고로 토사지반구간에서 NATM 공법으로 굴착하게 되는 피난연락갱의 지질 리스크, 품질관리 및 시공관리의 중요성을 인식하게 되는 중요한 계기가 되었다고 할 수 있다. 따라서 토사지반구간에 시공되는 지반 그라우팅공법과 피난연락갱에서의 지반동결공법의 시공관리 및 주변 지반의 차수 및 보강효과를 검증하는 품질관리가 무엇보다 중요하므로 세심한 주의와 관리가 무엇보다 요구된다 할 수 있다. 또한 이러한 지질 및 시공리스크를 최소화하거나 극복할 수 있는 기술이 더욱 신중하게 검토되고 적용되어야 할 것이다.
다음 제9강에서는 독일 Rastatt TBM 터널공사에서 발생한 붕락사고로부터 사고 원인과 메커니즘 분석, 임시대책 및 보강·복구 방안 그리고 사고로부터 배울 수 있었던 교훈에 대하여 설명하고자 한다. 이것은 TBM 터널공사중에 발생한 실제 붕락사례를 기초로 한 것으로 TBM 터널에서의 사고 문제에 관심이 많은 지반 및 터널 기술자들에게 실제적으로 도움이 될 것이다.