지능형 다짐(Intelligent Compaction)을 이용한
연속다짐관리(Continuous Compaction Control)
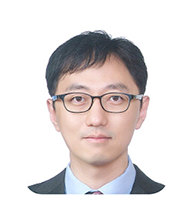
김 규 선
삼성물산㈜ 건설부문(kyusun@empas.com)
1. 개요
최근 건설현장에서 스마트 기술을 활용한 자동화 시공에 대한 관심이 많아짐에 따라 건설기술에 다양한 IT 기술이 접목되고 있다. 이러한 시대적 요구에 발맞춰 2023년 1월에는 ‘KCS 10 70 10 머신가이던스 및 머신컨트롤 시공 일반’이 국가기준으로 제정되기도 하였다. 지반공학 분야에서도 스마트 기술 관련한 여러 시도들이 있는데, 토공사에서 진동롤러 다짐 후 품질시험을 반복적으로 수행하는 일반 다짐공정을 연속적인 자동화 작업으로 대체할 수 있는 지능형 다짐(Intelligent Compaction, 이하 IC) 기술에 대해 다수의 연구 및 현장 적용이 진행되고 있다. 본 고에서는 스마트 건설기술로서 국내·외적으로 관심도가 높아진 IC 기술을 이용한 다짐관리 방법에 대해 소개하고자 한다. 유럽에서는 지능형 다짐을 연속다짐관리(Continuous Compaction Control, 이하 CCC)라고 정의하여 문헌에서는 IC와 CCC 두 가지 용어가 혼용되고 있는데, 여기서는 지능형 다짐을 IC로 통일하여 표현하였다.
IC 기술은 유럽에서 40여년 전에 개발된 이래로 유럽과 미국을 중심으로 연구과제, 실증시험 및 표준화 작업이 진행되고 있다. 꽤 오래된(?) 기술이지만, 최근의 IT 기술발달 및 미국 연방도로국(FHWA)의 2004년 IC 로드맵 발표 이후 IC 기술개발 및 현장 적용이 가속화되었다. 초기에는 다짐롤러를 생산하는 장비제조사(Original Equipment Manufacturer, 이하 OEM) 주도로 기술이 개발되어 장비에 따라 다짐도를 평가하는 측정치가 각각 달랐는데, 최근에는 CMV(Compaction Meter Value)를 측정치로 이용하는 상용화된 IC 장착키트(Retrofit kit)가 개발되어 OEM과 상관없이 해당 모듈을 운영장비에 장착 후 IC 롤러로 활용하여 기술보급이 확대되고 있기도 하다. 국내에서는 한국건설기술연구원(KICT)을 중심으로 관련 연구가 진행되고 있는데, ‘텔레매틱스를 활용한 지능형 성토다짐관리시스템 개발(2009)’, ‘지능형 가상 지반데이터 및 다짐 관리 기술을 적용한 스마트 토공 플랫폼 개발(2020)’이 연구과제로 진행되었고, 2020년에 착수된 도로공사 주관의 ‘스마트 건설기술 개발 국가 R&D사업’의 세부과제로 IC 관련 연구가 현재 진행중이다. 2021년에는 ‘KCS 10 70 20 지능형 다짐공’이 국가기준으로 제정되면서, 국내에서도 본격적으로 IC 기술을 실무에 적용할 준비가 되고 있다. 하지만, IC 기술은 아직까지는 체계를 잡아가고 있는 단계이고, 많은 현장에 전파되지 않았기 때문에, 국내 실무자에게는 다소 생소할 수도 있는 내용이기도 하다.
IC 기술은 필자의 주요 연구분야와의 연관성으로 인해 오랜 기간 관심있게 지켜보던 기술이었는데, 국내에서도 관련 연구가 순차적으로 진행되면서 다수의 연구결과가 발표되니 무척 반가운 일이다. 국내 연구자들에 의해서도 논문집에 몇 차례 소개된 바 있지만, 본 고에서는 IC 롤러를 이용하여 연속다짐관리를 수행하기 위한 개요와 절차 중심으로 IC 기술에 대해 간단히 정리하였다.
2. 지능형 다짐(Intelligent Compaction)
지능형 다짐은 기초지반에 대한 다짐작업의 정확도와 효율성을 향상시키는 기술이며, 연속다짐관리를 제공하는 진동롤러 일체형 시스템을 IC 시스템으로 정의한다(Mooney & Adam 2007, White et al. 2009). 기초지반의 요구성능(다짐도) 확보를 위해서 토공사 시 다짐품질 확인 및 균일성 유지는 매우 중요하다. 기존의 진동롤러에 의한 다짐관리 시 발생하는 부분적인 미다짐 또는 과다짐은 부등침하 또는 기초지반의 성능저하를 유발할 수 있다. 이는 다짐작업 중 롤러 운전자가 실시간으로 지반의 다짐도에 대한 파악이 어려워서 균질한 다짐이 쉽지 않기 때문이다. 이를 개선하기 위해, 신속한 다짐평가가 가능한 비파괴 및 관입시험법(Soil Stiffness Gauge, Dynamic Cone Penetrometer, Light Weight Deflectometer, Nuclear Density Gauge 등)을 이용하여 빠르게 지반의 물리·역학적 특성을 평가하기도 하는데, 비파괴적인 급속시험이라 하더라도 일점시험법은 시험수량의 한계(전체면적의 약 1%)가 있기 때문에, 부지 전체에 대한 다짐상태를 대표하는 충분한 수량의 품질시험 결과를 제공하기는 어렵다(Mooney et al. 2010). 이러한 일점시험의 Coverage 관련한 단점은 다짐 중 연속적으로 지반강성에 대한 정보를 제공하는 IC 기술을 이용하여 해결할 수 있을 것으로 판단된다(그림 1 참조).
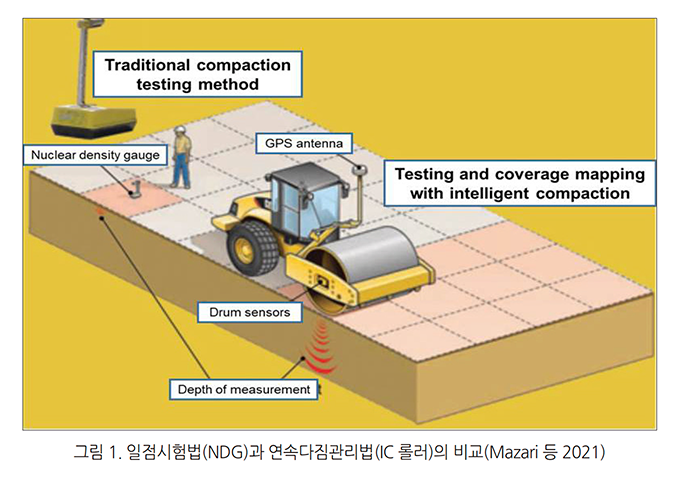
IC 롤러는 다짐작업 중 측정된 지반강성에 대응하여 다짐을 위한 롤러의 파라미터를 자동으로 제어할 수 있는 측정·제어 시스템이 탑재된 진동롤러로 정의된다. 롤러의 진동드럼으로 원심력이 지반에 가해지게 되는데, 이는 주파수와 진폭으로 표현되고, 이후 롤러는 지반반력을 측정하고 이를 지반강성 값으로 표시할 수 있다. IC 롤러는 일반적으로 드럼에 장착된 ① 가속도계, ② GNSS(Global Navigation Satellite System, 미국에서는 GPS), ③ 컴퓨터시스템, ④ 디스플레이, ⑤ 자동 제어시스템의 5가지 요소로 구성된다(그림 2 참조). 가속도계는 진동드럼 근처의 롤러 프레임에 장착되어 가속도, 드럼의 움직임 또는 진동과 함께 다짐롤러의 진폭 및 주파수를 연속적으로 측정하고, 측정값은 다짐도를 평가하기 위해 지반강성 또는 탄성계수를 상관관계를 이용하여 나타낸다. GNSS는 다짐 중 측정위치에 대한 연속적인 측정에 활용되는데, 위치 데이터는 수십 mm의 정확도로 GNSS에 의해 수집된다. 수집된 정보는 장착된 컴퓨터시스템에 전송되고 측정값은 OEM에서 개발한 알고리즘에 의해 특성치 분석이 수행된다. 컴퓨터시스템은 IC 측정치와 GNSS 데이터를 병합하고, 디스플레이는 롤러 운전자에게 다짐상태뿐만 아니라 지반강성, 통과횟수, 주파수, 속도 및 진폭을 실시간으로 색상구분하여 다짐작업을 효율적으로 진행할 수 있도록 한다.
IC 롤러 운전자가 반자동으로 취득한 정보를 이용하여 다짐을 위한 제어작업을 하는 경우를 ‘낮은 단계의 IC’라고 한다면, 드럼에서의 강성 반력에 응답하여 진폭과 주파수를 운전자의 개입없이 자동으로 조정하는 것을 ‘높은 단계의 IC’로 정의할 수 있다. IC 롤러를 활용하면 시간과 비용을 절감할 수 있을 뿐만 아니라 높은 다짐품질 확보를 기대할 수 있는데, 이를 기반으로 다짐공정을 자동화하면 경제적인 비용으로 토공작업의 정확도를 극대화 할 수 있다. 또한 연속적인 데이터 취득이 가능하므로 토공품질의 균질성을 보장하고 지반구조물의 장기성능 향상을 통해 토공사 품질관리에 있어서 중요한 역할을 할 수 있으며, 향후 프로젝트를 위한 설계 기초 데이터로 활용할 수 있는 잠재성도 있다.
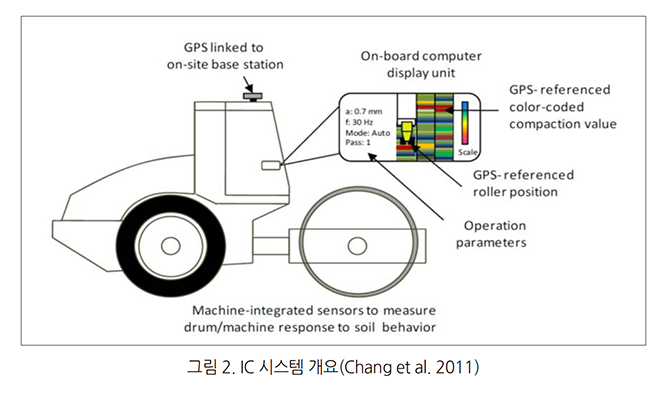
일반적으로 보수적인 기준을 적용하는 토공사 분야에서 신기술을 적용하고자 할 때는, 해당 기술에 대해 신뢰할 만한 공공기관의 설계기준 및 시방서 제공이 중요한데, IC 기술의 경우에는 유럽과 미국 등의 몇몇 국가 주도로 기준에 대한 체계를 잡아가고 있다. IC 기준은 1990년 오스트리아에서 처음 도입되었으며, 이후 독일, 스웨덴, 스위스에 차례로 도입되었다. 오스트리아 기준을 기반으로 국제지반공학회(ISSMGE)는 2005년에 관련 지침을 발표하기도 하였다. 현재는 유럽 기술표준인 CEN/TS 17006 ‘Earthworks-Continuous Compaction Control (CCC)’으로 2016년에 통합되었다. 미국은 FHWA가 2014년에 토사용 IC에 대한 기준(Generic-IC Specifications for Soils)인 Intelligent Compaction Technology for Soil Applications을 발표하였고, 각 주(State)의 교통부(Department of Transportation, 이하 DOT)에서 지역 규정을 반영하여 순차적으로 IC 기준을 승인하고 있다. 그림 3은 2020년 기준으로 토사용 IC를 인증하고 있는 미국내 주별 현황을 나타내고 있다. 토사용 IC는 아스팔트용 IC에 비해 전파속도가 다소 늦지만 꾸준히 적용 사례가 증가하고 있는 추세이다.
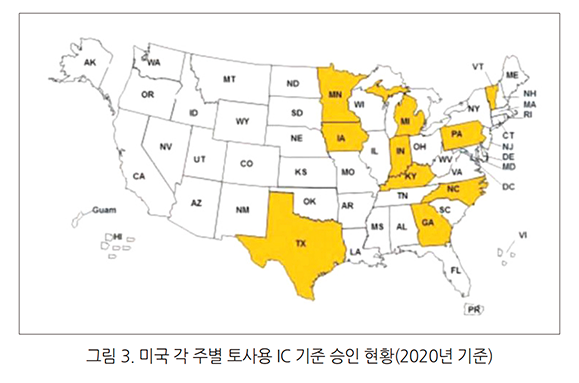
3. IC 개발역사 및 장비별 특징
지능형 다짐의 개념은 1970년대 유럽에서 시작되었으며, 최초의 롤러기반 연속다짐관리 시스템이 특허를 받은 지도 40여년이 지났다(Forssblad 1980, Thurner & Sandstrom 1980). 초기에는 다짐층의 강성을 진동주파수와 연관시키는 개념으로 시작되어 CMV가 제안되었다. 롤러기반의 가속도 측정에 대한 첫 연구는 1974년 스웨덴 고속도로 관리국이 가속도계가 장착된 Dynapac社의 진동롤러를 이용하여 수행했을 때이다. 1975년에는 스웨덴 Geodynamik社가 설립되었고, 다짐도를 평가하기 위한 CMV는 1978년에 개발 및 도입되었다. 스웨덴 Dynapac社는 1980년에 상업적으로 CMV 기반의 다짐측정기를 제공하기 시작했으며, 이후 스위스 Ammann社와 미국 Caterpillar社 등의 OEM에서도 CMV 기반의 IC 롤러를 제공하기 시작했다. 독일 Bomag社는 1990년대 후반에 동적 지반강성을 측정하기 위한 Evib를 개발했다. 1999년 Ammann社는 흙의 다짐도 측정을 위해 집중 매개변수 2자유도 스프링-질량-대시포트 시스템을 고려한 ks을 도입했다.
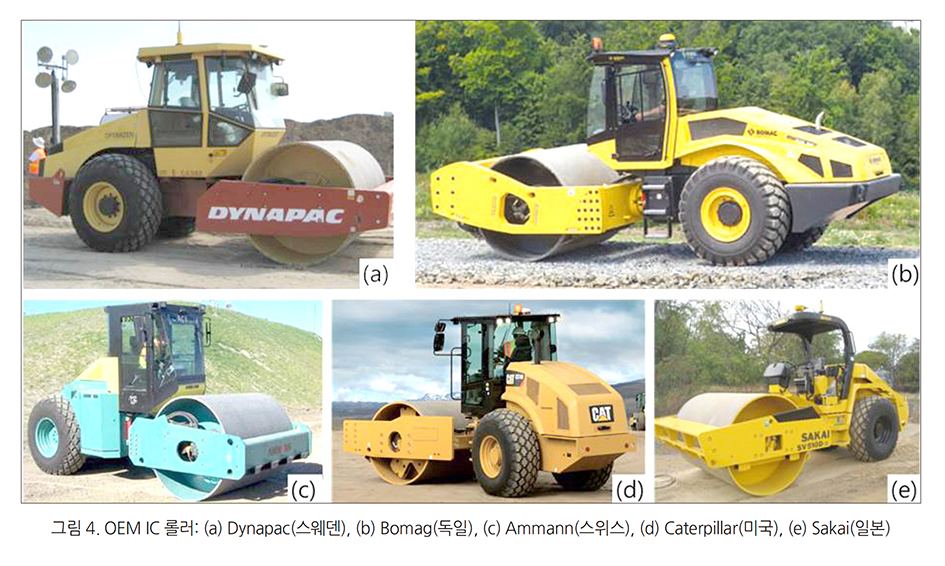
이 두 가지 매개변수(Evib 및 ks)는 기존의 가속도 기반 특성치인 CMV와는 달리 지반성능과 관련된 특성치로 생각할 수 있다. 2003년 Caterpillar社는 회전저항을 기반으로 하는 MDP(Machine Drive Power)를 도입했고, 2004년 일본 Sakai社는 다짐상태를 평가를 위해 진동의 고조파(Harmonics) 성분을 사용하여 CMV 기반의 CCV(Compaction Control Value)를 개발하여 IC 롤러에 적용하였다(Mooney et al. 2010). CCV는 CMV와 유사한 개념인데, 채택된 주파수 성분이 더 많으므로, CMV의 확장판으로 생각할 수 있다. 최근에는 IC 롤러의 여러 파라메터에 대한 공통적인 표현으로 ICMV(Intelligent Compaction Measurement Value, 이하 ICMV)를 IC 측정치로 표현하고 있다. 각각의 OEM이 제공하는 IC 롤러는 그림 4에 일부를 나타내었고, ICMV에 대한 특성을 정리하면 표 1과 같다.
전용장비를 사용해야하는 OEM IC 롤러에 대신에 장착모듈을 활용한 경제적인 IC 시스템을 운용할 수도 있다. 2008년 Trimble社는 일반 진동롤러에 장착할 수 있는 IC 장착키트를 출시했다. 이후 IC 장착키트의 고도화 및 개선으로 최근 적용 사례가 증가하고 있다.
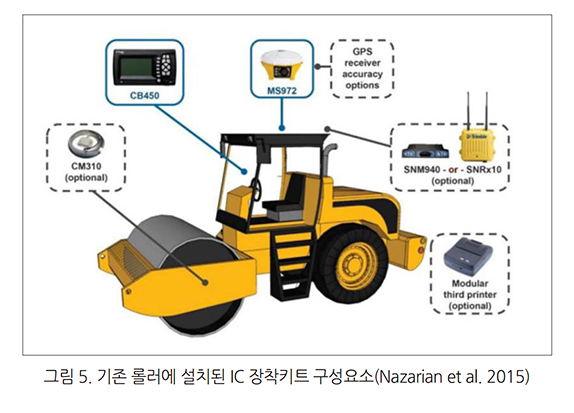
이 키트에는 GNSS 안테나와 수신기, 진동 센서(가속도계), 연결 케이블, 모니터링 디스플레이가 포함된다(Nazarian et al. 2015). 그림 5는 일반 진동롤러에 설치하는 IC 장착키트의 구성요소를 나타낸다. IC 장착키트는 매핑(통과횟수 및 ICMV), 실시간 정보(롤러속도, 위치, 진폭 및 주파수), 실시간 보고서(다짐성능, ICMV 데이터 및 위치 데이터)를 제공하므로 OEM IC 롤러와 동일한 성능을 발휘할 수 있다. 현재의 Trimble IC 장착키트는 가속도 측정 기반의 장치이므로 인증된 기술자에 의한 가속도계 설치가 중요하며, 드럼의 실제 진동을 포착할 수 있는 위치에 센서를 장착한 후 검교정이 필수적이다.
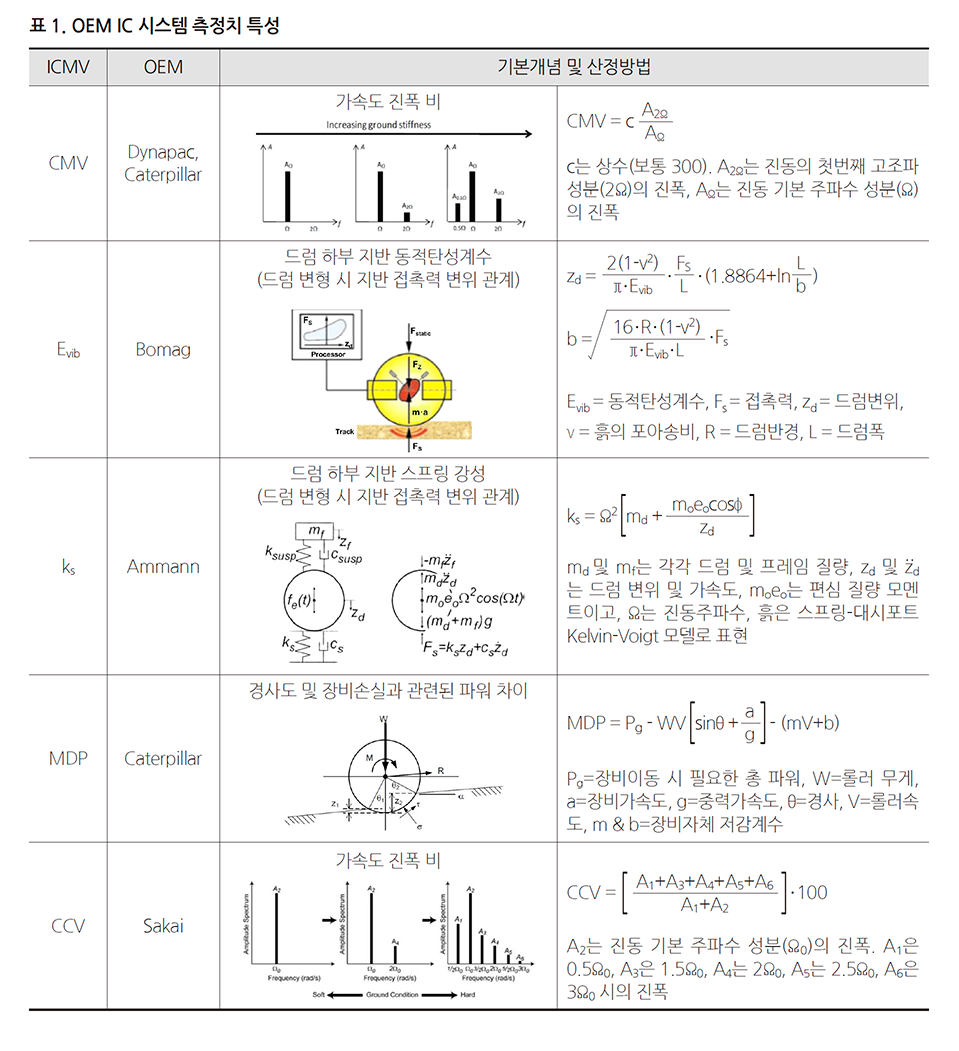
4. 지능형 다짐을 이용한 연속다짐관리 기준
앞 절에서 설명하였듯이, IC 관련 기준은 현재 미국 FHWA 기준을 기반으로 하는 각 주의 DOT 기준과 유럽 기준인 CEN/TS 17006 등이 있다. 미국 기준이 IC 시공을 위한 프로세스 중심으로 설명되어 있는데 반해, 유럽 기준에는 IC를 적용하기 위한 기술적인 설명이 추가되어 있어서 해당 기술을 이해하는데 도움이 된다. 국내의 경우에는 공통공사 표준시방서로 KCS 10 70 20 “지능형 다짐공”이 2021년에 제정되었다.
4.1 미국 기준(2014)
미국 FHWA에서는 IC 기준을 2014년에 제정하였고, 이후 각 주별 DOT에서 각자의 실정에 맞게 수정하여 적용하고 있다. 이 기준에서는 IC 시공 시 다짐에 필요한 GNSS 사양, 다짐횟수, 다짐속도, 다짐도 등의 측정항목 및 방법을 정의하고 있다. GNSS 및 수신기가 각 IC 롤러에 설치되어야 하고, 롤러의 위치를 모니터링하고 다짐횟수를 추적하며, 가속도계 기반의 측정시스템으로 다짐도를 측정한다. 미국 기준에서는 표준화된 IC 전용 데이터 관리 소프트웨어(VETA, 舊VEDA)를 사용하도록 권고하고 있다. 이 소프트웨어를 이용하여 IC를 통해 생성된 공간(geospatial) 데이터에 대한 저장, 시각화, 분석작업 및 일점시험법에 의한 데이터 관리가 가능하다. 그리고, 아스팔트 IC의 경우에는 온도 프로파일링을 추가로 처리할 수 있다.
IC 롤러의 최적 통과횟수를 결정하기 위해서는 시험시공(길이 75m, 폭 8m 이상)이 실시되어야 하며, 구간 전체에서 동일한 설정(속도, 주파수)을 사용해야 한다. 구간 내 균일하게 이격된 10개 이상의 위치에 대해, 롤러 통과 후 밀도 또는 강성을 측정한다. 목표 ICMV는 그림 6에 나타낸 바와 같이, 통과횟수별 ICMV 곡선에서 ICMV 증가가 5% 미만으로 발생한 통과횟수에 해당하는 ICMV를 참고하여, 다짐기준(밀도 또는 강성)에 대응하는 목표 ICMV 및 롤러 통과횟수를 시공기준으로 설정할 수 있다. 그리고, FHWA 기준에는 포함되지 않았지만 일부 DOT 기준에서는 장비의 요구조건이 제시되어 있다. 롤러의 위치는 ±40~50mm의 정밀도, 속도는 0.5km/hr(전진 시), 주파수는 2.0Hz, 진폭은 0.2mm 범위의 허용오차를 요구하기도 한다.
본시공에서는 시공면적의 최소 90% 범위가 시험시공에서 결정된 목표 ICMV의 70% 이상이 되어야 한다. IC 기준을 만족하지 못하는 구간은 재작업 및 재평가를 하도록 규정하고 있다. FHWA 기준에서는 IC 작업에 대해 4~8시간의 현장교육을 실시하도록 규정하고 있는데, 일부 DOT에서는 2일 교육(1일차 이론교육, 2일차 현장교육)을 요구하는 등 IC 기술에 대한 현장 작업자 대상의 교육을 강조하고 있기도 하다.
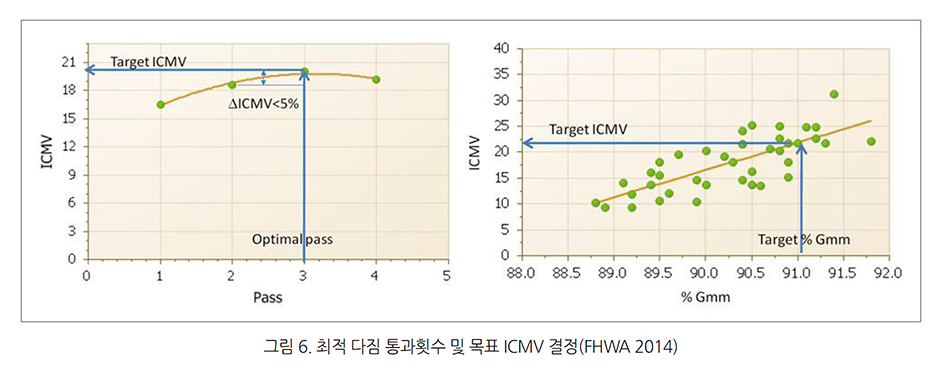
4.2 유럽 CEN 기술표준(2016)
유럽은 IC 기술과 관련하여 오스트리아, 스웨덴, 독일 등 각국의 자체 기준이 있었으나, 2016년 유럽표준(CEN/TS 17006:2016)으로 통합되었다. 유럽표준화위원회(Comite Europeen de Normalisation, CEN)의 기술표준(Technical Specification, TS)에 진동롤러 기반의 연속다짐관리와 관련하여 상세하게 설명하고 있으며, 유럽에서는 지능형 다짐을 지칭하는 용어로 IC 보다는 CCC를 주로 사용한다.
진동롤러의 동적하중으로 다져지는 연속다짐관리는 롤러무게, 진폭, 주파수, 운행속도, 구동방향, 층두께, 흙의 종류, 세립분 함유량, 함수비 영향을 받기 때문에 운영 시 주의가 필요하다. 특히 포화도가 높은 세립지반에서 롤러의 동적하중은 흙의 유동성을 증가시켜서 측정값의 감소를 나타낼 수 있으므로 주의가 필요하다. 측정값(ICMV)의 정밀도를 위해서 IC 롤러의 진동주파수는 2Hz, 진폭은 0.1mm, 이동속도는 1km/hr 이내로 일정하게 유지해야 한다. ICMV는 길이 0.5 m 당 1회 이상의 빈도로 본시공에서 다짐도를 관리한다.
측정기준을 선정을 위해 길이 30m, 폭 10m 이상(길어깨 포함 3개의 레인)에 대해 시험시공을 수행해야 한다. 롤러 통과횟수를 다르게 조성한 시험지반에서 다짐도 및 지반강성을 측정하여 ICMV과의 회귀관계로부터 목표 측정값(TM)을 결정하며, 회귀분석의 결정계수(r2)는 0.7보다 크도록 데이터 정밀도 관리를 요구하는 것이 특징적이다.
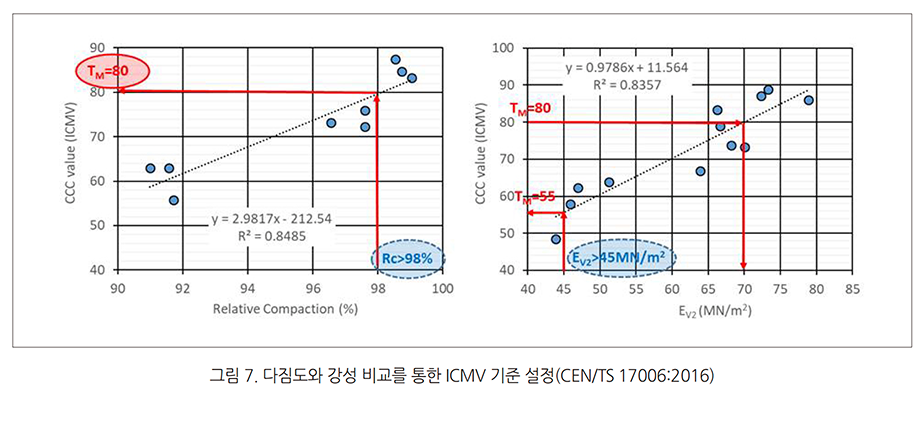
4.3 국내 기준(2021)
국내 기준도 타 기준과 동일하게 IC 롤러의 위치정보, 다짐횟수, 롤러의 진동과 진폭, 지반강성 등을 자동측정하고 전산화하는 것을 지능형 다짐공사로 정의하고 있다. 적용 대상은 시공면적 2,000m2 이상, 폭 8m 이상인도로, 철도, 단지조성 등의 노체 쌓기 및 노상 다짐으로한정하고 있다. 장비의 GNSS수신기는 다짐롤러의 위치에대한 ±50mm 이내의 정밀도를 요구하며, 롤러의 운행속도는 2~6km/hr, 진동주파수는 ±2.0Hz 범위에서 일정하게 유지할 것을 요구한다.
IC 관리기준 설정은 현장 시험시공(길이 80m, 폭 8m 이상)을 통해 결정해야 하며, 감독자가 승인한 3개소 이상의 위치에서 다짐횟수마다의 밀도 또는 지지력계수(타 기준은 강성 또는 탄성계수)를 평가 후 ICMV(전진 시)와의 회귀분석을 통해 결정한다. IC 관리기준 결정절차는 그림 8과 같이 타 기준에 비해 좀더 직관적으로 이해하기 쉽게 설명되어 있다. 우선 전통적인 다짐기준으로부터 목표 ICMV를 설정하고, 이를 기준으로 롤러 통과횟수를 결정한다. 본시공에서의 평균 ICMV는 기준값(목표 ICMV)의 105% 이상이 되도록 관리하고, 측정된 ICMV가 기준값의 70% 미만인 다짐경로가 전체경로의 10% 이하가 되도록 관리한다.
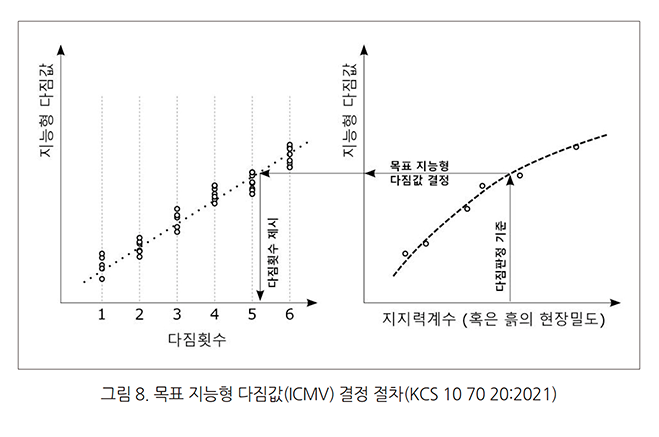
5. 최근 IC 기술 연구개발 동향
앞에서 IC 롤러 운전자의 다짐 진행여부 판단이 필요한 반자동식과 완전 자동화 방식에 대해 언급하였는데, IC 기술이 빠르게 변화하고 있는 최근에는 ‘높은 단계의 IC’에 가까운, 지능적인 운영이 가능한 IC 장비가 개발되고 있다. 비교적 최근(2020년)에 발표된 Dynapac社의 Seismic 시리즈의 10~12톤 롤러에 해당하는 CA2500D~3500D(그림 9)는 지반의 상태에 따라 IC 롤러가 최적의 주파수를 자동 결정하는 기술(주파수 조정 시스템)이 장비에 탑재되어 있다. 이 기능을 통해 지반의 동적 특성을 감지하고 최적의 다짐을 위한 드럼의 진동주파수를 계산한다. 0.2초마다 주파수를 유압으로 변경할 수 있는데, 이를 통해 다짐작업의 시간단축 및 비용절감이 가능하다. 제조사의 설명에 따르면, 해당 장비를 이용하여 과다짐, 과소다짐의 문제점를 해결할 수 있고, 연료 소비를 감소시켜 전체 생산성을 향상시킬 수 있다고 소개하고 있다. 또한 완전 자동화 주파수 제어시스템은 20Hz보다 낮은 주파수 영역에서 동작하게 하여 장비의 노이즈 수준을 감소시켜 소음문제도 개선 가능하다고 한다. 이와 같이 자동화된 IC 시스템은 다짐품질을 지속적으로 모니터링하고 취약한 부분을 효율적으로 해결하는데 도움을 줄 수 있을 것으로 기대된다.
최근 중국에서도 IC 기술에 대한 관심이 급증하여 관련 연구결과가 다수 발표되고 있는데, 그림 10에 나타낸 바와 같이, IC 롤러에스마트폰을 부착한 후 Non-Des-tructive Pavement Probe(NDPP)software라는 어플리케이션을 이용하여 다짐 중 아스팔트 다짐도 평가를 위한 데이터를 취득하는 연구가 최근 발표되었다(Zhang 등 2023). 이는 스마트폰에 내장된 가속도 센서 및 지자기장 센서를 활용하여IC 롤러를 운영하기 위한 정보를 취득하는 흥미로운 연구인데, 결과의 신뢰도에 대한 추가적인 검증이 필요하겠지만, 실용적인 IC 보급버전으로는 의미가 있다고 생각되며 향후 진행과정 및 추가 연구결과가 기대된다.
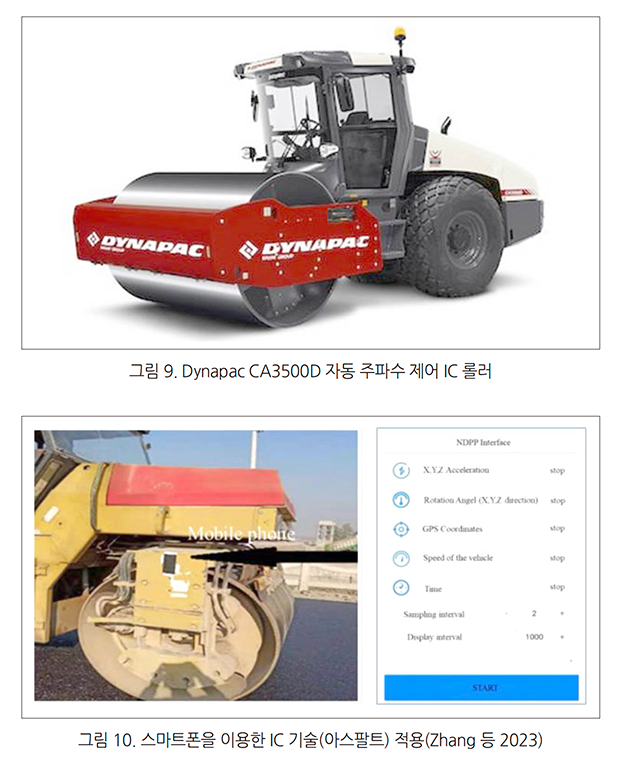
6. 결언
이상 살펴보았듯이, 각국의 기관들은 IC 기술 도입을 통해 토공사 중 리스크를 최소화하면서도, 균질하고 효율적인 시공품질 확보를 위한 건설기술의 자동화를 단계적으로 추진하고 있다. IC 기술의 장점을 요약하면, (1) 다짐품질 확보 및 균일성 향상, (2) 다짐상태의 시각적 확인을 통한 롤러 통과횟수 최적화, (3) 미다짐으로 인한 재작업과 관련된 품질시험 비용절감, (4) 시공 중 연약층을 즉시 식별하여 적기 재시공, (5) 최적화 운영에 따른 연료소비 절감 및 장비마모 감소, (6) 기초지반에 대한 역학적 특성 확보를 통한 시공 후 유지관리를 위한 기초 데이터로의 활용 등으로 정리할 수 있다.
실무에서 IC 기술을 적용하기 위해서는, IC 장비비가 약 3~5% 추가됨에 따른 비용편익을 고려해야 하며, OEM IC가 아닌 최근의 IC 장착키트를 사용할 경우에는 센서설치 및 검교정을 신중히 수행해야 한다. 또한, IC 롤러를 운전하는 작업자를 위해 장비 작동을 포함한 IC 기술에 대한 교육내용도 체계화해야 할 필요가 있다. 그리고, 국내의 IC 기준에서는 지지력계수와 ICMV와의 상관관계를 수립하도록 제시하고 있는데, 평판재하시험에 대한 지지력계수(K30) 보다는 다른 비파괴적인 시험법을 통한 동적 지반강성과 비교하는 것이 합리적이고 장기적인 비교연구에 도움이 될 것으로 생각한다. 또한, 시험시공과 본시공과의 시간차가 크지 않은 대부분의 국내 현장여건을 고려할 때, IC 시공관리 기준을 현장에서 신속하게 결정하기 위해 LWD, SSG와 같은 디지털화된 비파괴 지반강성 측정장치의 활용이 필요하다. 그리고, 신기술 활용 독려를 위한 인센티브 제공 및 발주처의 시험시공 결과승인을 위한 프로세스 소요시간을 단축시킬 수 있는 제도적인 뒷받침이 있다면 IC 기술도입 및 운영에 도움될 것으로 생각된다.
최근의 센서기술 및 모바일 데이터처리 기술이 발전하고 있는 환경에서, 토공분야의 IC 기술은 스마트 건설의 중요한 역할을 할 수 있을 것이라고 생각한다. 토공 자동화를 위한 이용 측면뿐만 아니라 공사 중 수집되는 수많은 데이터의 공학적 활용에 대해서도 고려해볼 수 있다. 특히 IC 롤러는, 그림 11에 나타낸 바와 같이, 여타 다짐특성 측정법에 비해 영향범위가 크기 때문에, 다짐에너지 지중전파와 관련한 효과적인 검증툴로 활용할 수 있는 잠재성이 있다. 이를 이용해서, 토공장비의 규모와 성능이 과거에 비해 확연하게 달라졌음에도 불구하고 여전히 수 십년째 사용중인 20cm 내외의 성토두께 규정을 개정하고자 하는 토공분야의 숙원사업(?)에 대한 해결책을 IC 기술이 제공할 수 있지 않을까 하는 조심스러운 기대를 해본다. IC 기술에 대한 추가적인 연구 및 현장 실증결과가 앞으로 현업에 널리 전파되어서 국내 토공현장의 생산성을 높이는데 기여했으면 하는 바램이다.
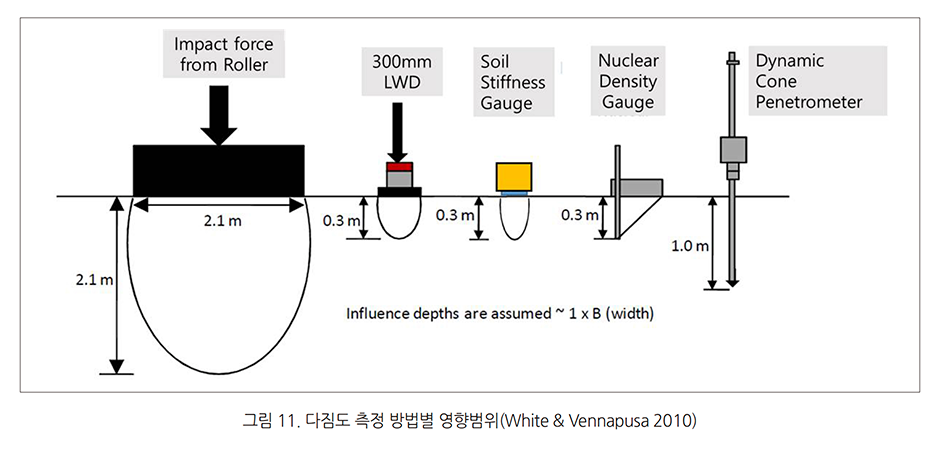
참고문헌
1. KCS 10 70 10(2023), 머신가이던스 및 머신컨트롤 시공 일반: 공통공사 표준시방서, 국토교통부.
2. KCS 10 70 20(2021), 지능형 다짐공: 공통공사 표준시방서, 국토교통부.
3. CEN/TS 17006(2016), Earthworks-Continuous Compaction Control (CCC), The British Standard Institution.
4. Chang, G. et al.(2011), Accelerated Implementation of Intelligent Compaction Technology for Embankment Subgrade Soils, Aggregate Base, and Asphalt Pavement Materials, Final Report FHWA-IF-12-002.
5. FHWA(2014), Intelligent Compaction Technology for Soils Applications, Generic - IC Specification for Soils.
6. Forssblad, L.(1980), “Compaction meter on vibrating rollers for improved compaction control”, Proc., Int. Conf. on Compaction, Paris.
7. Mazari M. et al.(2021), Developing Guidelines for Assessing the Effectiveness of Intelligent Compaction Technology, Report 20-56, Mineta Transportation Institute.
8. Mooney, M. and Adam, D.(2007), “Vibratory roller integrated measurement of earthwork compaction: An overview”, Proc., 7th FMGM 2007: Field Measurements in Geomechanics.
9. Mooney, M. et al.(2010), Intelligent Soil Compaction Systems, NCHRP Report 676, Transportation Research Board.
10. Nazarian, S. et al.(2015), Intelligent Compaction Roller Retrofit Kit Validation, Final Report FHWA TIDP-130 (096).
11. Thurner, H. and Sandstrom, A.(1980), “A new device for instant compaction control”, Proc., Int. Conf. on Compaction, Paris.
12. White, D.J. et al.(2009), Implementation of Intelligent Compaction Performance Based Specifications in Minnesota, Final Report MN/RC 2009-14.
13. White, D.J. and Vennapusa, P. KR.(2010), A Review of Roller-Integrated Compaction Monitoring Technologies for Earthworks, Final Report ER10-04.
14. Zhang, W. et al.(2023), “In-Time Density Monitoring of In-Place Asphalt Layer Construction via Intelligent Compaction Technology”, J. Mater. Civ. Eng., 35(1): 04022386.
[본 기사는 저자 개인의 의견이며 학회의 공식 입장과는 관련이 없습니다]
인입식 PBD, RCP 공법으로, 연약지반 위 구조물이 안전해지다
전 찬 민
(chan@engjournal.co.kr)
연약지반은 구조물의 기초지반으로써 충분한 지지력을 갖지 않은 지반 특성을 가지고 있다. 기초지반은 구조물의 하중을 지반이 견딜 수 있도록 조성돼야 하기 때문에 연약지반 위에 구조물을 건설하기 위해서는 견고한 기초지반으로 연약지반을 개량하는 것이 매우 중요하다.
아무리 튼튼하게 지어진 건물이라 하더라도 견고하지 못한 지반 위에 지어진 건물은 약한 외부 하중 변화에 쉽게 기울어지거나 무너질 가능성이 높다. 실제로 건설 현장에서 지반에 대한 정보가 부족해 지반 사고가 빈번히 발생하고 있으며 특히, 간척 매립지나 유수에 의해 형성된 연약한 퇴적층이 발달한 우리나라에서는 지반에 대한 이해가 절실한 실정이다.
연약한 지반을 견고한 지반으로 개량하기 위한 방법으로는 대표적으로 압밀을 촉진하는 방법과 모래나 쇄석을 지중에 치환하는 방법이 있으며, 그 외에도 시멘트를 경화해 고결시키는 방법 등이 활용되고 있다.
압밀을 촉진하는 방법의 경우, 플라스틱 보드 드레인(PBD)을 지중에 설치해 무른 땅을 견고하게 하는 방법이 있다. PBD 공법은 장비가 간편하고, 시공 속도가 빠르며, 자재비가 비교적 저렴할 뿐만 아니라 지반 교란이 최소화되기에 점차 사용량이 증가하고 있는 공법으로 활용되고 있다.
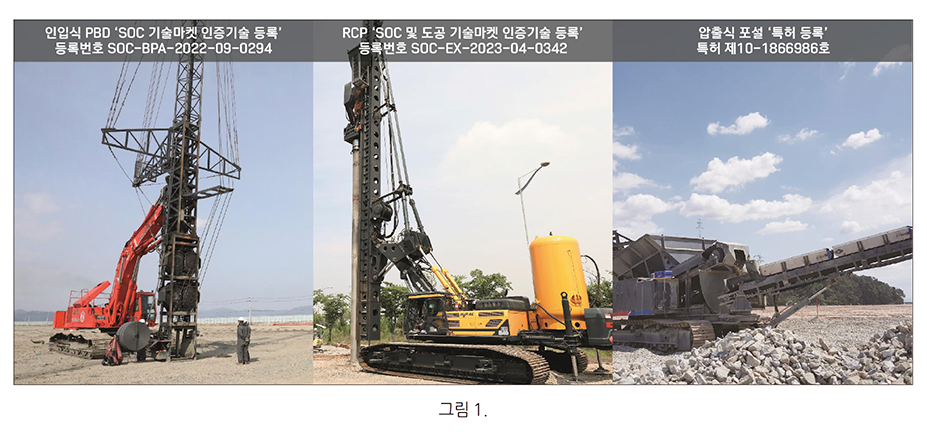
하지만, 설치 도중 국부적으로 다져진 매립층이나 견질의 모래층 등 상대적으로 단단한 지층을 만나면 배수재의 관입이 곤란한 경우가 많아 기존에는 이러한 층을 선행천공하거나 여타 다른 비싼 공법을 고려해야만 했다.
이에 따라 기존 PBD 공법의 한계를 해결하고자 인입식 PBD 장비가 개발돼 주목을 받고 있다. 이 장비를 개발한 주인공이 바로 ㈜미래지반연구소다.
연약지반 개량 전문기업 미래지반연구소가 개발한 ‘인입식 PBD 장비’는 기존 장비의 문제점을 보완해 보다 효율적인 압입 효과를 발휘할 수 있도록 개선했고, 작업속도도 기존 공법보다 동일하거나 더 빠르게 개선했다. 또한, 선행천공 없이 PBD 시공을 함으로써 지반 교란 영역(Smear Zone)이 최소화될 수 있어 지반에 더 유리하게 설계됐다는 것이 특징이다.
뿐만 아니라 정보화 시공이 가능하도록 전자센서를 부착해 지층의 연약 정도, 천공 심도, 연직도, 관입 저항치를 측정하고 확인할 수 있어 시공성, 품질관리 측면뿐만 아니라 장비의 안정성도 확보했다. 신규 장치의 경우 하부 리더는 사각형 구조, 상부 리더는 삼각형 구조로 중량을 기존 장비 대비 약 25% 정도 감소시켰으며, 케이싱은 내마모강의 자재(AR-500)를 사용해 케이싱의 중량을 30% 감소시키고, 강도를 최적화시켰다.
인입식 PBD는 부산신항, 새만금 도로공사 등 여러 현장에 적용됐으며, 이러한 성과를 바탕으로 그 우수성을 인정받아 지난 2022년 9월 SOC 기술마켓(SOC-EX-2023-04-0342)에 등록됐다.
한편, 연약지반에 모래 또는 자갈 기둥(SCP/GCP)을 형성하는 기존 장비들은 일본에서 일반적으로 사용하던 형식으로 기중기를 개조한 장비를 활용하고 있다. 하지만, 이처럼 기중기를 개조하고, 바이브로 해머를 장착한 장비는 성능뿐만 아니라 전도의 위험성, 건설 환경(진동·소음) 면에서 많은 문제를 가지고 있다.
이에 따라 공사 현장 환경 개선 인식이 확대되면서 새로운 장비에 대한 요구가 증대됨에 따라 미래지반연구소는 무진동·저소음 장비를 이용해 자갈 또는 모래를 다짐해 기둥을 형성하는 ‘RCP(로타리식 쇄석 또는 모래 다짐말뚝) 공법’을 개발했다.
RCP 공법의 장비는 오거형 타입으로 무진동 시공이 가능하기 때문에 케이싱 내 재료 분리를 최소화해 연약지반에 보강재를 효과적으로 다짐할 수 있고, 우수한 관입력으로 원하는 설계 심도까지 시공이 가능하다는 것이 장점으로 손꼽히고 있다.
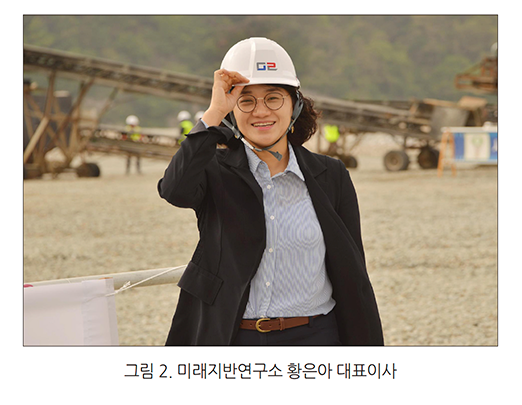
미래지반연구소 황은아 대표이사(그림 2)는 “비자주식이었던 기존 장비와 달리 RCP 공법의 장비는 자주식 리더로 리더를 자체 자립 및 하강할 수 있어 안전상 위급한 상황 시 대처가 용이하고, 트랙식 강제승강장치에 의한 리더 연직도 관리도 우수하다”라며 “특히, 스마트 건설에 발맞춰 디지털 자동기록장치를 개발해 자재 투입량, 심도, 리더 각도 등의 시공 상태를 실시간으로 확인할 수 있으며, 저장된 데이터들을 통해 스마트 품질관리까지 가능하다는 것이 특징”이라고 말했다.
그는 이어 “무엇보다 RCP 공법의 가장 큰 장점은 무진동·저소음 시공으로 건설 환경이 개선돼 간섭구간에 문화재, 축사, 도심, 주거시설이 있어도 현장에 적용이 가능하다는 점이다”라며 “이 장비는 새만금~전주간 고속도로 개설공사 현장에서 본격적으로 적용돼 순수 국내 기술로 만들어낸 RCP 공법의 기술력, 안정성, 시공성, 건설 환경 등을 인정받았다”라고 말했다.
이러한 기술력을 토대로 2023년 02월 도공 기술마켓 인증기술(기술추천-2022-0212), 2023년 04월 SOC 기술마켓 인증기술(SOC-EX-2023-04-0342)에 등재되며 개발 기술인 인입식 PBD 공법과 RCP 공법 모두 SOC 기술마켓에 등록되는 남다른 행보를 이어나가고 있다.
이처럼 미래지반연구소는 지난 2005년 1인 기업으로 시작해 연약한 지반에 대해 조사에서 설계, VE 검토, 시공(개량공사), 토목·계측·유지관리까지 연약지반의 모든 것을 책임지고 수행하고 있다. 특히, 직접 개발한 장비와 공법으로 단지 조성, 항만, 도로 등 공사 현장에서 연약한 퇴적층을 견고한 기초지반으로 개량하는 작업을 수행하고 있으며, 엔지니어 사업부를 별도로 두어 현장에서 시공 중에 발생할 수 있는 문제점을 미연에 보완·제거하고, 준공 이후에도 시설물 유지관리가 가능한 체계를 갖춘 기업으로 꾸준히 성장해가고 있다.
최근에는 연약 또는 초연약지반 상에 매우 느슨한 모래나 유동화된 점토 등을 준설해 대규모 항만 부지 또는 물류단지, 산업용 부지를 확보하기 위한 해안 매립 공사가 활발하게 이뤄지고 있어 압출식 포설 장치에 대한 개발을 서두르고 있다.
준설토는 일반적으로 함수비가 매우 높고 유동성이 크며 고압축성을 갖는 경우가 많아 준설 매립 지반을 개량하기 위해서는 인력과 장비의 진입을 위한 표층처리공법의 적용이 필수적이다. 하지만, 기존 방식들은 효율이 낮거나 준설토 표층의 소성변형을 수반하는 장치를 이용해 왔다.
이에 미래지반연구소는 작업 효율과 소성변형 억제책을 고민하다가 ‘압출식 포설 장치’를 개발하게 됐다. 압출식 포설 공법은 접지압을 최소화한 포설장치를 이용해 포설 각도, 포설량, 포설 거리 조절이 자유로운 수평배수재 포설 방법으로 무인 제어장치로, 그 원리는 장비 진입 전 원거리에 압성토 시공을 해 연약지반 매트(P.P Mat)를 구속시키고 점진적으로 근거리를 포설함으로써 연약지반의 소성 유동을 최소화하는 방법이다.
또한, 원거리(30~50m)에서 근거리로 점진적 포설을 해 안정적인 단면 형성이 가능함에 따라 균등한 포설 두께를 형성할 수 있고 시공 중 지반침하량이 거의 균등하게 발생해 부등침하에 따른 문제점을 해결할 수 있다.최근 부산항 신항 서컨 준설토 투기장 표층 처리 공사 현장에서 압출식 포설기로 시공한 결과 쇄석 포설 시 소성유동이 거의 발생하지 않으며, 균등 포설이 가능한 것을 입증하였고, 현재 접지압 향상을 위한 개선 작업이 한창 진행 중이다.
황 대표는 “현재 가덕도 신공항 프로젝트는 형성하고자 하는 지형이 연약한 바다에 위치하고 있어 연약지반 처리가 필수적”이라며 “이를 효율적으로 수행하기 위해서는 해상에서 연약지반처리를 하고 매립하는 동안에 압밀침하량이 목표치에 도달하게 함으로써 공사기간 단축, 공사비용 절감을 꾀할 수 있어 미래지반연구소는 해상PBD와 관련해 기술 개발에 박차를 가할 계획”이라고 말했다.
출처 : 공학저널(http://www.engjournal.co.kr)
http://www.engjournal.co.kr/news/articleView.html?idxno=2423
[본 기사는 저자 개인의 의견이며 학회의 공식 입장과는 관련이 없습니다]